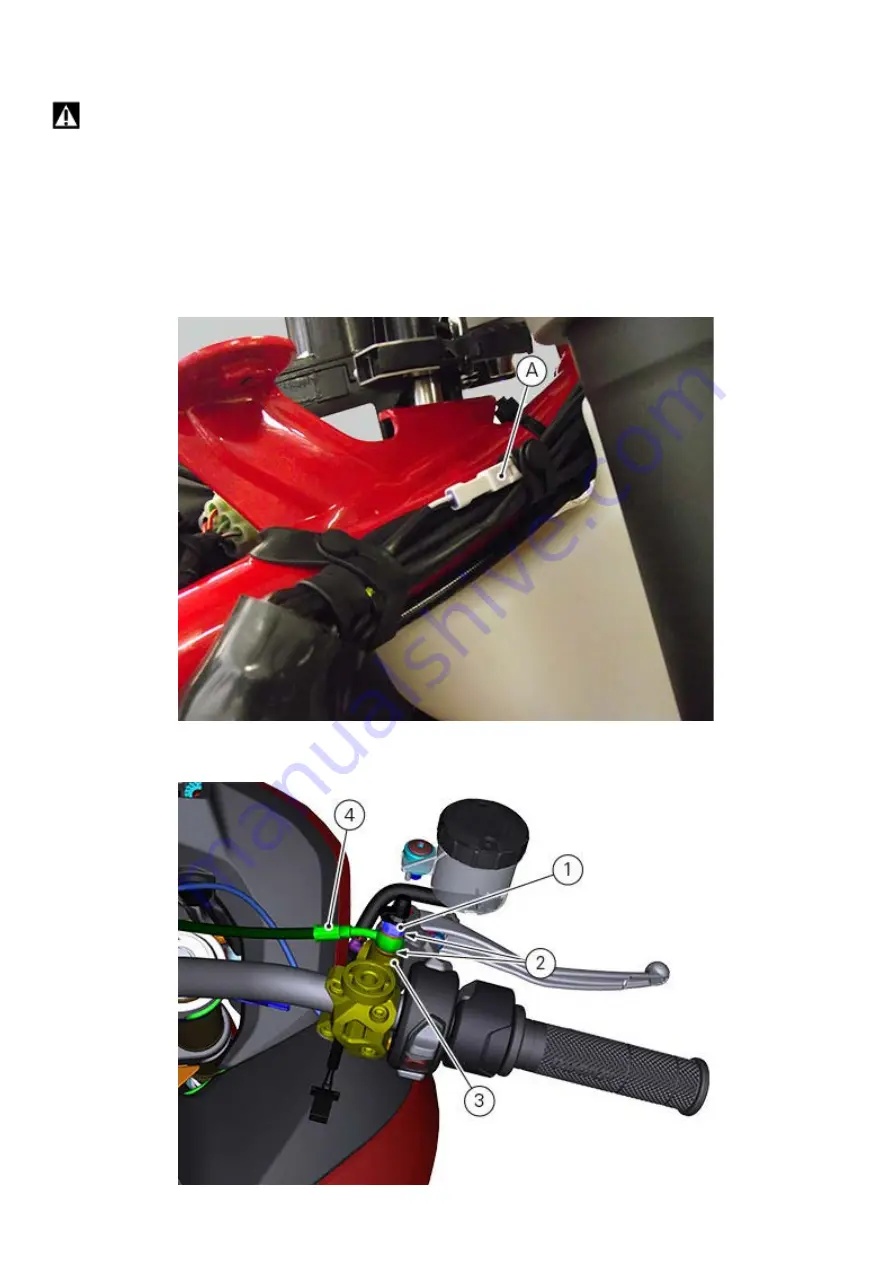
Removing the front brake master cylinder
Warning
The brake master cylinder manufacturer advises against servicing the brake master cylinder due to the safety
critical nature of this component. Incorrect overhaul can endanger rider and passenger safety. Maintenance
operations on these units are limited to replacement of the following parts: control lever, fluid reservoir assembly
and relative fasteners and master cylinder fasteners.
