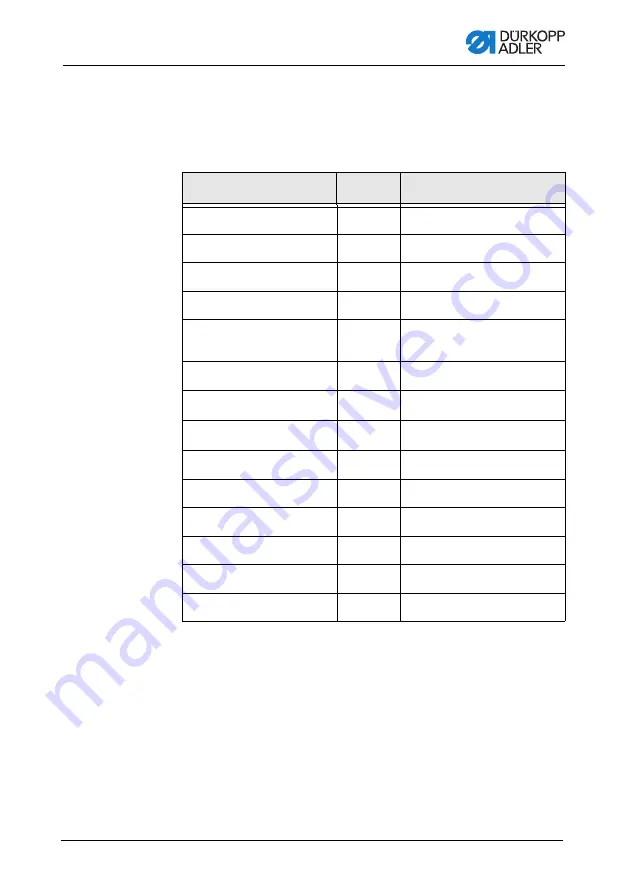
Technical data
Operating Instructions 969 PURE - 00.0 - 04/2020
77
10 Technical data
10.1 Data and characteristic values
10.2 Requirements for fault-free operation
Compressed air quality must conform to ISO 8573-1: 2010 [7:4:4].
Technical data
Unit
969 PURE
Machine type
Lockstitch 301
Hook type
Barrel shuttle, XL large
Number of needles
1
Needle strength
[Nm]
140-280
Thread strength
[Nm]
43/3-5/3 (needle thread)
60/3-8/3 (hook thread)
Stitch length
[mm]
12/12
Speed maximum
[min
-1
]
800
Speed on delivery
[min
-1
]
800
Mains voltage
[V]
230
Mains frequency
[Hz]
50/60
Length
[mm]
700
Width
[mm]
250
Height
[mm]
420
Weight
[kg]
92
Summary of Contents for 969 PURE
Page 1: ...969 PURE Operating Instructions...
Page 14: ...Safety 12 Operating Instructions 969 PURE 00 0 04 2020...
Page 18: ...Machine description 16 Operating Instructions 969 PURE 00 0 04 2020...
Page 70: ...Setup 68 Operating Instructions 969 PURE 00 0 04 2020...
Page 72: ...Decommissioning 70 Operating Instructions 969 PURE 00 0 04 2020...
Page 74: ...Disposal 72 Operating Instructions 969 PURE 00 0 04 2020...
Page 78: ...Troubleshooting 76 Operating Instructions 969 PURE 00 0 04 2020...
Page 80: ...Technical data 78 Operating Instructions 969 PURE 00 0 04 2020...
Page 82: ...Appendix 80 Operating Instructions 969 PURE 00 0 04 2020 Fig 39 Fixed tabletop without slot...
Page 83: ...Appendix Operating Instructions 969 PURE 00 0 04 2020 81 Fig 40 Swiveling tabletop...
Page 85: ...Appendix Operating Instructions 969 PURE 00 0 04 2020 83 Fig 42 Swiveling tabletop...
Page 87: ......