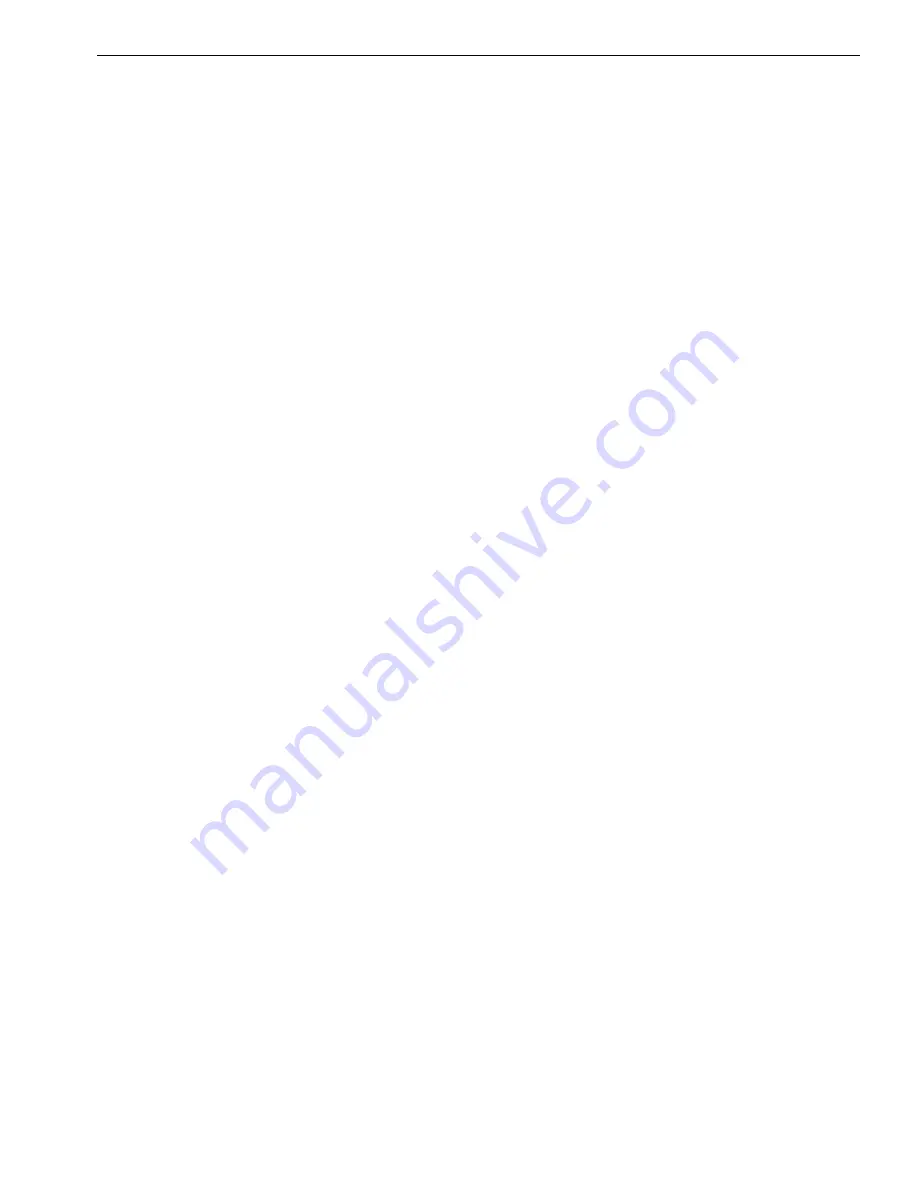
Installation, Operation and Service Manual
LKP Series 4 Channel OEM
© 2019 DynAmp, LLC
Page 11
041593O
E.
When mounted, the two head halves of the Measuring Head should be in the same
plane so no distortion of the part-line will occur. No tension, twist, or excessive pressure
should be applied to the part line.
F.
The Measuring Head should be electrically insulated from the bus. A 6mm (1/4”)
minimum distance between the bus and window insulation should be maintained in dry,
clean air. More separation should be maintained if the bus voltage is greater than 1000
Volts or if the air quality is bad. This will insure electrical isolation of the head structure
from the bus.
The aluminum head structure is grounded via the cables to the
Metering Unit. Do not short between the head structure and the bus to prevent
serious damage or injury.
For that reason, always disconnect the cables from the
Measuring Head prior to installation or maintenance. Touching both an energized bus
bar and grounded Measuring Head may result in electrical shock.
Most models interconnection cables have a GRN/YEL wire that is used for Measuring
Head grounding. To electrically float the Measuring Head above ground potential, the
GRN/YEL wire from each cable must be disconnected at the Metering Unit. Note that
for safety reasons, the metering unit cabinet should be grounded at all times.
G.
Do not loosen any of the bolts that hold the Measuring Head casting sections together.
Doing so, will compromise the seal between parts and allow water or contaminants to
enter the Measuring Head.
H.
The Measuring Head must be installed with current arrows in the same direction as
conventional current flow in the bus. An arrow indicates the direction that conventional
bus current must flow through the aperture (+ to -). No damage will occur if the
Measuring Head is reversed, but an LKP system will not produce an output in this
condition.
CAUTION:
The part-line insulation pieces (located on the mating surfaces of the
Measuring Head) contain sensitive electronic devices, are brittle, and can be easily
damaged if one is not careful during installation.
I.
Make sure that the serial number on the top half of the Measuring Head matches the
serial number of the lower half, and that the halves go together squarely and evenly
without forcing, twisting, or cocking.
J.
Try to mount the Measuring Head in an area free of other bus bars. This is not an
essential requirement if a satisfactory magnetic centering can be achieved.
K.
Final Measuring Head position will be determined by the magnetic centering process, so
the head support members should be temporary at first. If a bus analysis has not been
performed, the Measuring Head should be geometrically centered on the bus during the
initial installation. If a bus analysis was performed, follow the recommendations for initial
positioning, and also perform the centering process.
L.
After final magnetic centering, the Measuring Head must have adequate support.
Sudden changes or shutdown of bus current can induce high voltages in open coil circuits
inside the Measuring Head. This is a risk of shock if someone is in contact with the connector
pins during the event. There is a slight possibility of connector or coil damage if the Measuring
Head is left un-operation (stored) for prolonged periods on a live bus with frequent fluctuations.
The following precautionary measures must be taken to prevent damage and risk of shock.
Best option is to leave the cables connected between Metering Unit and Measuring Head.
Even if the Metering Unit is not powered, it will shunt induced currents in the coil and prevent
high voltage from developing. If that is not feasible then use one of the following options: