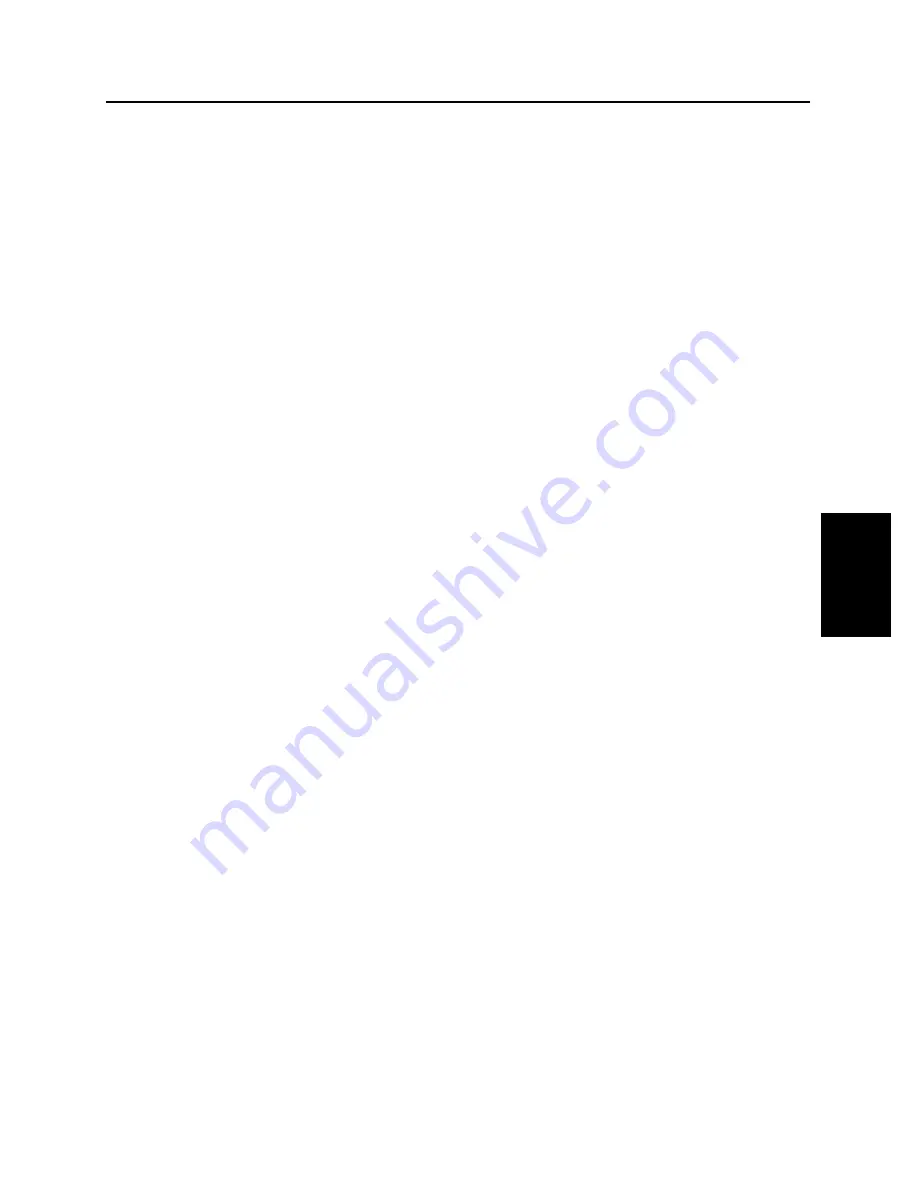
Ancillary Machine Controls
4-5
Function of
Controls
Pneumatic Rebound Brake Connection (Pneu Rebound Brake)
The Pneu Rebound Brake connection is located on the left side panel of the Model 8250's
motor enclosure (see Figure 3-3).
This connection is used when the pneumatic rebound brake is installed on the Model
8250 and allows the Model 8250 to automatically reset the rebound brake after each test
sequence. Consult the Pneumatic Rebound Brake Manual for specific installation
instructions.
Pneumatic Clamp Pressure Regulator (Clamp Air Pressure)
The Clamp Air Pressure regulator is located on the left side panel of the Model 8250's
motor enclosure (see Figure 3-3).
If the Model 8250 is equipped with a pneumatic clamp, the pressure regulator can be used
to vary the amount of force applied by the clamp in securing the test specimen. The
amount of force applied is calculated by multiplying the value observed on the pressure
gauge by 6.47 to obtain the value in pounds, or by 28.75 to obtain the clamping force in
Newtons. For best function, the pressure should be set above 20 psi and the maximum
pressure should not exceed 100 psi.
The pressure regulator will have no effect on the pneumatic clamp unless the Clamp
On/Off button on the pendent is set to ON.
Pneumatic Assist Pressure Regulator (Pneumatic Assist Air Pressure)
The Pneumatic Assist Air Pressure regulator is located at the back of the Model 8250 on
top of the motor enclosure.
The regulator and gauge combination is used to vary the velocity of the crosshead when
the test machine is in pneumatic mode (GRAV/PNEU switch set to PNEU). The
maximum air pressure setting is 85 psi. The maximum velocity obtained is dependent on
the combination of fixturing and crosshead weight. Under no circumstances should the
heavier crosshead assemblies (greater than 50 lbs.) be accelerated above 14.5 ft/sec.
To adjust the knob for a desired velocity:
(a)
Turn the regulator knob until the gauge reads 40 psi.
(b)
Initialize the Instron Dynatup data system and access the VELOCITY command
(see the Data System Manual for details of the velocity command).
(c)
Fire the crosshead and observe the reported value for the velocity obtained.
(d)
If the velocity was lower than the desired value, increase the pressure supplied to
the pneumatic assist by turning the regulator knob clockwise. If the velocity was
higher than that desired, turn the regulator knob counter-clockwise. Observe the
gauge while turning the regulator knob. Large increases or decreases in pressure
correspond to large increases or decreases in velocity.
Summary of Contents for 8250
Page 1: ... M14 13655 EN Operating Instructions Instron Dynatup 8250 Drop Weight Impact Tester ...
Page 10: ...Preliminary Pages M14 13655 EN x ...
Page 29: ...Connecting Utilities and Initial Set up 3 7 Installation Figure 3 3 Motor Enclosure ...
Page 34: ...Initial Machine Operation and Checkout M14 13655 EN 3 12 ...
Page 49: ...6 1 Operation Chapter 6 Chapter 6 Operation Outline Performing a Test 6 2 ...
Page 54: ...Performing a Test M14 13655 EN 6 6 ...
Page 58: ...Scheduled Maintenance M14 13655 EN 7 4 Figure 7 1 Lubrication Points LUBRICATION POINTS ...
Page 62: ...Troubleshooting M14 13655 EN 7 8 ...
Page 64: ...Glossary M14 13655 EN A 2 ...