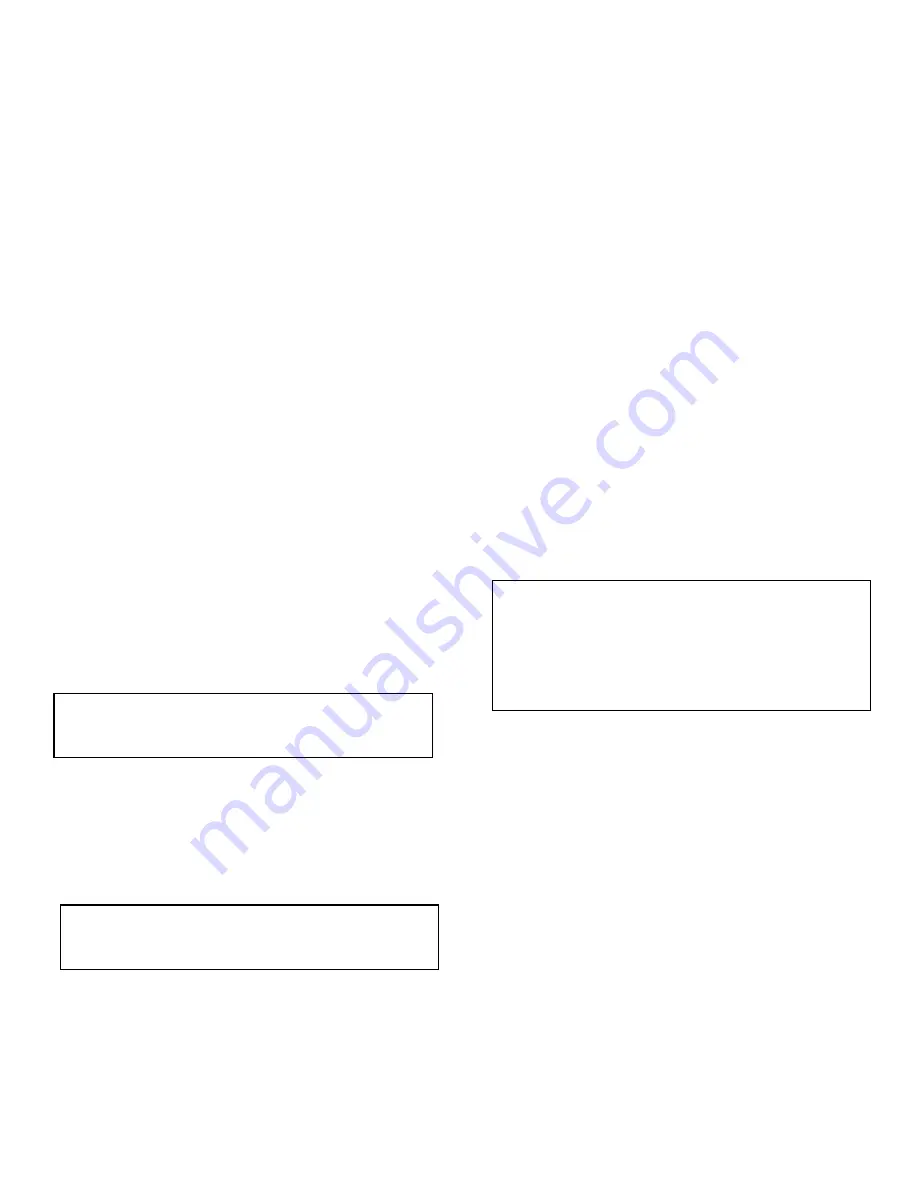
35
Section 7
Service & Renewal Parts
DSI/Dynamatic® provides a total service program to
ensure your satisfaction with its products by maintaining
an Aftermarket Sales & Service Department which offers
the following services to you: Technical Assistance, Field
Service, Training, Factory Repair Service and Renewal
Parts.
The Company also maintains a world-wide network of
Authorized Service Centers, Major Parts Distributors,
Drive Distributors and Field Service Engineers. For
locations of those nearest you, contact DSI/Dynamatic®
at 262-554-7977 or toll free at 1-800/548-2169.
Field Service
Trained service engineers, located at the factory and in
key industrial centers around the world, are available to
provide technical assistance to you. These engineers
provide technical advice and counsel relating to the
installation, maintenance, adjustment, modification and
repair of the equipment.
This assistance may be offered over the telephone or, if
required, by a trip to your plant. Requests for field service
assistance should be made through the Field Service
Department in Sturtevant, Wisconsin.
Repair Service
Repair and overhaul or rebuild services are provided by
the Repair Service Department at the Sturtevant factory.
These services are also available through Authorized
Service Centers located in key industrial centers around
the world.
Note
: All warranty work must be approved and
authorized by the Field Service Department at the
factory.
Any non-warranty item returned will be repaired on a time
and material basis if deemed repairable unless a fixed
quotation is requested before authorizing the repair.
Contact the Repair Services Manager at the factory for
quotations at: 1-800/548-2169.
Return Instructions
Items being returned for repair, including warranty repairs,
require a Repair Instruction (RI) Form. Contact your local
Sales Office for the form and return
authorization. Provide all the information requested on the
form and return it with the equipment and your purchase
order.
Those items not manufactured by DSI/Dynamatic® such
as instruments, meters and digital counters, are repaired
by the vendor. Returning them to the factory will only
delay the repair. Contact the Repair Service Department
at the factory for shipping instructions.
Any return for reasons other than repair requires a Return
Authorization (RA) form, available from your local Sales
Office or the factory.
Repair Instructions
Customers wishing to repair or overhaul Ajusto-Spede®
drives should contact DSI/Dynamatic® to obtain detailed
instructions, bills of material, specifications and drawings.
To ensure that the correct information is furnished, the
model number, PRO number and serial number must be
obtained from the nameplate of the specific unit for which
information is being requested.
Renewal Parts
Contact the factory in Sturtevant, WI to place orders for
renewal parts.
Note
: To ensure that correct parts are furnished,
include complete nameplate data from your specific
unit, a purchase order number, description of the part
and the quantity required. The nameplate lists the
model number, PRO number and serial number.
These numbers are necessary to identify the units and
to establish the correct parts for your unit(s).
Renewal parts will be shipped from the distributor's stock,
from factory inventory or will be manufactured on receipt
of an order, depending on availability. Inventory quantity
and location is based on the level of demand for individual
items. Renewal parts are covered by the standard
renewal parts warranty, as published in the Company
Terms and Conditions of Sale for Renewal Parts.
Lists of recommended spare parts, complete parts lists
and other renewal parts information are available on
request.
Note
: Do not return any item to the factory without
authorization. Comply with the "Return Instructions"
that follow.