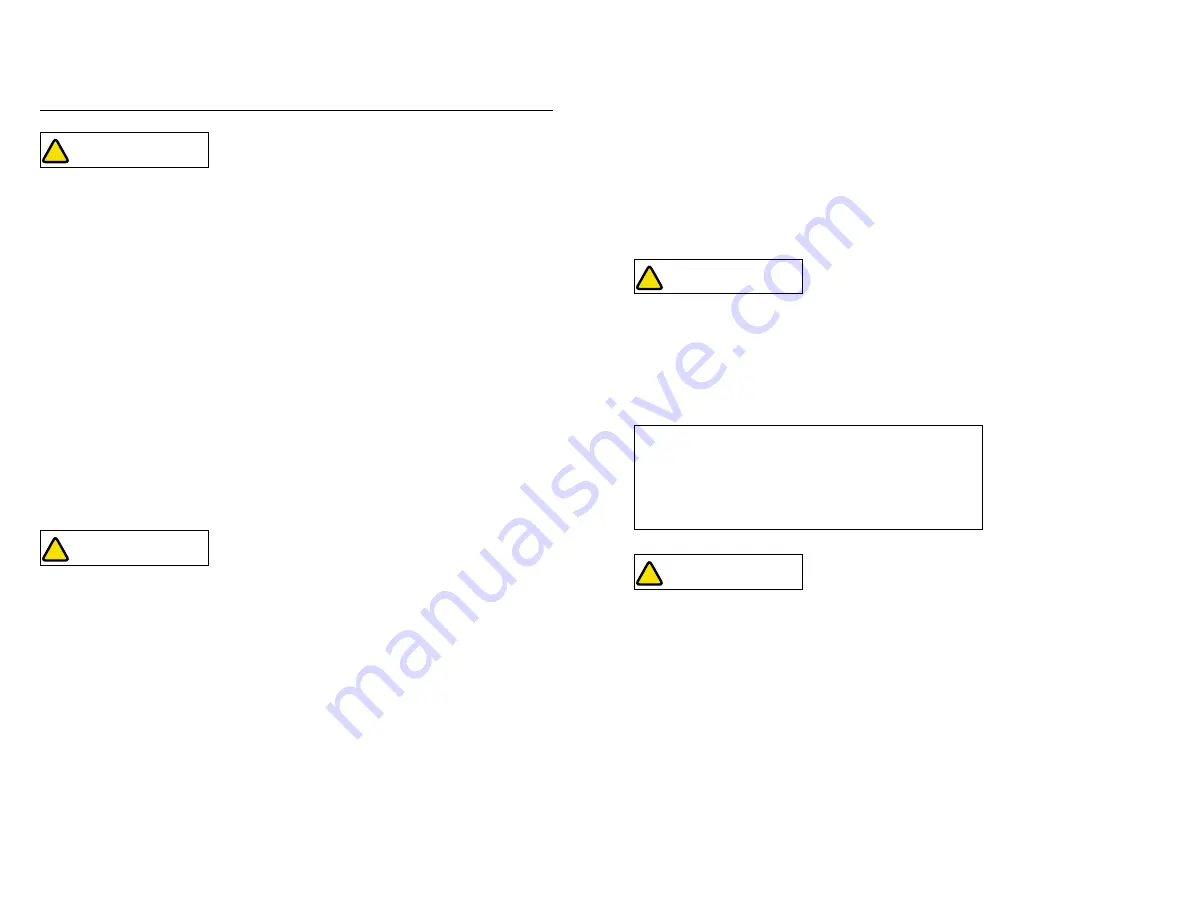
11
10
This machine is intended to be operated by experienced
machinery operators. Operator shall also be aware of any
additional personnel in the general vicinity. Each person should
always know the whereabouts of the other person(s). Operators
are to be familiarized with the safety of operation of this manual.
!
CAUTION
Keep children, bystanders and animals at least 100’ away from
machine while in operation. Beware of any potential flying pieces
of wood from saw or out of the splitting wedge. Logs on the deck
also have the potential to fall or possibly roll off causing severe
damage to the machine or to the operator and any bystanders.
CALIFORNIA
Proposition 65 Warning
Diesel engine exhaust fumes and some of its constituents are
known to the State of California to cause cancer, birth defects,
and other reproductive harm.
!
DANGER
Before starting machine make a circle around your machine.
The machine area should be restricted to any by-passers. It is
absolutely necessary that the operator has unobstructed access
to the machine with no protruding branches, logs, stumps, or
uneven ground to cause tripping and possibly result in severe
injury. The log deck and discharge conveyor should be secured.
Check for loose components, tools, or foreign objects in or on
any part of the machine. Check for blown or leaky hoses or
disconnected fuel lines. Make sure all caps are on reservoirs or
tanks and are tightly secured. Make sure all canvas covers are
removed while in operation.
SAFETY OF OPERATION
!
DANGER
This machine was built and designed with your safety in mind.
Your physical well-being is important to us. Decals and guarding
were installed on your machine for your safety. It will only serve
as your protection if the decals are read, understood, and
followed as indicated. Guarding should be left installed and
maintained.
All operators or potential operators are to read and understand
the complete owner’s manual. It is the owner of this machine’s
responsibility to insure that all individuals operating this machine
are properly trained and qualified according manufacturer’s
recommendations. Any individual who has not read and
understood this owner’s manual and decals is
NOT
qualified to
operate this machine. The operator’s safety is dependent on the
individual’s knowledge of this machine and how to safely operate
this machine at full potential.
!
WARNING
Almost all accidents occur when proper operator safety
procedures are not followed or machine has not been properly
maintained and/or adjusted to manufacturer recommendations.
Operator mistakes normally occur when the individual has
operated the machine for a length of time. After the operator
is accustomed to the machine the alertness and cautiousness
has a tendency to fade away. Reaching into splitter area while
splitter is in motion, steadying the log while feeding log forward or
holding onto the wood while saw is in function are some common
mistakes made when accidents happen. Usually these mistakes
are made by experienced operators. Always maintain the initial
operator alertness throughout all the time spent operating this
machine.
IMPORTANT SAFETY INFORMATION
IMPORTANT SAFETY INFORMATION