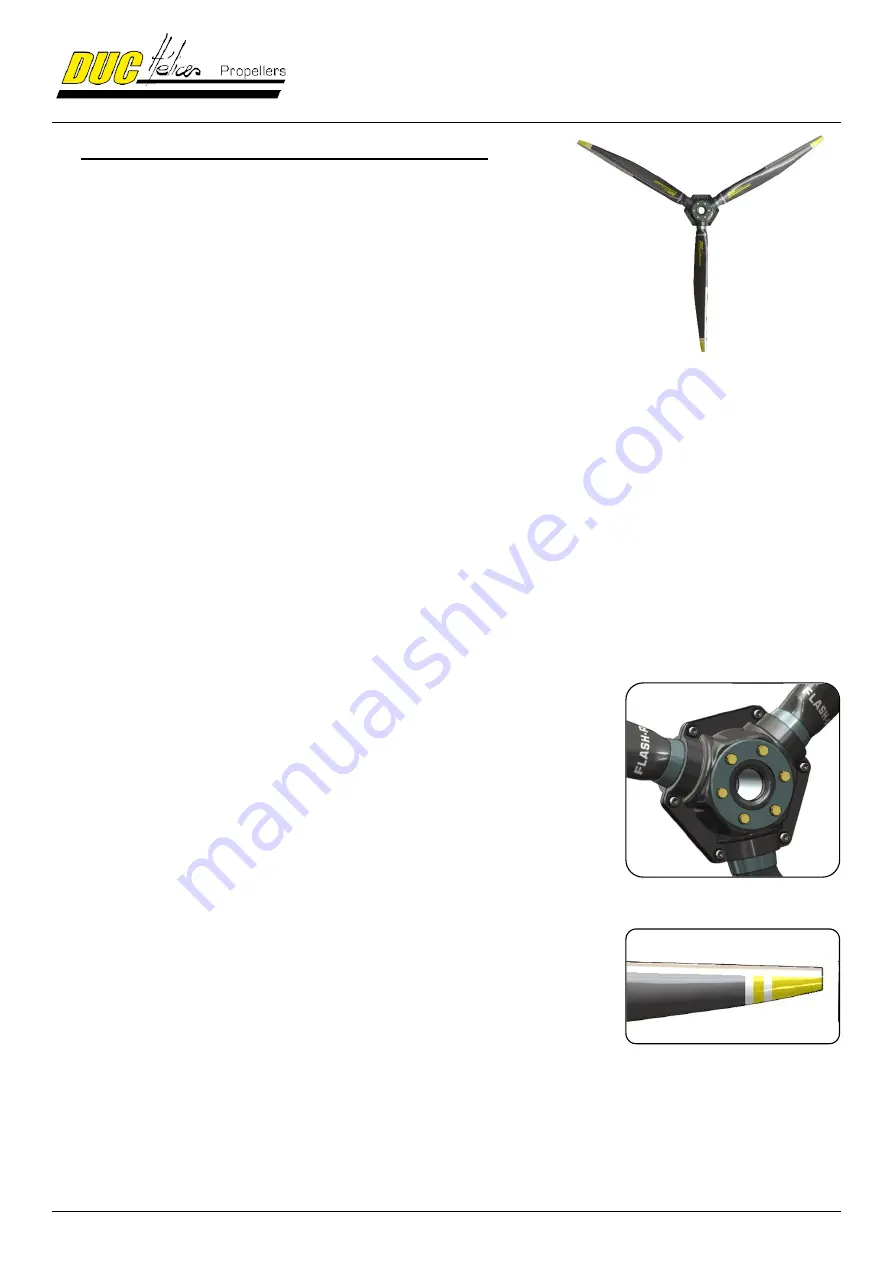
Certified FLASH-R
4/27
1. Presentation of the Certified FLASH-R propeller
Description
1.1.
The
certified
FLASH-R
propeller has a new innovative design,
specific about its twisting axis and center of pressure.
Its aerodynamic design allows a
"Constant Speed" effect
, limiting
variations in engine speed between on ground and in flight.
This propeller allows
high efficiency
throughout the flight envelope i.e.:
Improved takeoff and climb rate due to higher engine speed, then higher engine efficiency
Many cruise extension
A high user comforts
The blades and the hub of the FLASH-R propeller are manufactured according the DUC Hélices company
technologies, from unidirectional layers of carbon fibers prepreg epoxy resin.
The blade composite structure is defined to obtain the
maximum strength in torsion and bending
. Therefore
"constant speed" effect is not related to deformation of the blade but its geometry and specific profile.
Due to its
specific geometric definition
,
excellent performance
is obtained in
both aerodynamic and acoustic,
but also in consumption
.
Characteristics
1.2.
The Certified FLASH-R propeller range is available:
Ground adjustable propeller
Tractor configuration available in right rotation
Diameters Ø1520 to Ø1900mm (Ø59.8 to Ø74.7")
Shielded leading edge in Inconel
®
Carbon composite hub with metallic inserts
Protected again lightning strike
Direct assembly on the propeller-shaft Ø101.6mm
Safety marking on the tip of the propeller
Summary of Contents for FLASH-R
Page 26: ...26 27 ...
Page 27: ......