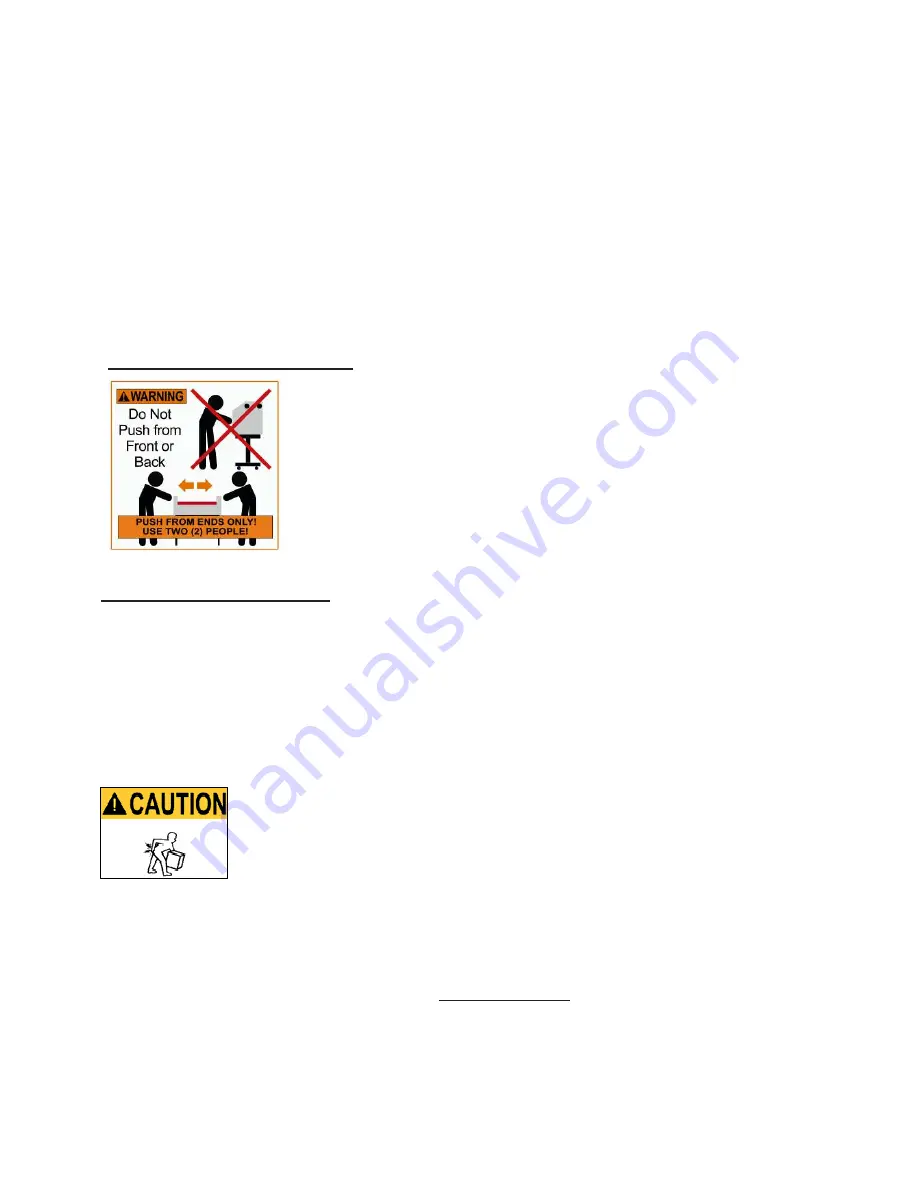
7
The noise level this machine generates at the operators’ position is less than 70dB.
Keep this manual near the machine for future reference. Also check our website for any
additional or updated safety information. (www.drytac.com)
Installation/Training is also available for your
JetMounter
™
. This service assures that your new
laminator is set up properly and the operators are trained in the various applications the
equipment can perform. Contact our Customer Service Department for details or if you have
any questions about the operation of this equipment or would like to make arrangements for
such a session.
Specific Moving Instructions
The Drytac JetMounter
TM
is to be handled with care to avoid personal
injury or collateral damage. Whenever the machine is moved, we
strongly recommend utilizing at least two people. The adage: “Better
safe than sorry,” applies here. When moving the machine, the
movers should be positioned at both sides. Do not push the
JetMounter
TM
from the front or back! This eliminates the possibility
of having the machine tip over onto the mover or their helper.
Unpacking and Installation
Upon receipt of your new JetMounter
™
, inspect the carton(s) carefully for signs of physical
damage or mishandling. There are two rough handling indicators that should be inspected
before the shipment is signed for. If either of the devices is “tripped”, this must be noted on the
receiving paperwork. Report any damage to the shipping company immediately and contact
Drytac Corporation if replacement parts are needed. If there is no apparent damage, proceed
with unpacking.
It is recommended that at least two people unpack the JM Pro XD to avoid
damage to the equipment or personal injury. Follow the instructions attached
to the front of the crate to remove the laminator correctly and safely. If the
instructions are missing check the appendix in this manual for an illustrated
version or contact Drytac Technical Services before attempting to unpack or install the machine.
Also see appendix for heating element installation procedure. If there are any questions about
electrical requirements for the equipment, please contact a qualified electrician prior to
attempting to power up the machine! Be absolutely certain that the voltage supplied at the
outlet corresponds with the voltage marked on the plate attached to your machine. Do not rely
on the cord or outlet configuration to determine the correct power supply voltage!
Summary of Contents for JetMounter Pro
Page 1: ...OPERATOR S MANUAL 9 16 16 ...