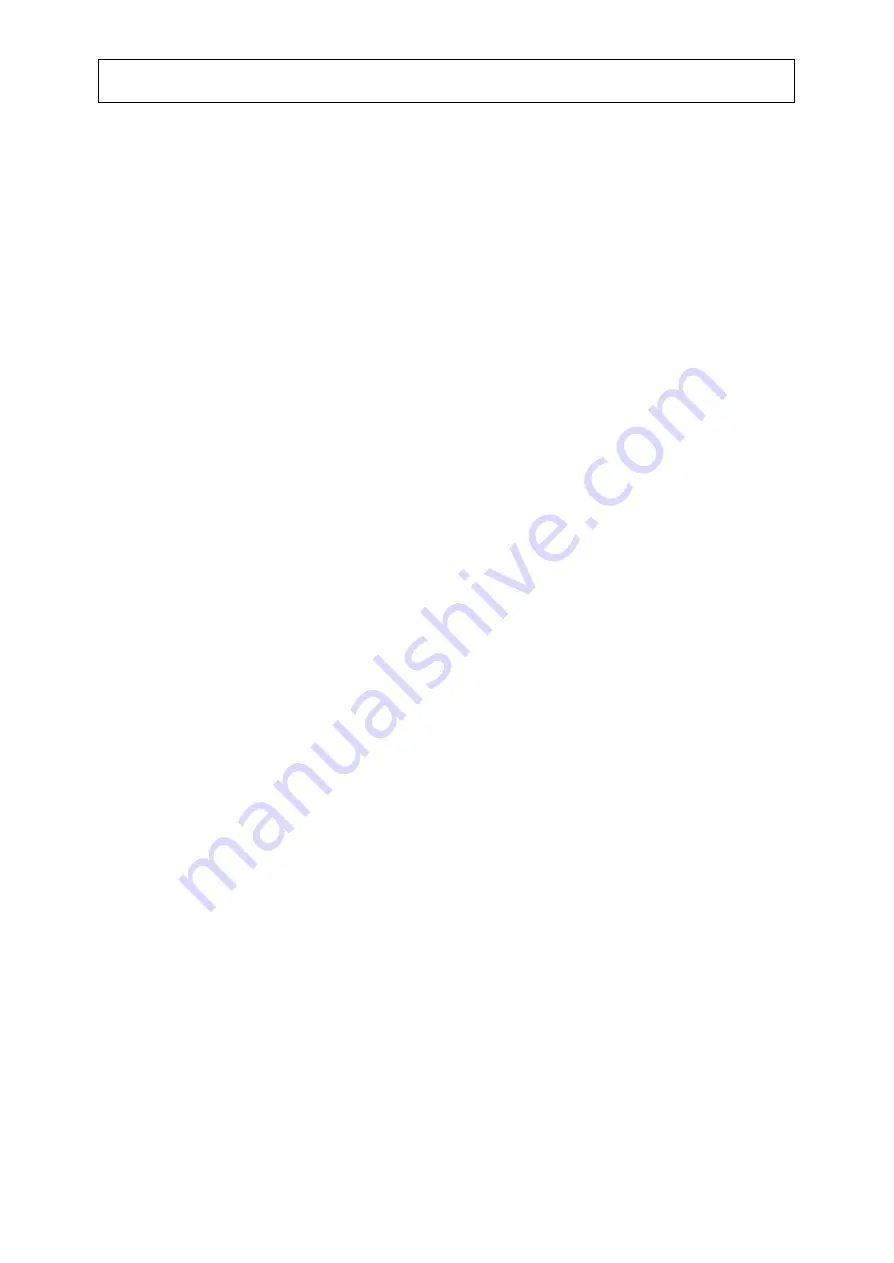
3.0 OPERATION
2. Start compressor(s), check the gages and note
if the pressures are within the prescribed
limits.
3. Check the refrigerant sight glass at the TX
Valve to be sure it is free of bubbles. If not,
charge as required to clean sight glass.
4. Stage unit down until all compressors are off
and check the compressor crankcase sight
glass for oil level. It should be 1/2 to 3/4 of
the compressor sight glass.