Drain the braking system (
Changing the front brake system fluid
).
Remove the rear-view mirrors (
Removing the rear-view mirrors
).
Remove the tank filler plug cover (
Removing the tank fairings
).
Disconnect the front brake switch connector (A) from the main wiring harness.
Undo the special screw (1), collecting the sealing washers (2) to release the front brake master cylinder unit (3)
from hose (4).
Summary of Contents for MULTISTRADA 1200S ABS 2015
Page 21: ...Injection system Make Type Control unit BOSCH ME7921...
Page 39: ...Dimensions...
Page 63: ...88713 5009 TDC control tool 8876 1737 Camshaft locking tool...
Page 71: ......
Page 83: ...Remove the brake pads 3 by pushing the calliper pistons fully inside their seats...
Page 84: ...Fit the new pads Insert pin 2 and fix it by means of the safety split pin 1...
Page 93: ...Refit the rear splash guard Refitting the splash guard...
Page 95: ......
Page 109: ...Refit the LH and RH panel Refitting the panel...
Page 115: ...Refit the fuel tank Refitting the fuel tank...
Page 117: ......
Page 121: ...Fit the belt 7 as shown in the figure using a screwdriver to tension it...
Page 123: ...Remove tool C part no 88765 1737 and fit it on the horizontal head...
Page 131: ...camshaft lobe B...
Page 137: ...Position O ring 7 on the crankcase and O ring 6 on the mesh filter 5...
Page 138: ...Refit the mesh filter 5...
Page 139: ...Apply a bead of sealing compound to cover 7 as shown in the figure...
Page 141: ...Refit the complete belly pan Refitting the belly pan...
Page 144: ...Fit clips 4 in the indicated areas of the central panel 5 Force ball joint 6 into its seat...
Page 147: ...Fit two rubber plugs 12 in the indicated holes Insert plugs 13 in recesses 14...
Page 152: ......
Page 155: ...Connect the immobilizer antenna by means of connector 1...
Page 156: ......
Page 159: ...Disconnect the power socket 7 and remove the panel...
Page 165: ...Fix the side conveyor 4 by tightening screws 3 to a torque of 2 Nm 10...
Page 167: ...U S A VERSION...
Page 168: ......
Page 170: ...Loosen screws 3 and remove conveyor 4 Repeat this operation on the other conveyor...
Page 171: ...Loosen screws 5 from both sides of the tank cover 7...
Page 172: ...Loosen the two upper screws 6 Remove the tank cover 7 by sliding it upwards...
Page 173: ......
Page 179: ...Position support 2 by inserting U bolt 23 in tooth 24 of the tank cover on the upper side...
Page 183: ......
Page 188: ......
Page 190: ......
Page 193: ......
Page 196: ......
Page 197: ...Start screws 1 with the relevant washer 2 and tighten them to a torque of 5 Nm 10...
Page 200: ......
Page 202: ......
Page 207: ...Tighten the screw 5 to a torque of 24 Nm 10...
Page 208: ...Tighten screws 14 and 15 to a torque of 5 Nm 10...
Page 210: ...Tighten the screw 5 to a torque of 24 Nm 10...
Page 212: ......
Page 214: ...Fit mudguard 2 by starting screws 1 with spacers Tighten the screws 1 to a torque of 3 5 Nm 10...
Page 215: ...FRONT MUDGUARD HALF KIT Refit half mudguard 8 by tightening screws 7 to a torque of 3 5 Nm 10...
Page 220: ...Loosen the two screws 7 and remove the half mudguard 8...
Page 221: ...If mudguard half 8 has not been installed remove bracket 9 by loosening screws 7...
Page 222: ......
Page 224: ......
Page 226: ......
Page 228: ......
Page 229: ......
Page 231: ......
Page 233: ......
Page 234: ......
Page 235: ......
Page 236: ...Table 10B POS DESCRIPTION 4 Ground cable...
Page 237: ...Table 10C POS DESCRIPTION...
Page 238: ...4 Horizontal head spark plug 5 Horizontal head coils...
