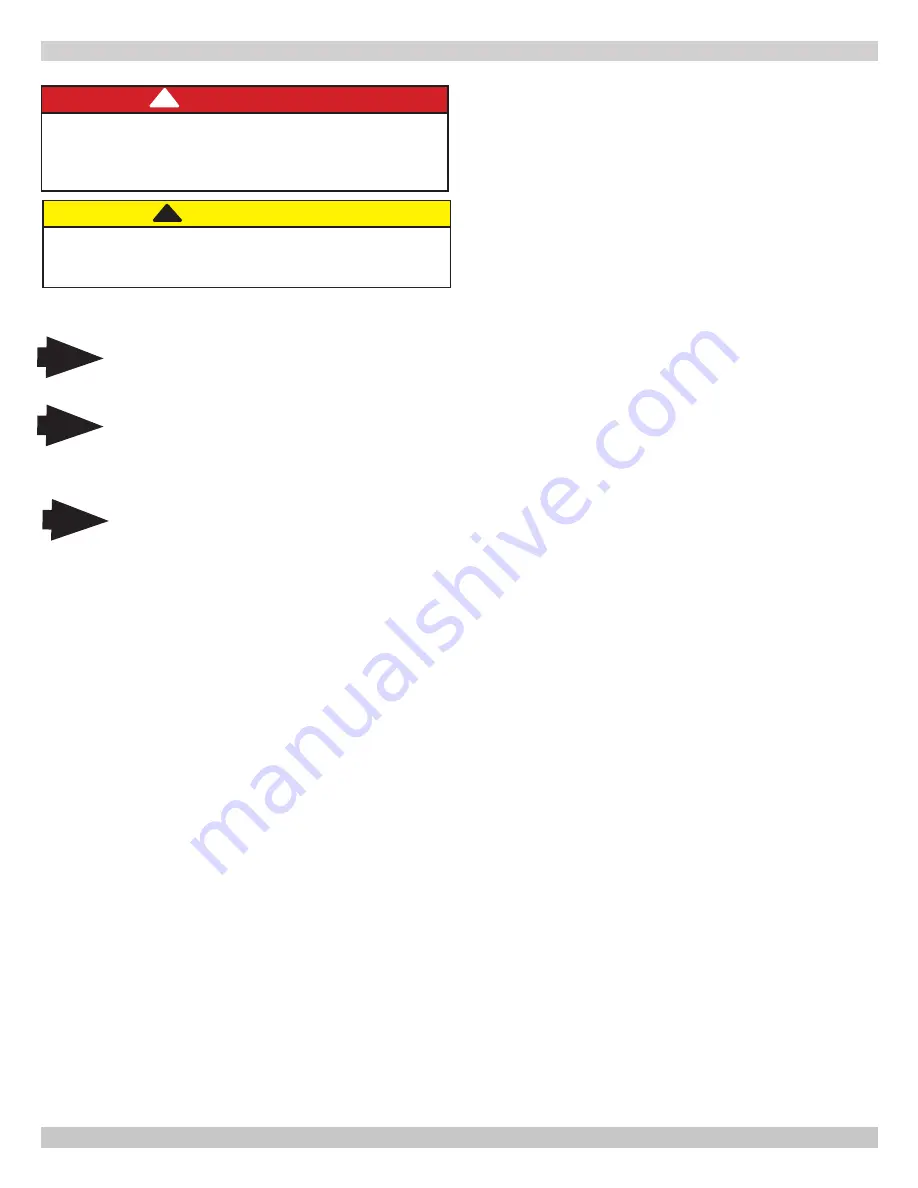
46
11.1 Beginning of Each Heating Season
• Check boiler area is free from combustible materials,
gasoline, and other flammable vapors and corrosive liquids.
• Visually inspect combustion air and vent piping for proper
operation. Check for and remove any obstruction to flow
of combustion air or vent gases. Immediately repair or
replace pipe showing deterioration or leakage. Reassemble
per instructions in section 6. Ensure proper reassembly and
resealing of system.
• Visually inspect condensate drain line for proper operation.
Checking for deteriorated or plugged condensate drain line.
Verify condensate trap drains freely and clean as required.
• Test safety relief valve for proper operation. Refer to valve
manufacturer's instructions packaged with relief valve.
• Examine heat exchanger, burner, condensate lines, and
clean (if necessary) by following instructions in section
11.3 - Component Replacement And Cleaning.
CAUTION
Label all wires prior to disconnection when servicing
controls. Wiring errors can cause improper and
dangerous operation.
!
DANGER
Before servicing, turn off electrical power to boiler at
service switch. Close manual gas valve to turn gas
supply OFF to boiler. Failure to comply will result in
death or serious injury.
!
Note
V
erify proper operation after servicing.
Note
Perform regular service and maintenance by
qualified service agency at least once every 12
months to assure safe, trouble free operation
and maximum efficiency.
• Circulator pump and combustion air blower motor furnished
with boiler are permanently lubricated from factory and
require no further lubrication. Lubricate field sourced
pumps and/or motors according to pump and/or motor
manufacturer’s instruction.
• Check following components are operating properly and are
free of blockages or obstructions:
• air vent;
• check venturi air inlet for blockage and clean as
required;
• verify pressure test port cap and combustion test port
caps are in place;
• verify supply and return sensors are properly clipped to
pipes as close to heat exchanger as possible;
• Check boiler for any sign of leaks.
•
Check external low water cutoff operation (if installed).
• Check operation by pressing test button on low water
cutoff.
• "Low Water" LED on the external LWCO should
illuminate and boiler should shut down.
•
Every 5 years remove low water cutoff. Reinstall after
cleaning.
•
Every 10 years replace low water cutoff.
•
Visual inspection of flame through sight glass. Burner
should be fully illuminated.
• Check heating system expansion tank.
Note
A Heat Exchanger cleaning kit is available for
annual service of the boiler. See repair parts
manual for part number.
11 - GENERAL MAINTENANCE AND CLEANING
240012564 REV A, [05/15/2019]