5. Restart the compressor. After an hour of
operation, the expansion valve superheat
setting should be checked, it should be
between 9° and 12°F at full load design
conditions. In some instances, it will be
necessary to lower the superheat setting to
ensure proper distribution. Turn the TX valve
adjustment stem clockwise to increase the
superheat setting and counterclockwise to
decrease the setting. Be sure and allow ample
time between each adjustment for the system
to rebalance.
6. The electrical control settings should be
checked and if necessary, reset to those
settings indicated on the wiring diagram.
Safety controls are factory set and must be
maintained at settings indicated on the wiring
diagram.
7. The temperatures of the chilled water both in
and out, should be checked to insure the unit
is operating within the desired temperatures.
3.6 SHUT-DOWN
(OVERNIGHT
OR WEEKEND)
To shut-down in the unit with compressors on or
off, turn each individual compressor switch. Do
not close any valve. The chilled water pump may
then be turn off. If it is possible that the
overnight ambient will drop below 65°F, it is
preferable to leave the chilled water pump on.
Finally, do not open the main unit disconnect.
Main power is required to keep the sump heaters.
3.7 SEASONAL SHUT-DOWN
PROCEDURE
Standard Ambient Units
1. Follow standard overnight
shut-down
procedure
2. Turn off chilled water pump
3. Close manual discharge valve
4. Close liquid valve on sealpot
5. If ambient temperature during the extended
shut-down period will not get below freezing,
the chilled water system may be left filled, If
the ambient temperature will be below
freezing, drain all water thoroughly, removing
all vent & drain plugs from both heads of the
evaporator, and blow out tubes will
compressed air to avoid serious stagnant
water corrosion.
6. Finally, it is recommended that an oil sample
be taken from each compressor & submitted
for lab analysis. Dunham-Bush offers this
service in its "Oil Kare" program. This
analysis should be done at the end of each
operating season or every 6 months if the unit
is used year round.
The power supply to the unit may be de-
energized to conserve energy. Just remember
that all heaters will now be inactive, and the
evaporator could freeze-up if not properly
drained.
3.8 SEASONAL START-UP
PROCEDURE
l. Check fan drives for wear, rust, propeller
clearance, etc. and make necessary repairs &
adjustments. Grease main fan shaft bearings
with a good grade of EP ball bearing grease.
2. Check & clean condenser fin surface if
necessary. Use a warm water soap solution,
being careful not to bend fins. Comb out bent
fin areas.
3. Check all power supply connections at all
points, and all control terminal screws for
tightness.
4. Energize main power to unit & leave on for at
least 24 hours in order for compressor to
thoroughly warm up.
5. Start chilled water pump and verify correct
flow-rate glycol % if required. Bleed-off
system air if necessary.
6. Open main discharge valve in discharge
header.
7. Open liquid valve on sealpot.
- 16 -
Summary of Contents for ACXi 165-5SP-LN
Page 6: ...2 0 INSTALLATION FIGURE 2 3 2 ACXi 165 5SP LN TYPICAL RIGGING 6...
Page 14: ...3 0 OPERATION FIGURE 3 2 ACXi 165 5SP LN TYPICAL SCHEMATIC PIPING 14...
Page 20: ...CHECKED REV NO DATE APPROV 4 0 ELECTRICAL FIGURE 4 2 ACXi 165 5SP LN WIRING SCHEMATIC 20...
Page 21: ...4 0 ELECTRICAL 21...
Page 22: ...4 0 ELECTRICAL 22...
Page 23: ...4 0 ELECTRICAL 23...
Page 24: ...4 0 ELECTRICAL 24...
Page 25: ...4 0 ELECTRICAL 25...
Page 26: ...4 0 ELECTRICAL 26...
Page 27: ...4 0 ELECTRICAL 27...
Page 28: ...4 0 ELECTRICAL 28...
Page 29: ...4 0 ELECTRICAL 29...
Page 30: ...4 0 ELECTRICAL 30...
Page 31: ...4 0 ELECTRICAL 31...