Page 239: ...Table 10D POS DESCRIPTION 6 Vertical head spark plug 7 Vertical head coils...
Page 240: ......
Page 241: ...ROUTING OF WIRING ON FRAME...
Page 243: ...Table 9C POS DESCRIPTION...
Page 245: ......
Page 246: ......
Page 247: ......
Page 249: ...ROUTING OF WIRING ON FRAME...
Page 251: ...ROUTING OF WIRING ON FRAME...
Page 254: ...ROUTING OF WIRING ON FRAME...
Page 256: ......
Page 257: ...ROUTING OF WIRING ON FRAME...
Page 258: ...Branch 5...
Page 259: ...Table 5A POS DESCRIPTION 1 Water temperature sensor cable 2 Pick up cable...
Page 260: ......
Page 261: ...Table 5B POS DESCRIPTION 3 Vertical oxygen sensor cable 4 Side stand cable...
Page 262: ......
Page 263: ...ROUTING OF WIRING ON FRAME...
Page 265: ...TABLE 4B POS DESCRIPTION...
Page 267: ...ROUTING OF WIRING ON FRAME...
Page 268: ...Branch 3 Table 3A POS DESCRIPTION 1 Purge valve cable...
Page 269: ...Table 3B POS DESCRIPTION 2 ABS control unit cable...
Page 270: ...Table 3C POS DESCRIPTION...
Page 272: ...Table 3D POS DESCRIPTION...
Page 274: ...Table 3E POS DESCRIPTION 8 Horn cable 9 Horizontal map sensor cable...
Page 275: ...Table 3F POS DESCRIPTION...
Page 276: ...10 Horizontal oxygen sensor cable...
Page 277: ...Table 3G POS DESCRIPTION 11 LH fan cable...
Page 278: ...Table 3H POS DESCRIPTION...
Page 279: ...12 RH fan cable ROUTING OF WIRING ON FRAME...
Page 281: ...Table 2B POS DESCRIPTION...
Page 283: ...Table 2C POS DESCRIPTION...
Page 285: ...Table 2D POS DESCRIPTION 9 Fuel pump cable 10 Bluetooth cable IF ENABLED ONLY...
Page 286: ...ROUTING OF WIRING ON FRAME...
Page 288: ...TABLE 1C POS DESCRIPTION 5 Air temperature sensor cable...
Page 289: ...TABLE 1D POS DESCRIPTION 6 12V power outlet...
Page 290: ...TABLE 1E POS DESCRIPTION 2 Oil temperature sensor cable 3 Oil pressure switch cable...
Page 291: ...ROUTING OF WIRING ON FRAME...
Page 292: ...ROUTING OF WIRING ON FRAME MAIN BRANCHES...
Page 293: ...MAIN WIRING POSITIONING Position main wiring as shown in the figure...
Page 294: ......
Page 308: ......
Page 318: ......
Page 324: ......
Page 333: ...Main fuses key Pos El item Rat A Main fuse 30 A A Spare 30 A ELECTRIC DIAGRAM...
Page 337: ......
Page 342: ...ELECTRIC DIAGRAM...
Page 345: ......
Page 347: ......
Page 351: ......
Page 353: ...ELECTRIC DIAGRAM...
Page 358: ......
Page 363: ...Bottom yoke front sensor Rear sensor...
Page 364: ......
Page 366: ...ELECTRIC DIAGRAM...
Page 368: ......
Page 370: ...Vertical head...
Page 373: ...ELECTRIC DIAGRAM Horizontal oxygen sensor Vertical oxygen sensor...
Page 374: ......
Page 379: ......
Page 382: ......
Page 385: ......
Page 388: ...Throttle Position System TPS In the Multistrada the TPS is integrated in the ETV...
Page 393: ......
Page 399: ......
Page 414: ......
Page 420: ......
Page 423: ......
Page 434: ......
Page 436: ......
Page 443: ......
Page 484: ......
Page 496: ...Fit spacer 7 in the wheel Apply the recommended grease on wheel shaft 6 thread included...
