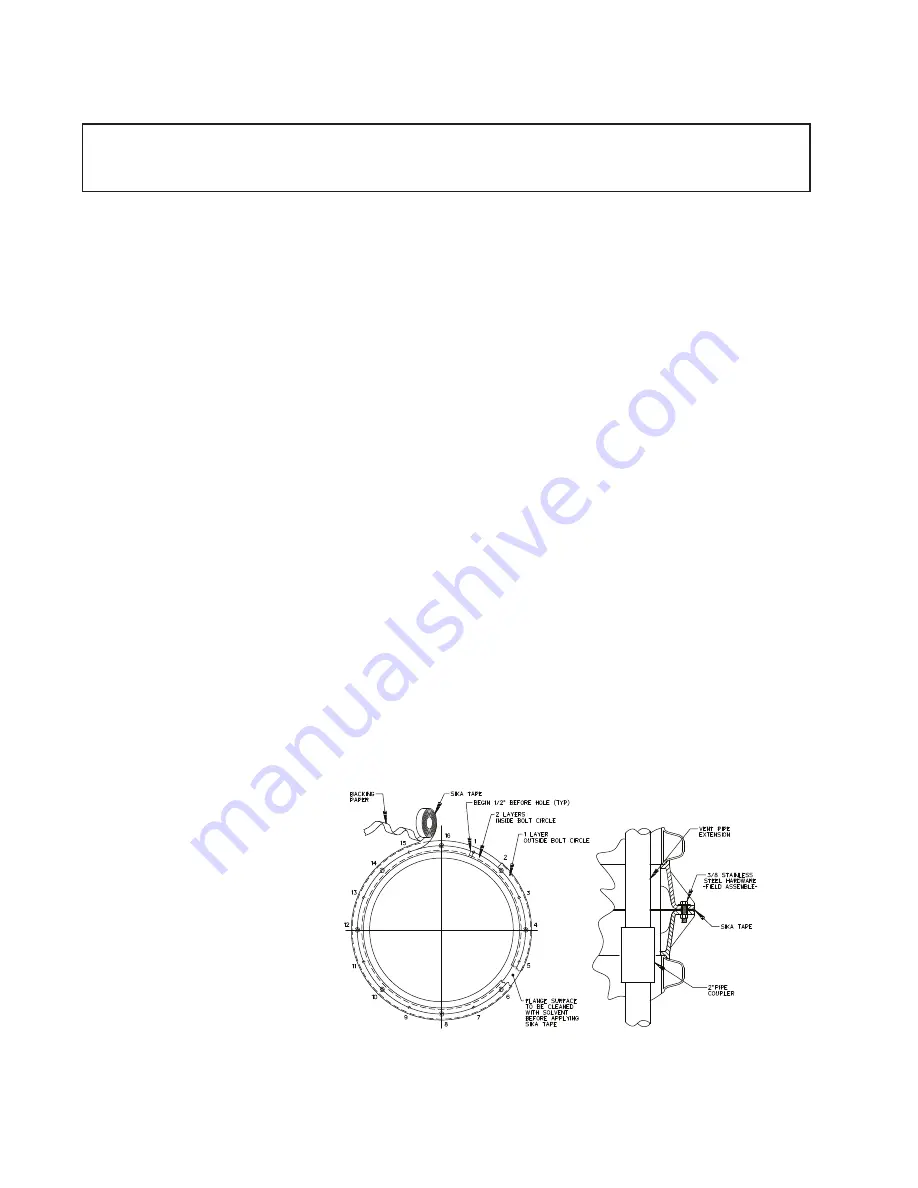
8
Field Joint Assembly Instructions
Parts included in Field Joint Kit:
Identify all parts before proceeding
with installation.
(16) 3/8-16 x 1-1/2 long screws
(16) 3/8-16 Elastic Stop Nuts
(32) Flat Washers
(1) Length Sealant (Sika) Tape
(1) Hole Punch
(1) Vent Pipe Extension
1) Carefully clean and dry both
accessway flanges with solvent.
IMPORTANT: Sealing surfaces
must be dry to ensure the
sealant adheres correctly.
2)
Starting at one hole of tank
flange, apply two layers of Sika
Tape around the inside half of the
flange. Align the outside edge of
the tape with the bolt circle. Move
to the adjacent hole and apply
one layer of Sika Tape around
the outside of the flange. Align
inside of tape with the bolt circle.
Remove the backing paper as you
lay the adhesive on the flange.
Do not stretch Sika tape during
application; it may result in a
leak.
The tape should overlap at
the end by approximately 1/2 inch,
as shown in Fig. 5a. If a section
of Sika Tape is misapplied, the
bad section may be cut out and
replaced. Cut away the poorly laid
portion cleanly with a knife and be
sure to over lap the tape at each
end about 1/2 inch.
3) Using the tool provided,
punch a hole through the tape at
each of the 16 existing bolt holes
in the flange.
Be careful to keep
the exposed sealant clean and
dry.
4) Insert three of the sixteen 3/8-
16 x 1-1/2” long bolts, with a flat
washer, into the flange attached to
the upper part of the accessway.
These will act as guides while
aligning the bolt pattern of the two
flanges.
5) Support the upper accessway
section a few inches over the
tank, making sure to align the vent
port in the lid with the vent pipe
in the tank. Once aligned, lower
the upper section onto the mating
flange using the three bolts to
guide it to the proper position. See
Fig. 5b.
6) Insert the remaining 13 bolts
with flat washers into the flanges.
Place a flat washer and elastic
stop nut on the end of each bolt,
turning the nut on just enough to
hold the washer in place.
7) Tighten the bolts until the
sealant begins to squeeze out
from between the flanges. To
ensure a consistent, sturdy seal,
tighten them in the following
sequence: 1, 9; 5, 13; 3, 11; 7, 15;
2, 10; 4, 12; 6, 14; 8, 16. Always
be sure to tighten one bolt and
then the bolt at the position 180°
from it; see Fig. 1 for position
numbers.
8) Using the same sequence as
in Step 7, tighten each bolt to 60
in-lbs. Visually inspect the joint,
each bolt and each nut should
have a flat washer between it and
the flange, and a uniform amount
of sealant should be protruding
from the seam along the entire
perimeter.
In the event that there are
any voids in the sealant, the
joint may leak. Take corrective
actions if necessary and be
sure that the joint is leak free
before continuing.
9)
In order to properly vent
the station, apply PVC primer/
cement (not provided) and
assemble the included sections
of vent pipe by using the
provided 2” PVC couplings.
After the pipe sections have
been assembled, ensure that
the bottom end of the pipe
is secured in the lower vent
grommet, then slide the top
end of the pipe through the
receptacle on the bottom of the
lid.
IT IS EXTREMELY IMPORTANT THAT THE JOINT IS SEALED PROPERLY BEFORE
BACKFILLING. EXCAVATING A UNIT FOR REPAIR IS VERY EXPENSIVE AND CAN BE EASILY
AVOIDED BY USING PROPER CAUTION DURING THE FOLLOWING PROCEDURE.
Figure 5a
Figure 5b