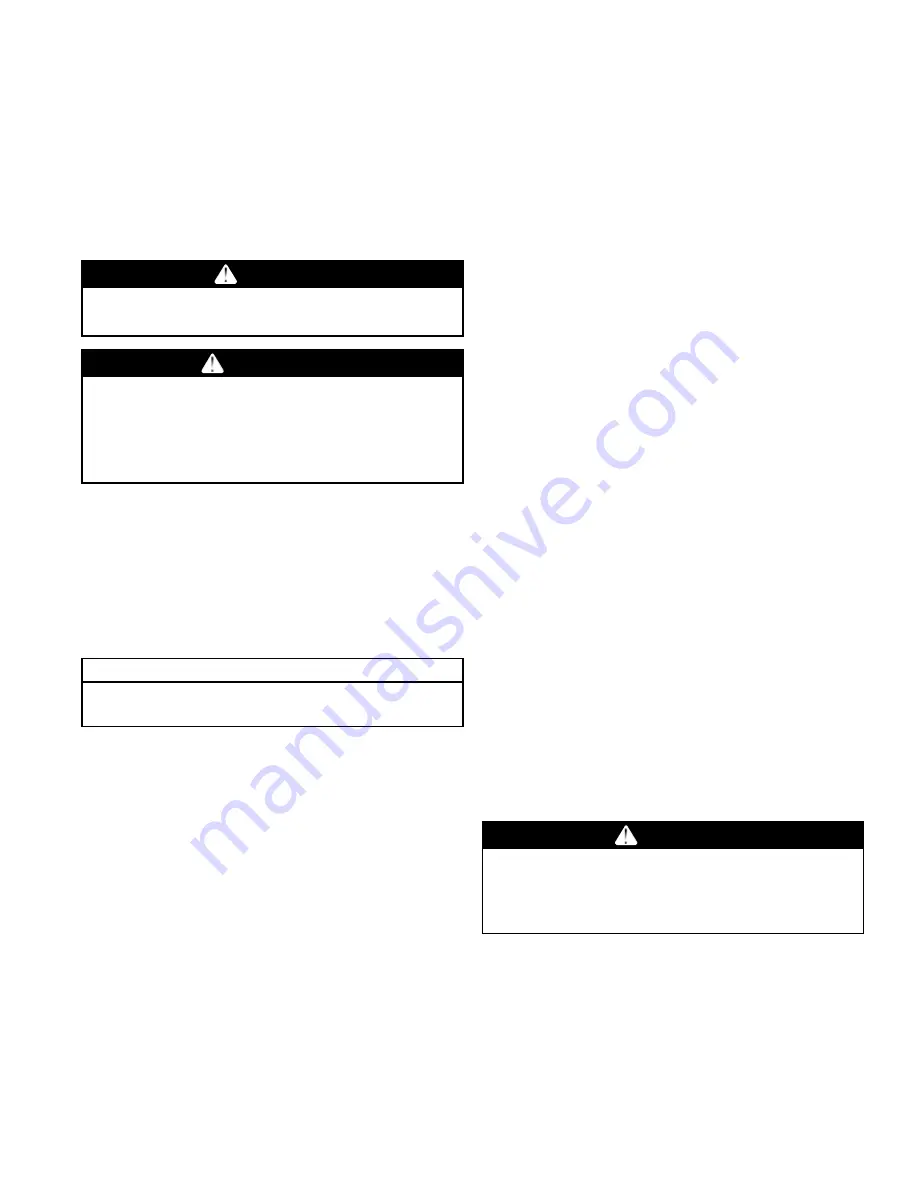
5
Section II
Installation
2-1. Installation Procedures
Use Figure 6-2 as a guide to properly attach the SPA
6415 DC actuator to your power source. Duff-Norton’s
PDC series control box or 2 SPDT Relays must be used
to avoid burning up the limit switches.
2-2. Limit Switch Adjustment
CAUTION
Disconnect power before making any adjustments to
the limit switches.
IMPORTANT
Before attempting to set limit switch nuts by these
instructions, be certain that the red and blue motor
leads and the switch leads are connected properly
per Figure 6-2. Unless leads are connected exactly as
shown, the following steps will be meaningless.
1. Setting Retracted Position
a. Do not install actuator in the intended application
at this time.
b. With nut retainer “A” installed in actuator and the
translating tube unstrained, operate actuator toward
retracted position until limit switch nut “B” trips limit
switch (see Figure 6-3).
NOTE
Translating tube may jam and rotate prior to tripping
limit switch.
c. Rotate the translating tube by hand until distance
between the housing clevis hole centerline and
the translating tube clevis hole centerline equals
the desired closed height. This centerline to
centerline dimension is not to be less than the
retracted centerline to centerline dimension listed
in Figure 1-6. If the two clevis end holes are not
oriented as required, rotate the translating tube
no more than 1/2 turn in either direction until they
are properly oriented.
d. Install actuator in application and check drift.
Slight readjustment in switch actuation may
be attained by removing nut restrainer “A” and
rotating limit switch nut “B” (1 notch of rotation =
.05 in. of screw travel). Replace nut restrainer,
“A”.
2. Setting Extended Position
a. Restrain the translating tube against rotation
by hand. Operate the actuator, toward the
extended position, until the distance between
the housing clevis hole centerline and the
translating tube clevis hole centerline equals
the desired extended height. This centerline
to centerline dimension is not to exceed the
extended centerline to centerline dimension listed
in Figure 1-6.
b. Remove nut restrainer “A” and rotate limit switch
nut “C” (see Figure 6-3) until it activates the limit
switch.
c. Replace nut restrainer “A”.
d. Install actuator in application and check the unit’s
drift. Slight readjustment in switch actuation may
be attained by removing nut restrainer “A” and
(1) rotating limit switch nut “B” to adjust retracted
position or (2) rotating limit switch nut “C” to
adjust extended position (1 notch of rotation =
.05 in. of screw travel).
e. After adjusting limit switch nuts, replace nut
restrainer “A”. Operate the actuator and readjust
limit switch nuts as necessary to achieve desired
travel.
2-3. Post-Installation Procedures
After actuator installation, position the air vent to prevent
moisture and dirt from entering the actuator. Vent can be
repositioned by loosening the set screw and rotating the
outer air tube into which the air vent is threaded. Spot drill
and re-tighten set screw.
If necessary, an elbow (1/8” female x 1/8” male pipe
thread) can be used for more effective positioning
CAUTION
Do not engage potentiometer shaft gear teeth with
plastic worm before reading the following procedure.
Failure to adhere to the following procedure could
cause damage to the potentiometer.
4. Retract actuator translating tube until stopped by limit
switch.
5a.
For travels up to 9” (single turn pot):
i. Turn pot shaft counterclockwise until resistance
between terminal
S and CCW is approximately 100
ohms. This will be the pot’s full retracted position.
ii. Being careful not to turn the pot shaft, slide it into
engagement with the plastic worm and tighten locknut.
Summary of Contents for TracMaster 6415 Series
Page 15: ...15 Notes...