Page 497: ...Fit the complete wheel between the fork bottom ends Take pin 6 fully home into the wheel hub...
Page 506: ...If the values measured are not within the tolerance limits replace the wheel...
Page 509: ...Loosen the wheel shaft retaining screws 5 on both fork bottom ends...
Page 511: ...Working on both sides remove the sealing ring 9...
Page 512: ......
Page 516: ......
Page 518: ......
Page 520: ......
Page 526: ...Refit the wheel on the motorcycle Refitting the front wheel...
Page 532: ......
Page 546: ......
Page 548: ...Refit the rear brake control 7 and the bracket 5 that retains the rear stop light 1...
Page 550: ...Fill the rear braking system Changing the rear brake system fluid...
Page 553: ...Undo pin 6 securing the brake lever 7 collecting spring 8...
Page 554: ...Slide out the brake lever 7 and collect pin 6 bushing 11 and O rings 9...
Page 564: ......
Page 566: ...TABLE B...
Page 567: ...TABLE C...
Page 568: ...TABLE D...
Page 569: ...TABLE E TABLE F...
Page 570: ...TABLE G TABLE H...
Page 571: ......
Page 579: ...Connect the connector 1...
Page 580: ...Refit the rear mudguard Refitting the rear mudguard Refit the rider seat Refitting the seat...
Page 584: ......
Page 591: ......
Page 594: ...Fit switch 2 fully home on support 3 Check that the switch is actually blocked...
Page 596: ...Tighten screws 9 to a torque of 2 8 Nm 10...
Page 603: ...Insert tool A inside seat 1 of switch 2 Push tool A until releasing switch 2...
Page 606: ......
Page 608: ......
Page 610: ......
Page 614: ...Connect the throttle control cable 3 to the switch...
Page 615: ...Position the hand guard 1 by tightening screw 2 to a torque of 10 Nm 10...
Page 617: ......
Page 628: ...Component A Component B...
Page 629: ......
Page 632: ......
Page 634: ......
Page 637: ......
Page 647: ......
Page 655: ...Remove the circlip 17 Slide out fork leg 19 from fork leg 1...
Page 658: ......
Page 661: ...Tighten the upper plug 3A on the damper rod while holding lock nut 2A with a wrench...
Page 664: ......
Page 668: ......
Page 671: ......
Page 677: ......
Page 686: ......
Page 688: ......
Page 692: ......
Page 695: ...Warning The maximum swinging arm rear end play is within 1 mm...
Page 700: ...Chain guard Undo the screws 10 to remove the chain guard 11 from the swinging arm 9...
Page 701: ......
Page 709: ...Remove the second washer 6 Slide out the eccentric hub 9 from swinging arm chain side...
Page 715: ...Using a mallet tap the sprocket flange 4 with the cush drive damper 7 off the rear sprocket 5...
Page 719: ......
Page 726: ......
Page 733: ...Connect the side stand switch connector A to the main wiring...
Page 734: ......
Page 739: ...Refit the side panels Refitting the panel...
Page 747: ...Loosen ring nut 12 of the adjuster Remove the two lateral plates 13...
Page 748: ......
Page 750: ......
Page 756: ...Insert the number plate holder assembly 5 in the rear subframe and fix it with screws 4...
Page 757: ...Connect the connector 3...
Page 760: ...Remove the number plate holder 5...
Page 761: ......
Page 763: ...Tighten the two screws 20 securing voltage regulator 21 Fit washer 22 and tighten with nut 23...
Page 765: ...Fit plate 26 by engaging lock tabs A and B in the recesses...
Page 775: ...Remove electrical components compartment 8...
Page 777: ...Reconnect the fuel pump connector 4 and hose 6 Grip and press flange A to insert hose 6...
Page 778: ...Reconnect the fuel level connector 3 and reposition the clips 1...
Page 780: ......
Page 781: ...Positioning the fuel tank drain pipe...
Page 782: ......
Page 783: ......
Page 784: ...Positioning the fuel pipes...
Page 785: ......
