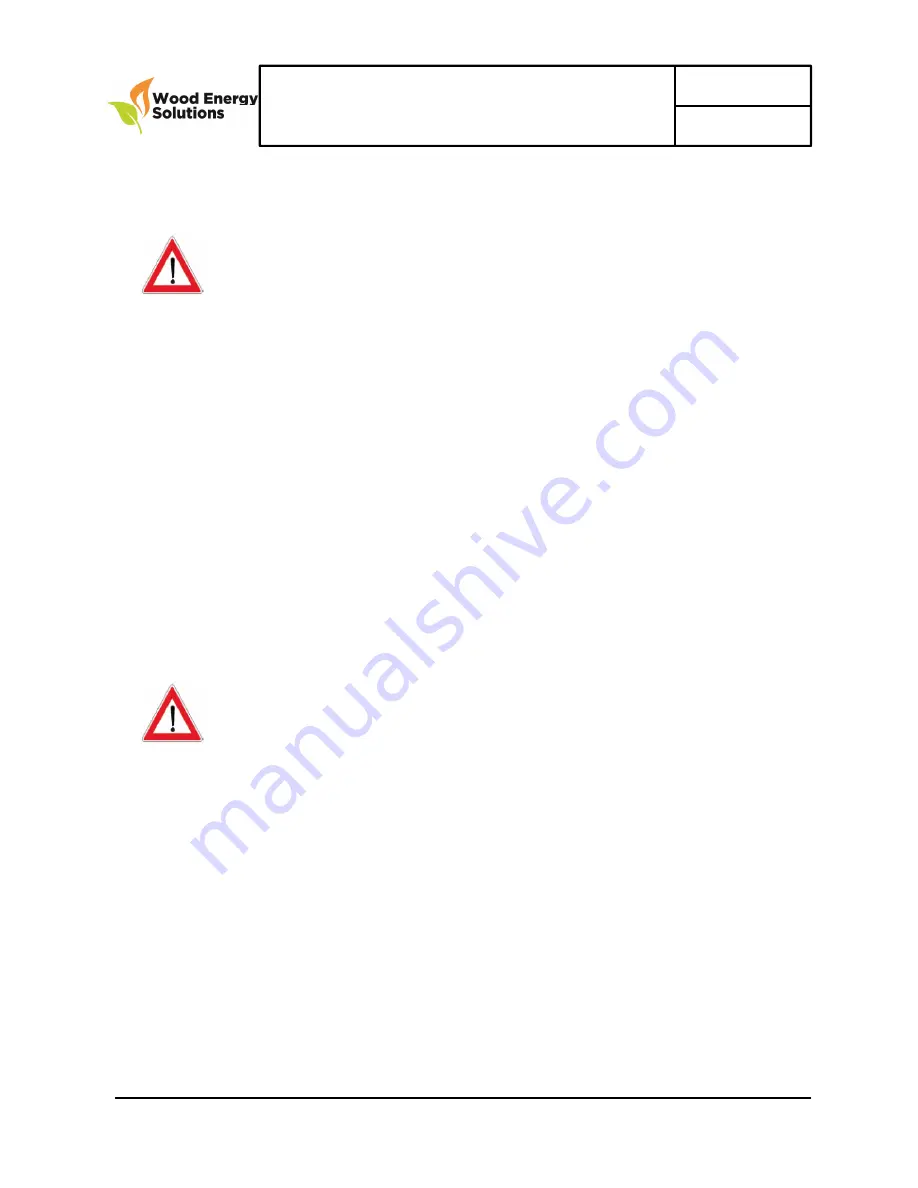
3.6 PLUMBING CONNECTIONS
IMPORTANT!
The connection of the boiler to the plumbing system
must be carried out ONLY by specialized personnel who
are capable of carrying out installation properly, in
compliance with current standards in the country of
installation.
If installation of the boiler will involve interaction with
another, pre-existing system complete with heating
equipment (gas boiler, methane boiler, fuel oil boiler,
etc.), it is even more advisable to call in qualified
personnel, who subsequently will be responsible for
conformity of the system with current applicable law.
WES will not be held responsible for damage to persons or things in
the event of failed or incorrect operation if the aforementioned
warnings are not complied with.
For connection of the plumbing system to the appliance, the user
should refer to chapter 4, INSTALLATION AND ASSEMBLY; specifically,
paragraph 4.5, CONNECTION TO PLUMBING SYSTEM.
ECOMPACT Slim
Page 12
Pre-Installation Considerations
© Wood Energy Solutions
woodenergysolutions.co.uk
It is recommended that a suitable anti-freeze
solution is added to the heating system to prevent
the freezing of water within the boiler in the case of
a power outage. The boiler has an anti-freeze
function which activates the pump in the event of
the temperature in the boiler dropping below 5
°
C.
Summary of Contents for 15
Page 2: ......