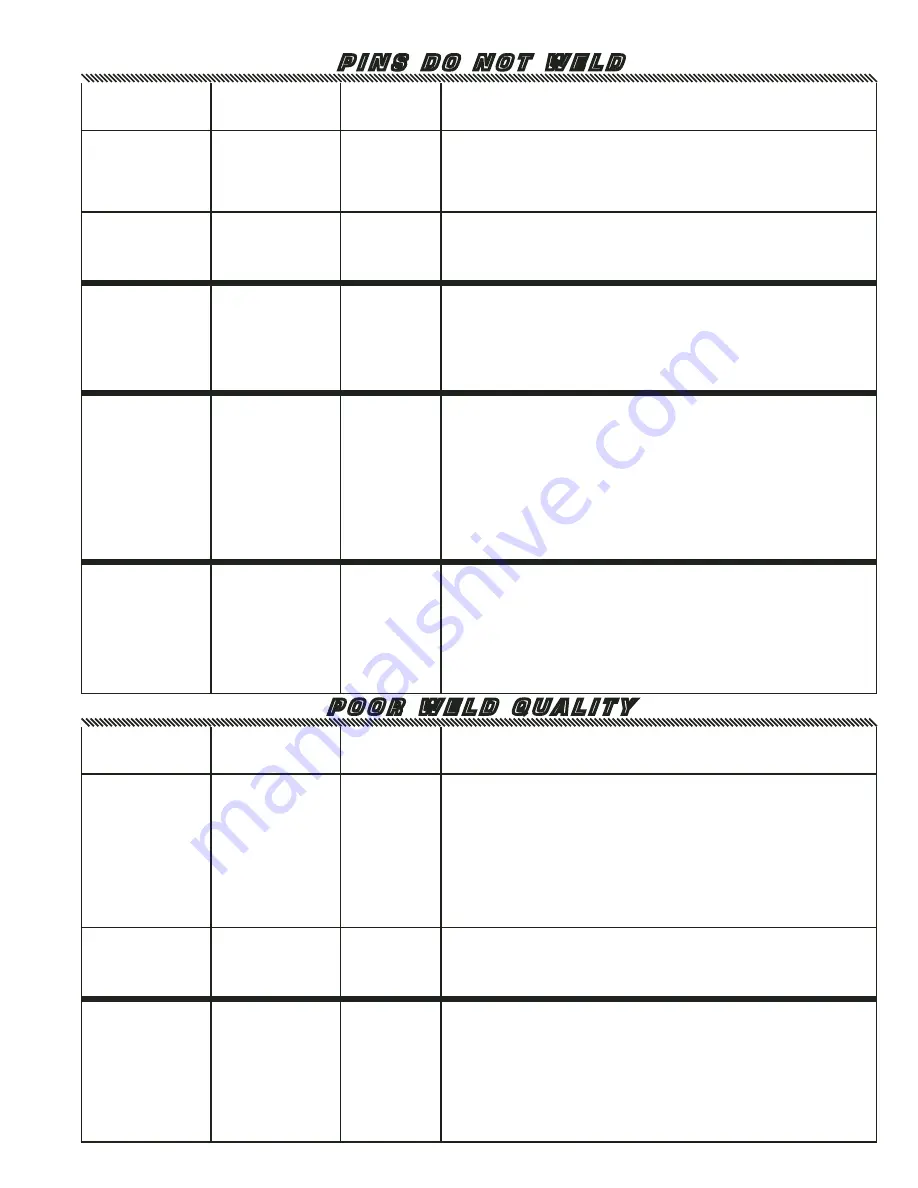
- 21 -
P I N S D O N O T W E L D
P O O R W E L D Q U A L I T Y
SYMPTOM
CORRECT
FUNCTION
INDICATOR
POSSIBLE
PROBLEM
ACTION
All indicators are
functioning
except
Weld signal, Weld
#1 and Weld #2
Weld signal indica-
tor goes on and
off with every
cycle
(A) Short cycle
relay.
(A) The Short cycle relay controls the voltage that turns on the Solid-
state relays that turn on the Weld transformer. To test this Short
cycle relay circuit check the voltage (24VAC+/-) at terminals #18 and
#21. Terminals #18 and #21 should go from 0 to 24VAC and back
to 0 on every cycle. If this voltage reading is incorrect replace Short
cycle relay.
