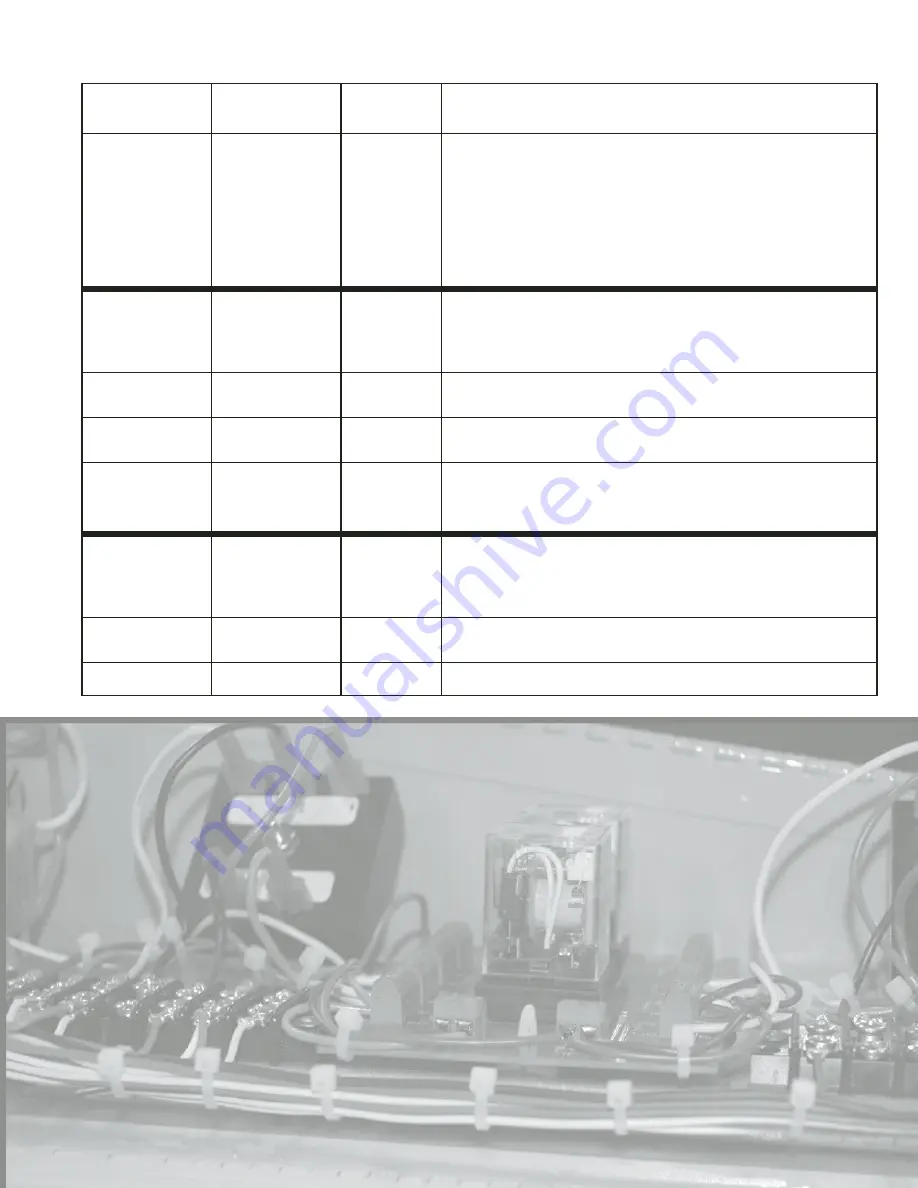
- 19 -
SYMPTOM
CORRECT
FUNCTION
INDICATOR
POSSIBLE
PROBLEM
ACTION
Feed collides with
dwell.
All indicators are
functioning
correctly except:
Dwell reed switch
output and
Feed solenoid
indicators are
not coming on
in the correct
sequence.
Dwell reed switch
output indicator
turns on with
the first machine
cycle. Goes off
and then back on
with every cycle.
F e e d s o l e n o i d
indicator goes on
and then back off
with every cycle.
Dwell reed
switch
The Dwell reed switch initiates the Feed timer. If this switch is malfunctioning
or out of position it will initiate the feed at the wrong time.
Refer to the action section on page 18 for Dwell reed switch possible
problem for instructions on how to check and adjust.
Sluggish
movement of
the Feed.
All indicators are
functioning
correctly
All lights flash in se-
quence
(A) Feed Speed
Control.
(A) Readjust the Feed Speed Control located on the air line going to the
Feed cylinder.
(B) Air Lines.
(B) Check the air lines for leaks and water in the air lines. If there is water
in the air lines, disconnect and blow out all air lines. Remove and clean
muffler. Reconnect the air lines and the muffler.
(C) Feed
cylinder.
(C) Turn the power and air off. Check the Feed cylinder and the Pusher
with Pawl for binding. Move Feed in and out. The Feed should move in
and out with a slight resistance.
(D) Feed
Solenoid.
(D) If the above procedures check out and the Feed still has sluggish
movement the problem may be the Feed solenoid. Remove the air
line from air inlet of the solenoid and spray a light oil in the solenoid.
Reconnect air line and cycle machine. If Feed still has sluggish movement
replace the Feed solenoid.
Feed does not
place Weld pins on
Upper Weld Tip.
All indicators are
functioning
correctly
All lights flash in se-
quence
(A) Feed Speed
Control.
(A) If the Feed Speed Control is open too much it may throw pins past
the Upper Weld Tip. Adjust Feed Speed Control so that it places the
pin on the Upper Weld Tip.
(B) Upper Weld
Tip.
(B) Check the Upper Weld Tip for Magnetism. Place a Weld pin under the
Upper Weld Tip. If the tip does not retain the pin or magnets feel weak
replace Upper Weld Tip.
(C) Pusher
with pawl.
(C) The Pawl (hinged part) on the Pusher may be damaged or missing. If
so replace Pusher with Pawl.