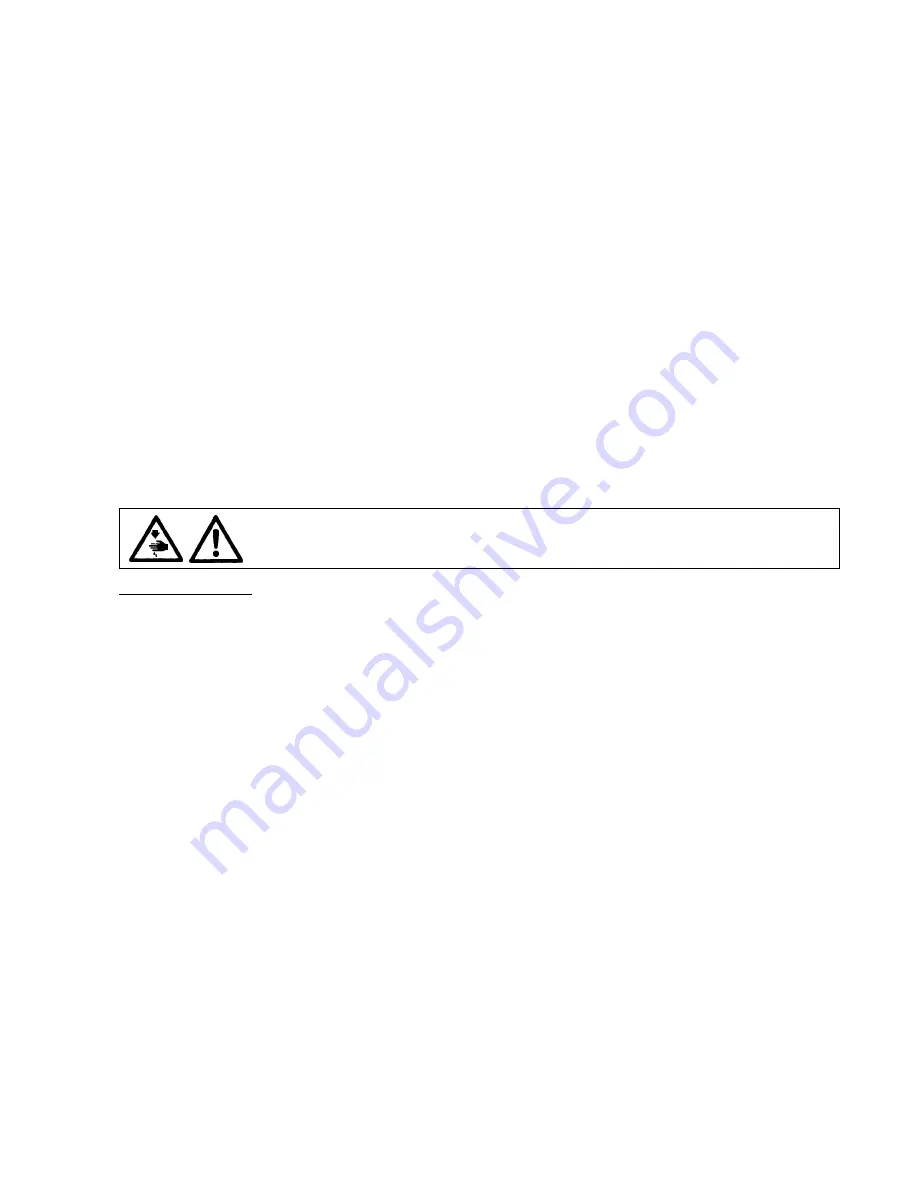
1
1. General safety instructions
The non-observance of the following safety instructions can cause bodily injuries or damages to the machine.
1. The machine must only be commissioned of the instruction book and operated by persons with appropriate training.
2. Before putting into service also read the safety rules and instructions of the motor supplier.
3. The machine must be used only for the purpose intended. Use of the machine without the safety devices is not permitted.
Observe all the relevant safety regulations.
4. When gauge parts are exchanged (e.g. needle, top roller, needle plate, feed dog and bobbin) when treading, when the
workplace is left, and during service work, the machine must be disconnected from the mains by switching off the master
switch or disconnecting the mains plug.
5. Daily servicing work must be carried out only by appropriately trained persons.
6. Repairs, conversion and special maintenance work must only be carried out by technicians or persons with appropriate
training.
7. For service or repair work on pneumatic systems the machine must be disconnected from the compressed air supply system.
Exceptions to this are only adjustments and functions checks made by appropriately trained technicians.
8. Work on the electrical equipment must be carried out only by electricians or appropriately trained persons.
9. Work on parts and systems under electric current is not permitted, except as specified in regulations DIN VDE 0105.
10. Conversion or changes to the machine must be authorized by us and made only in adherence to all safety regulations.
11. For repairs, only replacement parts approved by us must be used.
12. Commissioning of the sewing head is prohibited until such time as the entire sewing unit is found to comply with EC
directives.
It is absolutely necessary to respect the safety instructions marked by these signs.
Danger of bodily injuries !
Please note also the general safety instructions.
IMPORTANT WARNING
In spite of all safety measures made on the machines, inappropriate actions of the operator may lead to dangerous situations. In
industrial sewing machines Minerva, attention should be paid to the following still remaining possible sources of injury:
1. Moving sewing needle
- risk of injury when sewing with raised pressure foot or top roller, because the finger guard is then positioned too high.
2. Moving thread take-up lever
- risk of injury when inadvertently or intentionally inserting the finger(s) between the thread take-up lever and its guard.
3. Moving pressure member
- risk of injury when holding sewn work in immediate vicinity of the pressure member and beginning to insert under the
pressure member a considerably thicker sewn work portion,
- risk of injury when sinking the pressure member.
4. When switched off, the clutch motor slows down by inertia but would be reactivated by an accidental treading down of the
motor treadle. To avoid such risk, it is advised to hold the handwheel by hand and slightly to depress the motor treadle.
2. Introduction
This service book contains instruction for regulating the mechanisms of the sewing machine head.
The instructions for use and for putting the machine into operation and for the control of the stopmotor are not included in this
service book, but they are supplied as separate publications.
This service book is universal for all subclasses of the machine - it contains setting procedures for all elements which may be
placed on the machine of the given class. When the supplied subclass of this machine does not include some element, then it is
possible to leave out the respective parts of the instructions. The optional equipments of the machine and the respective
configurations of the subclasses of the machine are given in the operating instructions.
This sewing machine disposes of a large extent of its use. The machine should be set with respect to the parameters of the sewn
material, the sewing thread etc. The setting for the individual categories is given in the chapter 11.2.
For setting the machine, simple setting aids are used which are included in the accessory of the machine. Besides these aids,
universal measuring devices are used, such as slide calliper, feeler gauges and dynamometer for measuring the thread tension.