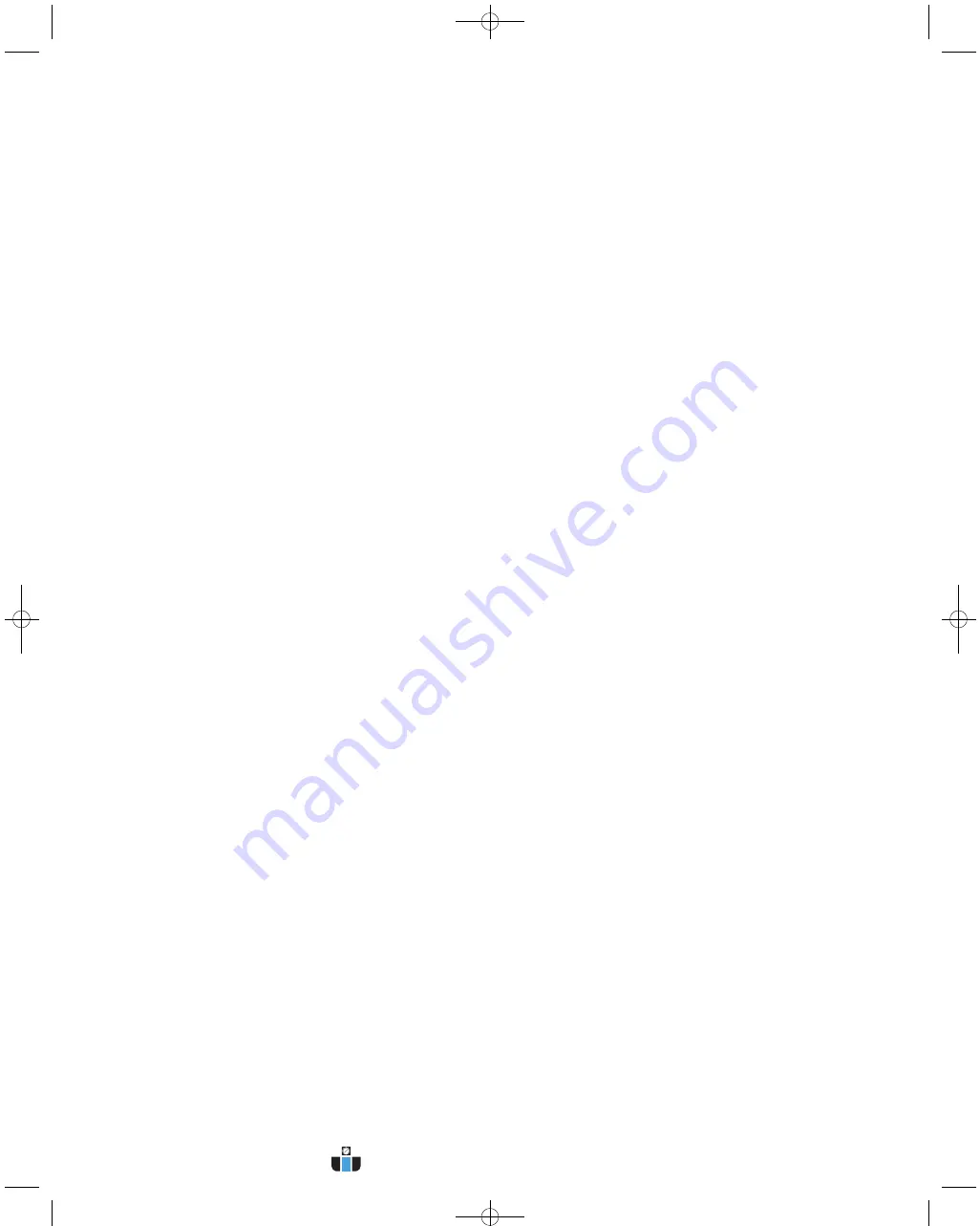
2.5 • Low Limit [Only available when DCP installed]
The operation of the Low Limit, available only with a pressure module
installed, is identical to the High Limit except this value sets the pressure
where the cleaning cycle will end. The upper settable value is the
calibration pressure of the pressure module and the lower limit is zero.
Pressing “SELECT” will change the system to the High Alarm Setup
mode.
