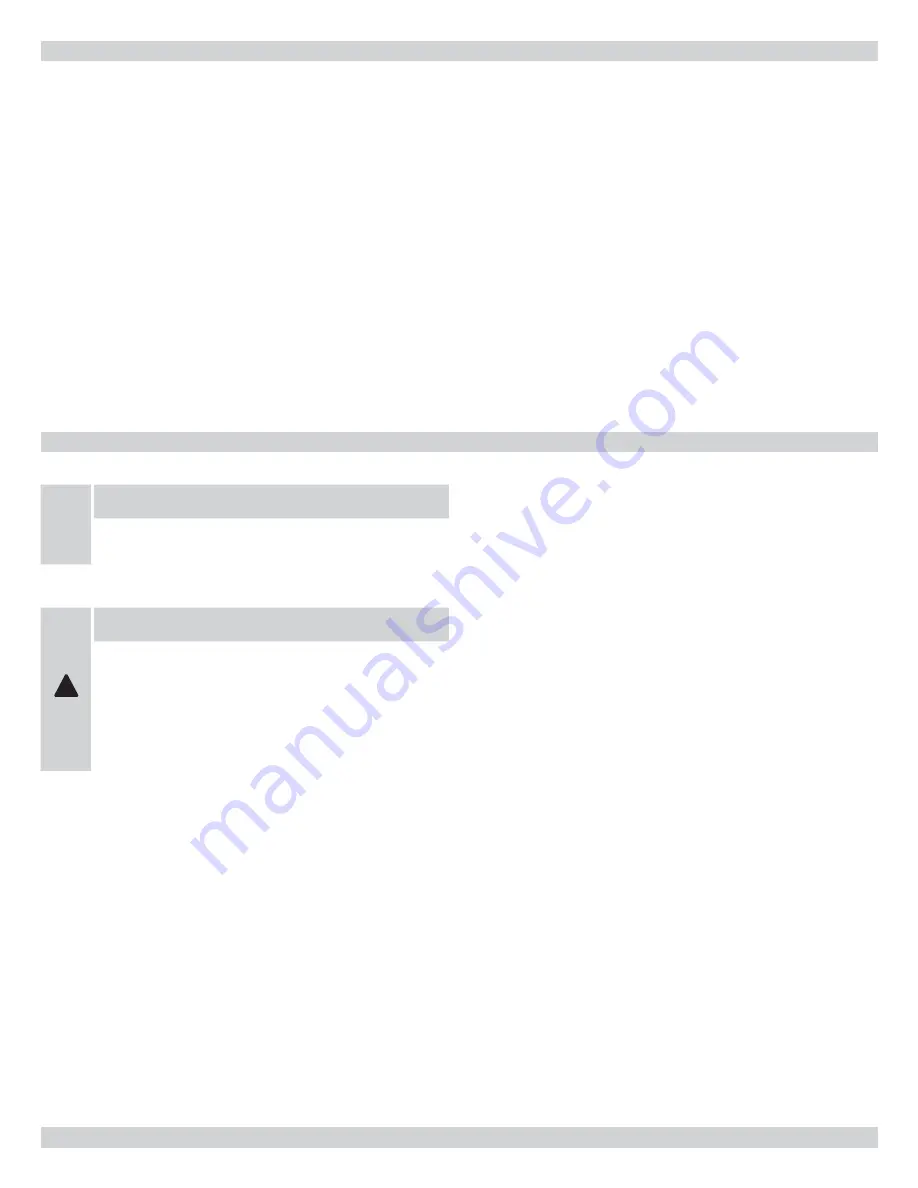
3
NOTICE
Read and understand the following
instructions completely before installing.
Introduction
This appliance is a gas-fi red direct vent cast aluminum
hot water boiler. A revolutionary cast aluminum heat
exchanger means better heat transfer and thermal storage
than similarly sized cast iron boilers, which results in
higher effi ciency. The heating system water absorbs large
amounts of heat from the cast aluminum heat exchanger,
cooling the fl ue gases and causing condensation. Sealed
combustion, premix gas burner, and low fl ame temperature
means drastically reduced CO and NOx emissions, which
contribute to a cleaner and healthier environment.
This appliance has been equipped for residential
installations. If used for commercial applications, any and
all additional code requirements must be adhered to for
installation. This may require additional controls, including
but not limited to a manual reset low water cut off, a
manual reset high temperature limit, and wiring and/or
piping modifi cations.
The manufacturer is not responsible for any fi eld
installation changes made to a boiler installation which are
not described or acknowledged in this manual.
Check all applicable state and local building codes and
1.
utility company requirements before installation. This
installation must conform with these requirements in
their entirety. In the absence of these codes, use NFPA
installation codes and good industry practice.
Before servicing the boiler, allow it to cool. Always
2.
shut off any electricity and gas supply connected to the
boiler prior to servicing.
Inspect gas line for leaks.
3.
Be certain gas input rate is correct. Over-fi ring may
4.
result in early failure of the boiler components. This
may cause dangerous operation. Under-fi ring may
result in too much air for the pre-mix burner causing
poor or loss of combustion.
Never vent the products of combustion from this boiler
5.
to an enclosed space. Always vent to the outdoors.
Never vent to another room or to inside a building.
Be sure there is adequate outdoor air supply to boiler
6.
for complete combustion.
Follow a regular service and maintenance schedule for
7.
effi cient and safe operation.
Keep boiler area clean of debris and free from
8.
combustible materials, gasoline and other fl ammable
vapors and liquids.
Proper through-the-wall or through-the-roof
9.
combustion venting shall be in accordance with the
materials and methods described in this manual.
Installation must comply with local codes.
This boiler and related hot water heating systems are
10.
not do-it-yourself items. They must be installed and
serviced by qualifi ed professionals.
RULES FOR SAFE INSTALLATION AND OPERATION
!
WARNING
Failure to follow these instructions could cause
a malfunction of the boiler and result in death,
serious bodily injury, and/or property damage.
For assistance or additional information,
consult a qualifi ed installer, service agency, or
the gas supplier.
This appliance, unlike normal residential atmospheric and
induced draft units, takes its combustion air directly from
the outdoors (sealed combustion) and does not compete
with building occupants for fresh air. Sealed combustion
(also known as “direct vent”) is the safest and best way
to obtain plenty of clean combustion air. The forced draft
fan draws in the outside combustion air to mix with gas,
which fl ows into the pre-mix burner and combusts. The
fan then forces the resulting fl ue gases from the boiler unit
and provides a positive removal of the fl ue gases from the
building through inexpensive and readily available PVC and
CPVC vent pipes.
90 125-200 CAST ALUMINUM BOILER
Summary of Contents for Q90-125
Page 30: ...30 SERVICE HINTS DETAILED SEQUENCE OF OPERATION...
Page 36: ...36 Troubleshooting Chart 2 TROUBLESHOOTING...
Page 39: ...39 Troubleshooting Chart 5 TROUBLESHOOTING...
Page 42: ...42 This Page Intentionally Left Blank...
Page 44: ...DUNKIRK BOILERS 2201 Dwyer Avenue Utica NY 13501 web site www ecrinternational com...