Page 788: ...Insert plug 8...
Page 795: ......
Page 797: ......
Page 802: ...REFITTING THE AIR FILTER Position filter 20 as shown in the figure...
Page 808: ......
Page 810: ......
Page 812: ......
Page 814: ...Refit the tank Refitting the tank...
Page 817: ......
Page 819: ...Loosen clamp 14 that keeps the airbox against the horizontal cylinder head 15...
Page 820: ...Loosen clamp 16 that keeps the airbox against the vertical cylinder head 17...
Page 822: ...REMOVING THE THROTTLE BODY Loosen screws 21 retaining the upper airbox 22...
Page 825: ......
Page 840: ...Position the retaining spring 10 Tighten clip 11 to a torque of 18 Nm 10...
Page 841: ...Reconnect the two lambda sensors 9 and 8...
Page 842: ...Position control cable 5 in plate 7...
Page 846: ......
Page 848: ...Remove retaining spring 10 of the horizontal exhaust pipe 1...
Page 851: ......
Page 854: ...Tighten the screw 3 to a torque of 5 Nm 10 Tighten clip 2 to a torque of 22 Nm 10...
Page 857: ......
Page 859: ...Fit canister filter 5 from the top It must be fitted into plate 7 guides 6...
Page 860: ...Reconnect pipes 1 and 2 and fix them with clamps 3 and 4 POSITIONING THE CANISTER FILTER PIPES...
Page 861: ......
Page 862: ......
Page 864: ......
Page 866: ...Work on the vertical head and remove clip 10 and disconnect pipe 11...
Page 868: ......
Page 877: ......
Page 879: ......
Page 881: ......
Page 885: ...Position pipes 5 as shown in the figure C delivery D return...
Page 886: ......
Page 891: ...Upon disassembly make sure not to lose the O rings A that guarantee the coupling sealing...
Page 893: ......
Page 898: ......
Page 900: ...Position hose 2 on the radiator with clip 1 and tighten clip 1 to a torque of 1 Nm 10...
Page 902: ......
Page 904: ...Loosen the clamps 1 to remove the hoses 2 and 5 from the tank 4...
Page 905: ......
Page 912: ......
Page 913: ......
Page 917: ...Undo the screws 12 and remove the water union 13 and recover clip 14...
Page 921: ......
Page 922: ...Reconnect the fan wiring to the main wiring C and D...
Page 928: ...Remove water radiator 4 from the vehicle by disengaging it from pin E...
Page 930: ......
Page 947: ...camshaft lobe B...
Page 954: ...Fit the belt 7 as shown in the figure using a screwdriver to tension it...
Page 956: ...Remove tool C part no 88765 1737 and fit it on the horizontal head...
Page 963: ...Insert the pulley fully home on the camshaft by centring pin 8 in hole C...
Page 967: ......
Page 970: ...Fit the first key 4 on the timing layshaft Locate the inner pulley 3...
Page 974: ...Remove the first key 4 from the timing layshaft Remove the spacer 5 and the inner pulley 3...
Page 975: ...Remove the inner spacer 6 and second key 4 on the timing layshaft...
Page 976: ...It is now possible to remove the snap ring 7 on the timing layshaft...
Page 977: ......
Page 980: ...Loosen the two retaining screws 5 and remove the two pulleys...
Page 983: ...Using suitable tools lift up plug 3 to remove it...
Page 984: ...Loosen the fastening screws 4 and 5 on the main cover 6...
Page 987: ......
Page 993: ...If previously removed install the oil flow pin 20 using suitable tools...
Page 994: ...Cylinder head cover Apply the indicated sealant on the four highlighted points...
Page 995: ......
Page 1001: ......
Page 1003: ...Remove the gaskets 7 and 8...
Page 1005: ......
Page 1006: ......
Page 1022: ...Locate the closing rocker arm 4 and drive the shaft 3 home...
Page 1027: ......
Page 1028: ...Withdraw the shafts 7 of the closing rocker arms on the exhaust and intake sides...