2.6 • High Alarm [Only available when DCP installed]
The operation of the High Alarm Setup is identical to the High and Low
Limit Setup and is only available when a pressure module is installed. The
High Alarm default is 0. The upper settable value is the full scale pressure
of the pressure module and the lower limit is zero. Pressing “SELECT” will
change the system to the Low Alarm Setup mode.
2.7 • Low Alarm [Only available when DCP installed]
The operation of the Low Alarm Setup is identical to the High and Low
Limit Setup. The Low Alarm default is 0. The upper settable value is the
full scale pressure of the pressure module and the lower limit is zero.
Pressing “SELECT” will change the system to the Cycle Delay Setup
mode.
2.8 • Cycle Delay (min)
The cycle delay inserts a delay time between the end of the last channel
and the beginning of the first channel. This may be set to between zero
and 255 minutes. The factory default is zero. Setting the value to zero will
disable the delay. Pressing “SELECT” will change the system to the Down
Time Cycles Setup mode.
2.9 • Down Time Cycles (min)
The Down Time Cycles setup will select a value between zero and 255
minutes. The factory default is one minute. Selecting zero will disable the
operation. When the down time cycles is activated by shorting the down
time cycles input to the common terminal, (see figure 2) the system will
enter a forced cleaning mode for the programmed duration.
Note:
The
cycle delay, if one is programmed, will not be inserted in the timing cycle.
Pressing “SELECT” will change the system to the Auto Alarm Reset Setup
mode, if a pressure module is installed, or to Process when no pressure
module is available.
2.10 • Auto Alarm Reset (sec) [Only available when DCP installed]
The Auto Alarm Reset Setup, available only when a pressure module is
installed, allows the auto alarm reset time to be selected. This value may
be set between zero and 255 seconds. The factory default value is five
seconds. When the auto alarm reset is enabled by shorting the auto alarm
reset terminal to a common terminal, (See Figure 1) the alarm will be reset
after the pressure returns to the normal range and the timeout has
expired. Pressing “SELECT” will change the system to Process mode.
3.0 Maintenance Support and Diagnostics
We have also included a number of features that will aid maintenance
personnel in diagnosing problems or verifying that the system is operating.
3.1 Restoring Factory Defaults
The DCT1000DC has been programmed with factory default values that
meet most industry operating conditions. In the event that you want to
restore all of the parameters to the original factory default values:
(1) Return the master controller to the process mode.
(2) Press and hold both “UP” and “DOWN” buttons.
The display will indicate a 10-second countdown, at the end of which all
parameters will be restored to factory defaults. Releasing the switches
prior to the end of the count will stop the process and no modification will
be made. Likewise, in each of the parameter setup modes, pressing and
holding the “UP” and “DOWN” buttons simultaneously will reset the
individual default value, leaving other settings unchanged.
3.2 Power Indicator
A power on LED indicator is provided at the center left edge of the board.
This will be illuminated when the power supply is operating properly. If the
power LED is not illuminated, the primary power may be off or there is a
fault in the power circuit.
3.3 Active Channel Indicator
Located just above the solenoid terminations, you will find that each
channel is provided with an LED that is illuminated when the triac switch
is on. This allows a visual correlation between the channel being pulsed
and the operation of the solenoid.
3.4 Comm Check Indicator
The comm check indicator can be found in the upper right hand corner of
the slave and master controller board (just above the “out” terminal, a
telephone style connector). This indicator is used for two purposes. First,
on a master controller a brief flash once per second is produced to
indicate that the system is operating. Second, this indicator is used to
show when the communication check operation is performed on slave
boards. The master controller will check each of the slave boards at a rate
of about one inquiry per second, starting with the slave board connected
directly to the master controller and ending with the last slave board in the
chain. The master controller will flash its Comm Check LED for about 250
msec each time it makes a communication check. The external module
selected for test will also flash its Comm Check LED for about the same
time each time it is interrogated. Observing this test sequence will indicate
that the communication between boards is operational. When a slave
board powers up, the Comm Check LED will be illuminated continuously.
It will be extinguished when the master controller has initialized its
communication channel. This indicator then shows that a master
controller is operating and that each slave board is responding properly on
the daisy chain.
E-97DC:e-97DC 10/5/10 8:27 AM Page 7
www.calcert.com
1.888.610.7664
0
5
10
15
20
25
30