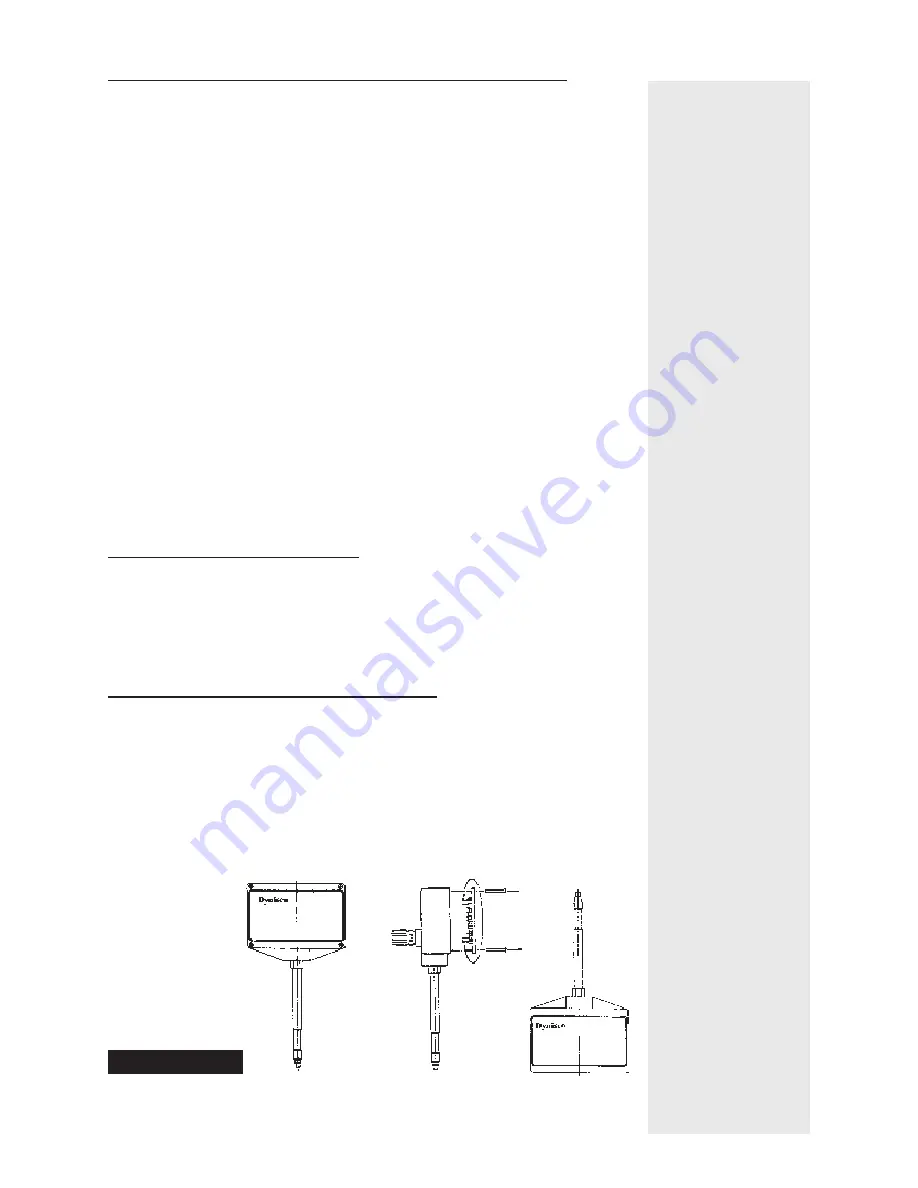
DYNISCO PG500 Series
3
33
3
3
3
33
3
3
2.
INSTALLATION
After lubricating the probe thread as described, install the probe in the
mounting hole with the hex nut provided at the top of the probe.
• DO NOT ATTEMPT TO SCREW UNIT IN BY TWISTING GAUGE
ENCLOSURE.
A mounting torque of 100 inch lbs. should provide an adequate seal,
although the stem will withstand up to 500 inch lbs.
*A mounting hole which has become damaged, distorted or partially
filled with plastic can render a gauge inoperative as easily as one which
is not properly machined.
*A cleaning tool kit (Dynisco P/N 200100) is available which is
designed to remove excess plastic from the 0.312 diameter hole, the
45° seat, the 0.451 diameter and the threads. A gauge plug is
included in this kit.
2.1
Gauge Enclosure Rotation
Once installation has been completed, the gauge enclosure can be
swiveled 310° to provide optimum visibility. To do this, rotate the
enclosure to the desired position. Do not attempt to force enclosure
rotation beyond the built-in mechanical stops.
2.2
Stem Up - Stem Down Modification
All PG500 Series gauges are shipped from the factory in a stem down
configuration (Figure 5). For those installations which require a stem
up configuration, (mounting on bottom of extruder barrel) merely
remove the four corner screws on the gauge face and gently lift the
face plate off (Figure 5). Reinstall face plate upside down and re-
tighten corner screws.
Fig. 5