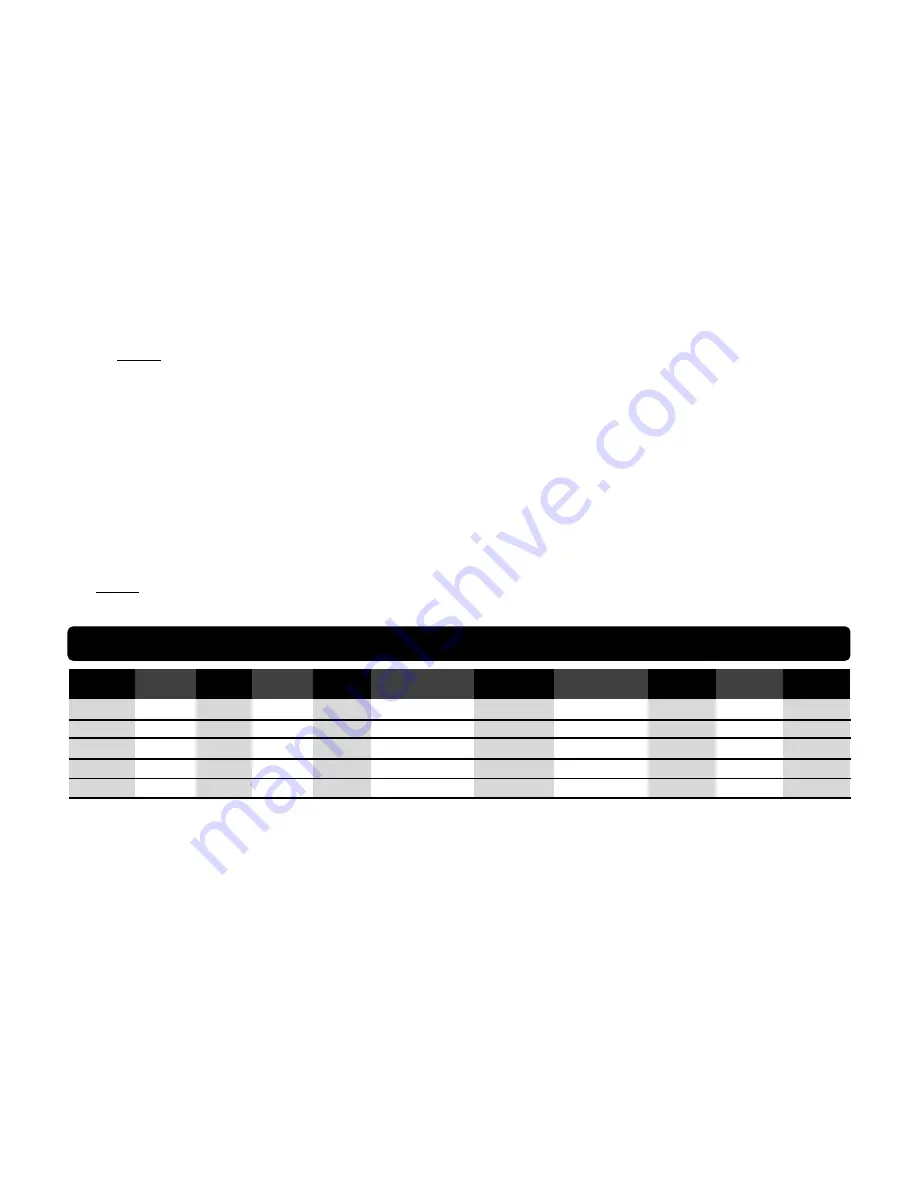
Maintenance Instructions
Important:
To keep tool safe a preventative maintenance program is recommended whenever portable power tools are used. The program should include
inspection of air supply lines, air line pressure, proper lubrication and repair of tools. Refer to ANSI B186.1 for additional
maintenance information.
•
Use only genuine Dynabrade replacement parts to insure quality. To order replacement parts, specify
Model#
,
Serial#
and
RPM
of your air tool.
•
It is strongly recommended that all Dynabrade rotary vane air tools be used with a Filter-Regulator-Lubricator to minimize the possibility of misuse due to
unclean air, wet air or insufficient lubrication. Dynabrade recommends the following:
10681
Air Filter-Regulator-Lubricator (FRL) – Provides accurate air
pressure regulation and two stage filtration of water contaminant's.
•
Grease the planetary gear assembly with the
95542
Grease by applying
2-3 plunges
with the
95541
Grease Gun after
every 50 hours
of use for
maximum gear life.
•
Dynabrade recommends one drop of air lube per minute for each 20 SCFM (example: if the tool specification states 40 SCFM, set the drip rate on the
filter-lubricator to 2 drops per minute). Dynabrade Air Lube (P/N
95842
: 1 pt 473 ml) is recommended.