(B) Pressure
switch.
(Mach Two
models
only)
(B) To test the pressure switch place a jumper between terminals #37
and #38. If the machine welds with jumper in place replace Pressure
switch.
All i
ndicators are
functioning except
Weld #1 and
Weld #2
Weld relay #1 or
Weld relay #2
indicator should
correspond with
Weld signal
indicator.
Goes on and off
with every cycle
Head test
switch.
The head test switch is single-pole, double-throw and center off switch.
This switch delegates which Solid State Relay controls the Weld
transformer.
To test this switch check for continuity at the switch.
All indicators are
Functioning.
Welding indicator
on the frame is
not functioning.
This indicator
shows when
there is voltage
(/-)
present at
the Primary
of the Weld
transformer.
All lights flash in
sequence
Solid State
Relay
The Solid State Relay controls the voltage to the Primary of the Weld
transformer. To check these Solid State Relays test for voltage
(24VAC+/_) at terminals A1 and A2 on the relay. Terminals A1 and
A2 should go from 0 to 24VAC and back to 0 on every cycle. If this
voltage reading does not correspond check the switch position. If this
voltage reading is correct now test the voltage (208-230 VAC+/-) at
the terminals L1 and T1. Terminals L1 and T1 should go from (208-230
VAC+/-) to 0 and back to (208-230 VAC+/-) with every cycle. If this
voltage is incorrect replace Solid State Relay.
All indicators are
functioning in-
cluding the Weld
indicator on the
frame
All lights flash in
sequence
Weld trans-
former.
To test the Primary of the transformer check the voltage at the terminals
L1 and T1 on the Solid State Relays. They should go from (208-230
VAC+/-) to 0 and back to (208-230 VAC+/-) every time the machine
cycles. Now test the secondary output voltage. Place meter leads on
copper bars coming out of the transformer(s) and test the voltage
every time the machine is cycled. The Mach 1 Transformers should
read approximately 5VAC. (2.5 VAC x 2 =5VAC) The Mach 2 should read
approximately 10VAC. (maybe 5VAC if on center tap) If the secondary
voltage reading is incorrect replace the transformer. (Turn the Weld
time to the highest setting when performing this test.)
SYMPTOM
CORRECT
FUNCTION
INDICATOR
POSSIBLE
PROBLEM
ACTION
Dwell delay
indicator is not
functioning
Dwell delay indicator
comes on when
the Weld timer
indicator goes off
and then goes off
when the Dwell
solenoid indicator
goes off.
(A) Short cycle
relay or
First pulse
relay
(A) The Dwell delay timer keeps the Dwell circuit on 150ms longer than
the Weld timer circuit. To check the Dwell delay timer test for voltage
(24VAC+/-) at terminal #11 and #12. The voltage on terminals #11
and #12 should go from 24VAC to 0 and back to 24VAC with every
machine cycle. If this voltage reading is correct proceed to step (B).
If this voltage reading is incorrect check the Short cycle relay at the
terminals TB4 (NC) and #11. This voltage reading should go from 24VAC
to 0 and back to 24VAC on every machine cycle. If this voltage reading
is incorrect replace the Short cycle relay. If this voltage reading is
correct and the voltage reading at terminals #11 and #12 are still
incorrect replace the First pulse relay
.
(B) Dwell delay
timer
(B) If procedures (A) test correctly now check the voltage (24VAC+/-) at
the terminals #9 and #12. The voltage at the terminals #9 and #12
should go from 0 to 24VAC and back to 0 on every machine cycle. If this
voltage reading is incorrect replace the Dwell delay timer.
All indicators are
functioning
All lights flash in
sequence
(A) Weld cable.
(B) Upper and
Lower
welding tips.
(C) Upper tip
retainer.
(D) Weld cable
retainer.
(F) Power
supply bar
Any connection from the Secondary of the Transformer to the Weld tips
can contribute to a poor weld quality. All the connections should be
Clean, Bright and Tight.
The Weld cable from use can also start
breaking down. Always inspect the Weld cable, transformer secondary
connections and Weld tips for they are the most common causes for
a poor weld quality.