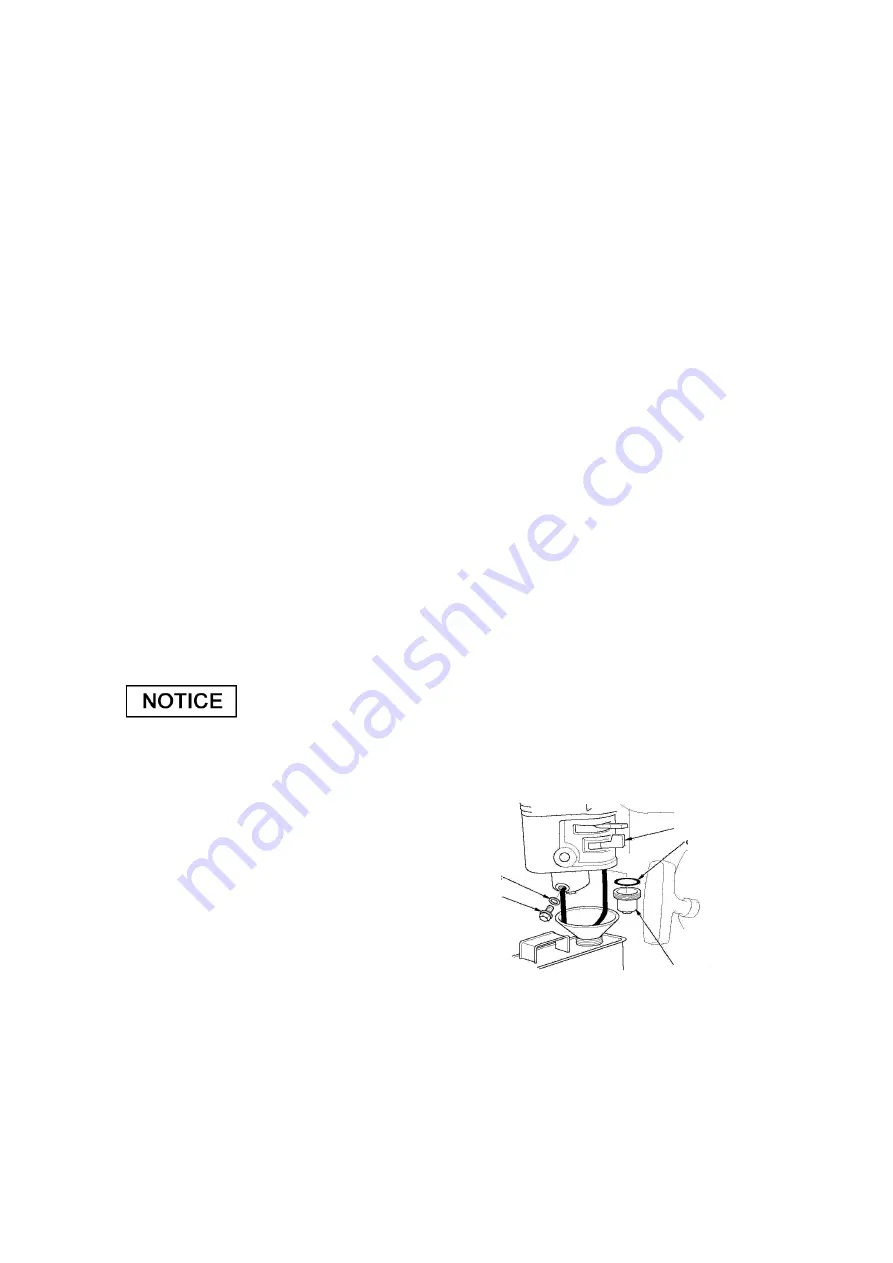
25
and other fuel system components serviced or replaced.
The length of time that gasoline can be left in your fuel tank and carburetor
without causing functional problems will vary with such factors as gasoline blend,
your storage temperatures, and whether the fuel tank is partially or completely
filled. The air in a partially filled fuel tank promotes fuel deterioration. Very warm
storage/temperatures accelerate fuel deterioration. Fuel deterioration problems
may occur within a few months, or even less if the gasoline was not fresh when
you filled the fuel tank.
The Distributor’s Limited Warranty does not cover fuel system damage or engine
performance problems resulting from neglected storage preparation.
You can extend fuel storage life by adding a fuel stabilizer that is formulated for
that purpose, or you can avoid fuel deterioration problems by draining the fuel
tank and carburetor.
Adding a Fuel Stabilizer to Extend Fuel Storage Life
When adding a fuel stabilizer, fill the fuel tank with fresh gasoline. If only partially
filled, air in the tank will promote fuel deterioration during storage. If you keep a
container of gasoline for refueling, be sure that it contains only fresh gasoline.
1. Add fuel stabilizer following the manufacturer’s instructions.
2. After adding a fuel stabilizer, run the engine outdoors for 10 minutes to be sure
that treated gasoline has replaced the untreated gasoline in the carburetor.
Dry operation will damage the pump seal. Be sure the pump
chamber is filled with water before starting the engine.
3. Stop the engine, and move the fuel valve lever to the OFF position.
Draining the Fuel Tank and Carburetor
1. Place an approved gasoline container
below the carburetor, and use a
funnel to avoid spilling fuel.
2. Remove the carburetor drain
bolt and sediment cup, and
then move the fuel valve lever
to the ON position.
3. After all the fuel has drained into the container, reinstall the drain bolt and
sediment cup. Tighten them securely.
O-RING
FUEL VALVE LEVEL
WASHER
DRAIN BOLT
SEDIMENT CAP