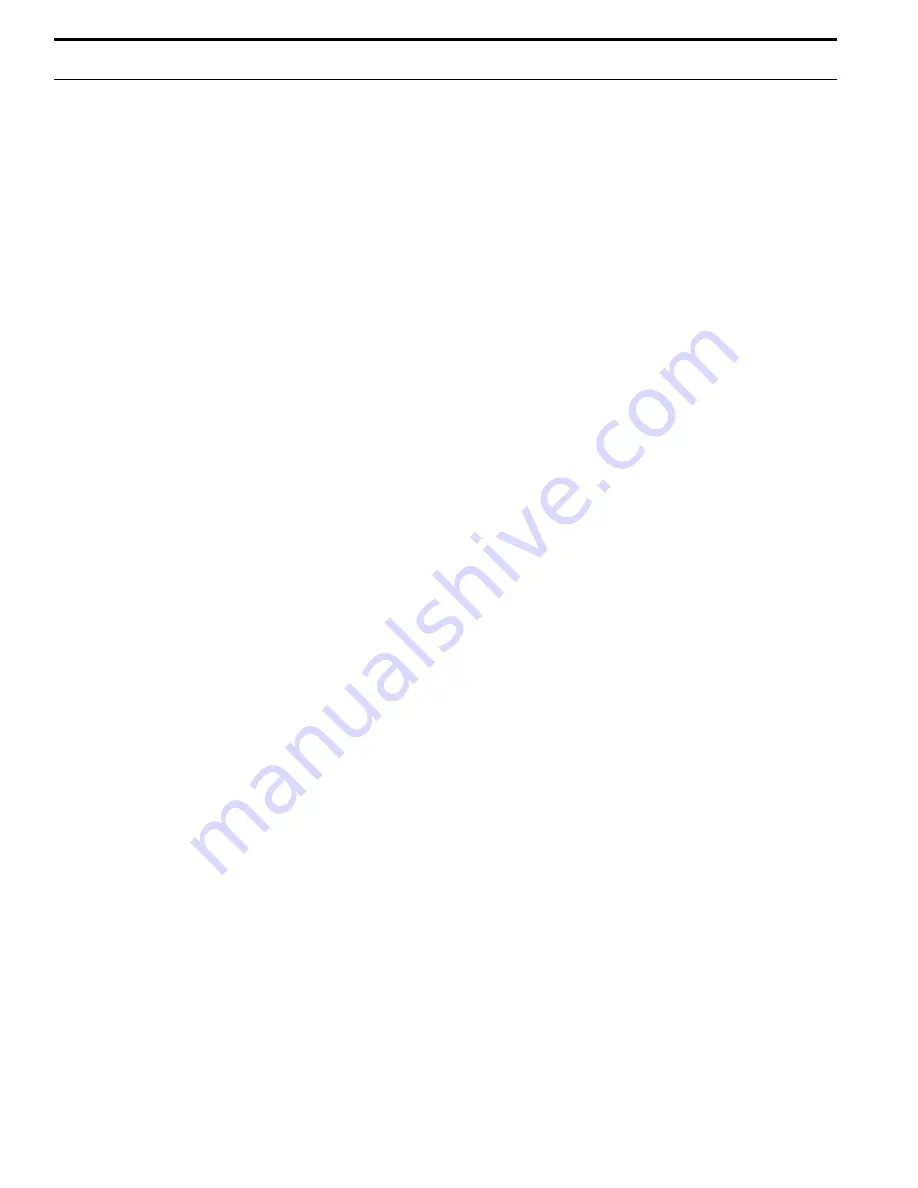
12
MAINTENANCE
Standard water models (VAPORMIST, cont.)
Off-season shut-down procedure
1.
Switch off electrical power.
2.
Remove enclosure.
3.
Shut off water supply to makeup valve.
4.
Drain evaporating chamber, and clean if necessary
(see “To inspect and service” on previous page).
5.
Replace enclosure.
6.
Leave chamber dry, the power off and the
water shut-off valve closed until the next
humidification season.
DI water models (VAPORMIST DI)
The VAPORMIST DI unit uses DI/RO water. Because
these water types are mineral-free, cleaning of the
evaporating chamber should not be necessary. However,
there are some simple maintenance steps that should be
followed to ensure all parts of the unit are in working
order.
To inspect and service
1.
Remove the evaporating chamber.
•
Remove the two fasteners on each side of the
cover enclosure.
•
Remove the enclosure.
•
Do not remove the electrical panel cover or
heater terminal cover until electrical power
is disconnected. Safety first.
•
If the VAPORMIST has a space distribution
unit (SDU) mounted directly above it, the
SDU cover must be removed before
removing the unit cover.
•
If the tank is hot, cool it down by opening the
manual ball valve on the side of the tank.
The float valve will open allowing cool water
to run into the tank until it is cool enough to
handle.
•
Shut off the water supply.
•
Shut off the electrical supply.
•
Allow the tank to drain completely.
•
Disconnect the fill line at the fill fitting.
•
Disconnect the electrical plugs between the
tank components and the back of the electrical
panel (includes: power plug, low water switch
plug, tank temperature sensor plug and thermal
trip plug).
DISCONNECT BY PULLING ON
PLUG HOUSING. DO NOT DISCONNECT
BY PULLING ON CORD OR WIRES.
•
Disconnect the drain union on the back left
corner of the frame.
•
Disconnect the steam supply hose from the
top of the tank.
•
Lift the tank foot above the frame flange and
slide the tank assembly forward to remove.
2.
Loosen the four cover bolts and remove the cover
assembly from the tank.
3.
Inspect the tank interior for debris or pitting.
4.
Inspect the valve inlet for debris.
5.
Check the operation of the float valve and the
condition of the float seat.
6.
Check the low water switch for free operation.
7.
Secure the chamber cover making sure the cover
gasket is seated and the chamber is sealed.
8.
Reinstall the evaporating chamber:
•
Reconnect the fill line.
•
Reconnect electrical plugs.
•
Reconnect drain union.
•
Reconnect the vapor hose.
9.
Close the drain valve.
10. Turn on the water supply.
11. Turn on the electrical power.
VAPORMIST DI off-season shut-down procedure
1.
Switch off electric power.
2.
Remove enclosure.
3.
Shut off water supply to makeup valve.
4.
Drain evaporating chamber by opening the drain
valve. For units with end-of-season drain, please refer
to the VAPOR-LOGIC
®
3
manual.
5.
Replace enclosure.
6.
Leave chamber dry, power off and the water shut-off
valve closed until the next humidification season.
VMOM-0600.PDF 12
11/19/2009 9:59:11 AM