Page 1029: ...Remove the closing rocker arms 5 the springs 6 with the spacers 8...
Page 1034: ...Fit the opening shims 1...
Page 1035: ...Repeat the same procedure for the other valves...
Page 1044: ...Push the cylinder 4 down until it seats against the crankcase Refit bushings 7 and O ring 11...
Page 1052: ...First ring S...
Page 1053: ...Second ring T Oil scraper ring R...
Page 1060: ...Refitting the clutch Insert guide 14 Locate the clutch housing 13 and the spacer 12...
Page 1065: ...Insert the control pin 6 in the bearing 7 and the latter in the gearbox primary shaft...
Page 1070: ......
Page 1074: ......
Page 1075: ...Slide out the spacer 12 Slide out the clutch housing 13...
Page 1076: ...Slide off the guide 14...
Page 1083: ......
Page 1092: ...Remove the ring nut 3 and the lock washer 4...
Page 1094: ......
Page 1096: ...Note There are two types of springs therefore pay attention to the installation seats...
Page 1104: ......
Page 1106: ......
Page 1109: ...Fit the 3th speed gear 12...
Page 1111: ......
Page 1114: ......
Page 1119: ...Disassembling the gearbox primary shaft Remove washer 18 from the primary shaft 17...
Page 1122: ......
Page 1126: ......
Page 1129: ...Block the flywheel rotation with the suitable tool no 88713 3367 Fit washer 5...
Page 1135: ......
Page 1136: ......
Page 1138: ...Remove the flywheel unit 6 and the driven gear 7...
Page 1139: ...Remove the roller bearing 7 and bushing 8 Remove gear 9...
Page 1140: ......
Page 1147: ...If necessary fit the water pump assembly Refitting the water pump...
Page 1153: ......
Page 1169: ...To remove the engine sensor 10 undo the screw 11 and collect the washer 12...
Page 1171: ......
Page 1175: ...Make sure that the two centring bushes A are correctly fitted on the crankcase...
Page 1179: ...Fit the two spacers B with the chamfered side facing the crankshaft...
Page 1191: ...Fit the oil seal 6 by respecting the values indicated in the figure...
Page 1193: ...TIMING LAYSHAFT BEARING 7 Fit bearing 7 and fix it with snap ring 8...
Page 1196: ...NEEDLE ROLLER BEARINGS 10 FOR SWINGARM SHAFT...
Page 1200: ...TIMING LAYSHAFT BEARING 20...
Page 1201: ...Fit bearing 20 and fix it with snap ring 21...
Page 1203: ...Fit the sealing ring 23 TIMING SHAFT SEAL RING 26...
Page 1204: ...Lubricate seal 26 using the specified product...
Page 1206: ......
Page 1208: ...Make sure that opening C is in a diagonally opposed position of machining D of bush 2...
Page 1210: ...GENERATOR SIDE MAIN BEARING...
Page 1213: ......
Page 1215: ...Undo the two retaining screws 2 and recover spacers 3 Remove the bearing 1...
Page 1216: ...PRIMARY SHAFT BEARING 4 Remove the internal ring 5 Remove the bearing 4...
Page 1217: ...Remove the sealing ring 6...
Page 1218: ...TIMING LAYSHAFT BEARING 7 Remove the snap ring 8 Remove the bearing 7...
Page 1219: ...Generator side external part Side A SECONDARY SHAFT OIL SEAL 9...
Page 1222: ...SECONDARY SHAFT BEARING 18...
Page 1223: ...Remove the internal ring 19 Remove the bearing 18...
Page 1224: ...TIMING LAYSHAFT BEARING 20 Remove the snap ring 21 Remove the bearing 20...
Page 1225: ...Clutch side external part Side D NEEDLE ROLLER BEARINGS 22 FOR SWINGARM SHAFT...
Page 1227: ...Remove the sealing ring 26...
Page 1231: ...Loosen screw 11 remove the lubrication valve 12 and collect the O ring 13...
Page 1237: ......
Page 1248: ...In order to correctly couple big end bearings 6 and crank pin 7 proceed as follows...