Routine Preventative Maintenance:
•
Check free speed of Pistol Grip Drill using a tachometer after every service or repair.
Caution:
Mineral spirits are recommended when cleaning the tool and parts. Do not clean tool or parts with any solvents or oils containing acids, esters,
ketones, chlorinated hydrocarbons or nitro carbons.
Caution:
DO NOT clean or maintain tools with chemicals that have a low flash point (example: WD-40
®
).
•
A Motor Tune-Up Kit (P/N
96067
) is available which includes high wear and medium wear motor parts.
•
Air tool laser etch information must be kept legible at all times, if not, reorder housing and replace. User is responsible for maintaining specification
information i.e.: Model #, S/N, and RPM. (See Assembly Breakdown)
•
Blow air supply hose out prior to initial use.
•
Visually inspect air hoses and fittings for frays, visible damage and signs of deterioration. Replace damaged or worn components.
•
Refer to Dynabrade's Warning/Safety Operating Instructions Tag (Reorder No.
95903
) for safety information.
After maintenance is performed on tool, add a few drops of Dynabrade Air Lube (P/N
95842
) to the air line and start the tool a few times to lubricate air motor.
Check for excessive tool vibration.
Handling and Storage:
•
Use of tool rests, hangers and/or balancers is recommended.
•
Protect tool inlet from debris.
•
DO NOT carry tool by air hose, or near the trigger.
•
Store accessories in protective racks or compartments to prevent damage.
Machine Specifications
3
Model
Motor
Motor
Chuck
Sound
Air Flow Rate
Air Pressure
Spindle Thread
Weight
Length
Height
Number
hp (W)
RPM
Size
Level
SCFM (LPM)
PSIG (Bars)
Size
Pound (kg)
Inch (mm)
Inch (mm)
52903
.4 (310)
500
1/4"
76 dB(A)
23 (651)
90 (6.2)
3/8"-24
3.7 (1.7)
10.6 (268)
11.8 (300)
52904
.4 (310)
1,000
1/4"
80 dB(A)
25 (708)
90 (6.2)
3/8"-24
3.7 (1.7)
10.6 (268)
11.8 (300)
52905
.4 (310)
2,400
1/4"
77 dB(A)
22 (623)
90 (6.2)
3/8"-24
3.1 (1.4)
10.6 (268)
11.8 (300)
52906
.4 (310)
3,600
1/4"
80 dB(A)
23 (651)
90 (6.2)
3/8"-24
3.1 (1.4)
10.6 (268)
11.8 (300)
52907
.4 (310)
5,500
1/4"
81 dB(A)
25 (708)
90 (6.2)
3/8"-24
3.1 (1.4)
10.6 (268)
11.8 (300)
Additional Specifications: Air Inlet Thread 1/4" NPT • Hose I.D. 3/8" or 10 mm
Sound Level is the pressure measurement according to the method outlined in ISO regulation ISO-15744.
Notice
All Dynabrade motors use the highest quality parts and materials available and are machined to exacting tolerances. The failure of quality pneumatic motors can
most often be traced to an unclean air supply or the lack of lubrication. Air pressure easily forces dirt or water contained in the air supply into motor bearings
causing early failure. It often scores the cylinder walls and the rotor blades resulting in limited efficiency and power. Our warranty obligation is contingent upon
proper use of our tools and cannot apply to equipment which has been subjected to misuse such as unclean air, wet air or a lack of lubrication during the use
of this tool.
Lifetime Warranty
All Dynabrade portable pneumatic power tools are rigorously inspected and performance tested in our factory before shipping to our customers. If
a Dynabrade tool develops a performance problem and an inherent defect is found during normal use and service, Dynabrade will warrant this tool
against defects in workmanship and materials for the lifetime of the tool. Upon examination and review at our factory, Dynabrade shall confirm that
the tool qualifies for warranty status, and will repair or replace the tool at no charge to the customer. Normally wearable parts and products are NOT
covered under this warranty. Uncovered items include bearings, contact wheels, rotor blades, regulators, valve stems, levers, shrouds, guards, O-
rings, seals, gaskets and other wearable parts. Dynabrade’s warranty policy is contingent upon proper use of our tools in accordance with factory
recommendations, instructions and safety practices. It shall not apply to equipment that has been subjected to misuse, negligence, accident or
tampering in any way so as to affect its normal performance. To activate lifetime warranty, customer must register each tool at www.dynabrade.com.
Dynabrade will not honor lifetime warranty on unregistered tools. A one-year warranty will be honored on all unregistered portable pneumatic power
tools. Lifetime warranty applies only to portable pneumatic tools manufactured by Dynabrade, Inc. in the USA. Lifetime warranty applies only to the
original tool owner; warranty is non-transferable.