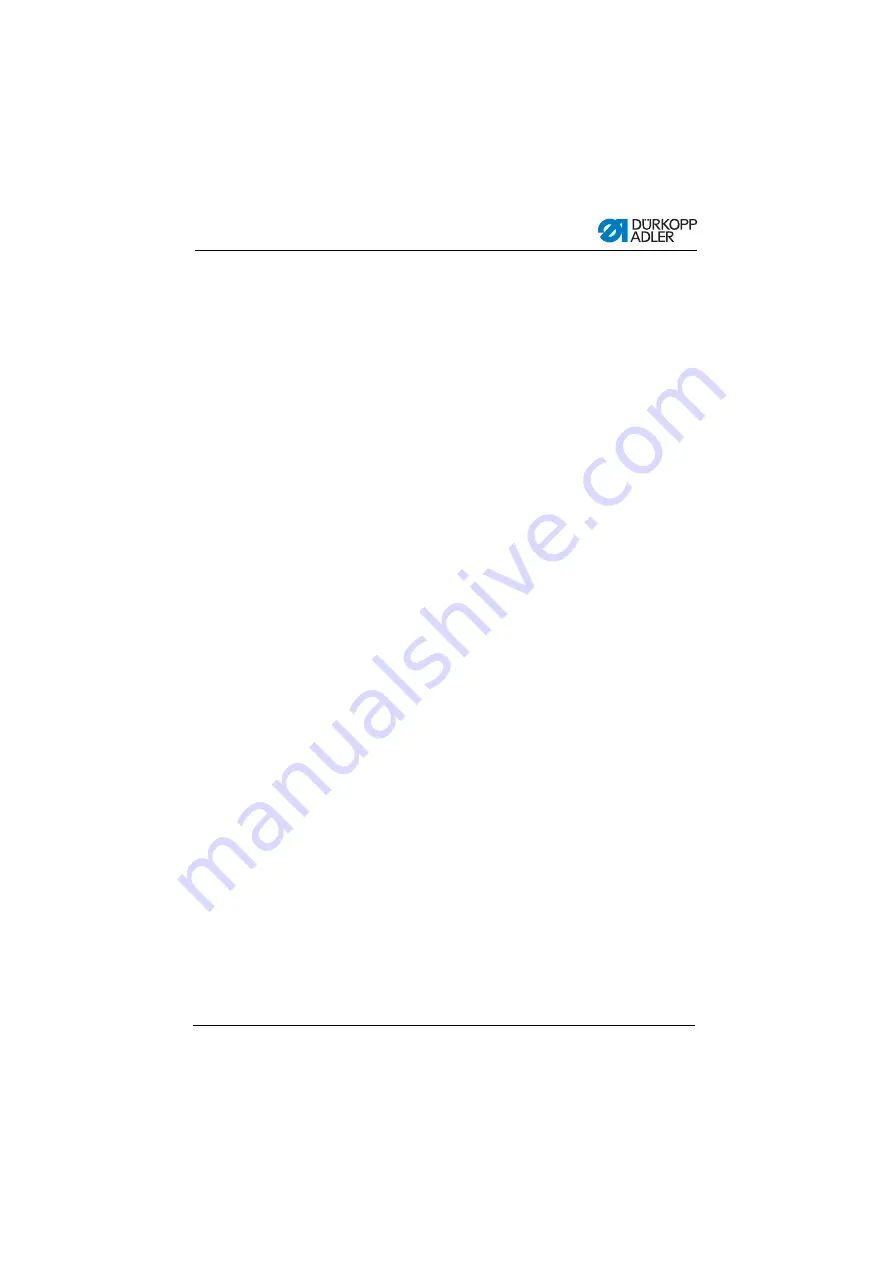
About this manual
Operating manual 281 Version 06.0 - 05/2013
3
1 About this manual
1.1 Scope of application of the manual
This manual describes the intended use and the set-up of the
special sewing machine 281.
It applies to all submodels listed in Section
1.2 Damage during transport
Dürkopp Adler cannot be held liable for any damage during
transport. Check the delivered product immediately after receiving
it. Report any damage to the last transport manager. This also
applies if the packaging is not damaged.
Keep the machines, devices, and packaging material in the
condition they were at the time the damage was identified.
That secures any claims towards the transport company.
Report all other complaints to Dürkopp Adler immediately after
receiving the product.
1.3 Limitation of liability
All information and notes in this operating manual have been
compiled in accordance with the latest technology and the
applicable standards and regulations.
The manufacturer accepts no liability for any damage due to:
• Failure to observe the instructions in the manual
• Improper use
• Unauthorized modifications to the machine
• The deployment of untrained personnel
• Damage during transport
• Using spare parts not approved
Summary of Contents for DAC classic 281
Page 1: ...281 Operating Manual...
Page 16: ...Performance description Operating manual 281 Version 06 0 05 2013 14...
Page 18: ...Device description Operating manual 281 Version 06 0 05 2013 16...
Page 46: ...Operation Operating manual 281 Version 06 0 05 2013 44...
Page 70: ...Disposal Operating manual 281 Version 06 0 05 2013 68...
Page 72: ...Appendix Operating manual 281 Version 06 0 05 2013 69...
Page 73: ......