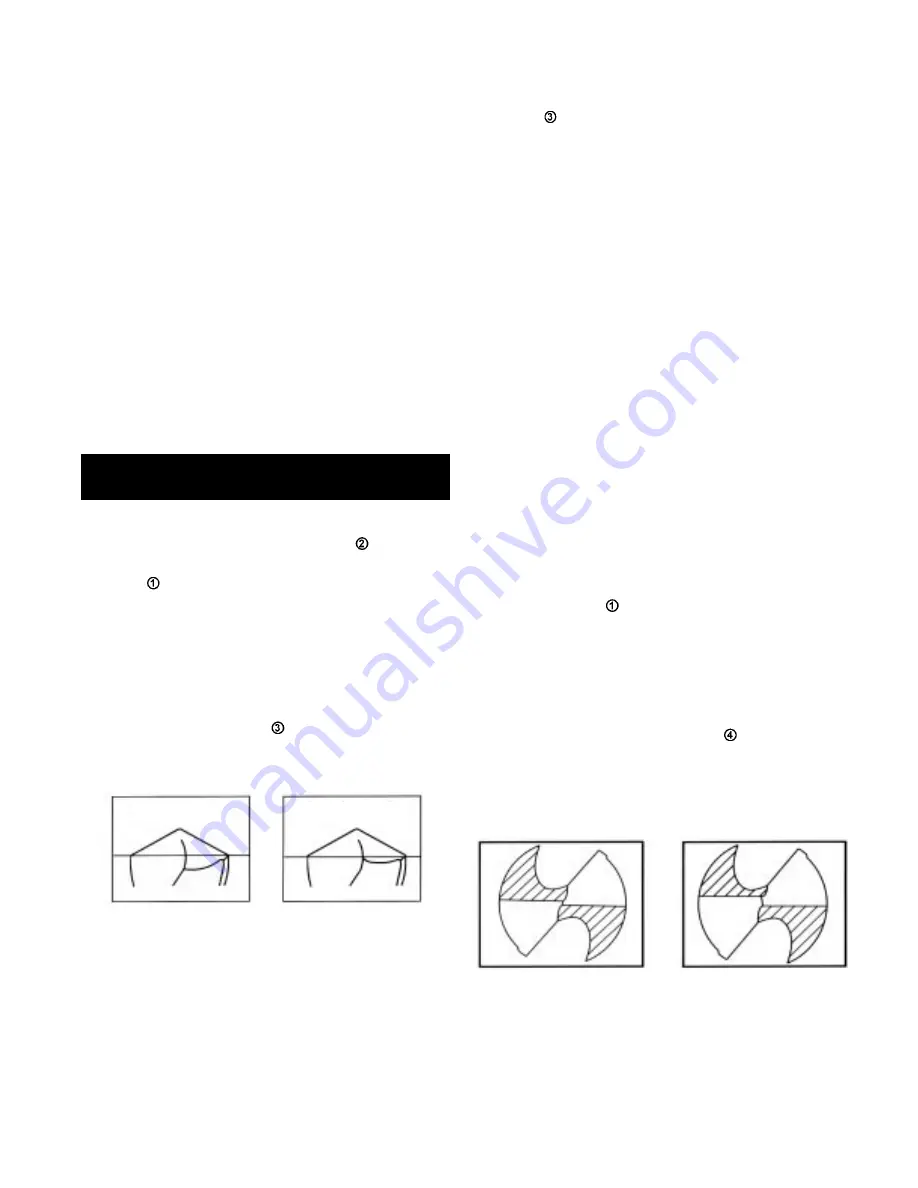
TROUBLESHOOTING & TIPS
1. I aligned the drill bit and sharpened it, but no material gets
removed. You may have allowed the paddle
to knock the
drill back into the chuck. Carefully realign the drill in the align-
ment tube
again. Make sure the drill is pushed all the way
against the drill stop (see Figure 8 on page 4).
2. I’m getting negative relief. Negative relief is present when the
heel of the flute is higher than the cutting lip on a drill. When this
happens the drill will not cut. To correct negative relief, set the
alignment tube to the non-split setting. Turning lever number 1
counter clockwise will increase relief. Realign the drill and
resharpen in the sharpening tube
. Maintain consistent inward
pressure to the grinding wheel during the chuck rotation.
3. Why is the drill point off center? If the tip of the drill bit
appears to be sharpened off center, check the following items:
a. Make sure that there are no particles between the chuck jaws
and the drill bit, which could hold it off center. b. Note if the clos-
ing knob is closed firmly enough to hold the drill bit on center.
c. During the sharpening process be sure not to push unevenly dur-
ing the rotations. If the point split appears off center see #10.
4. Why don’t my drills align like the “correct” diagram? There
may be a burr on the drill shank (remove burrs with a flat file).
Also, the drill may be too loose or too tight in chuck.
TROUBLESHOOTING
5. What can I do about the flat spot between the lip and the
heel? The flat spots or chattering on a sharpened drill, are the
result of an incomplete or fast rotation of the chuck in the sharp-
ening tube
. To correct, apply firm, not excessive inward pres-
sure and rotate the chuck smoothly while sharpening. Be sure to
complete the grind.
6. The chisel edge on my drill bit is flat. During the alignment
process the pawls were gripping “ON” the flutes of the drill bit.
Re-align the drill bit making sure that the pawls are located in the
narrowest section of the flutes.
7. After sharpening, the grind finish on my drill is rough.
Grind finish is initially rough when sharpened by a new diamond
wheel. Drill performance will not be noticeably affected howev-
er. The finish will improve as the diamond coating breaks down.
8. My small drills are grinding off center. After aligning the
small drill, look into the back of the chuck and notice if the jaws
are straight to each other. If the jaws are twisted in a spiral direc-
tion, grasp the closing knob and very carefully turn it counter
clockwise to straighten the jaws. This procedure will center the
drill in the chuck.
9. My drill point was sharpened improperly. The most com-
mon cause of improper sharpening is not aligning the drill in the
chuck properly. Key causes are: 1. Drill point not pushed all the
way to the drill stop. 2. Chuck not pushed all the way into the
alignment tube. 3. Drill not aligned in the pawls correctly.
In order to correct these problems be sure the chuck is all the way
in the alignment tube
with the flats entirely hidden. The drill
point is against the drill stop and the pawls are located in the nar-
rowest section of the drill flutes.
10. Why is my point split uneven? Figure 31 shows a drill point
that is under split and a drill point that is correctly split. To cor-
rect an uneven point split take more material off of the under split
flute. To do this, reinsert the chuck in the
splitting tube with
the under split flute on top. Repeat Step 2B (page 6) until split is
correct. A correct split point should look symmetrical. The two
parallel lines formed by the split should have a separation of .005
to .012 of an inch on the chisel angle.
Correct
Incorrect
If this guide and the video do not answer your questions call
Professional Tool Manufacturing LLC customer service at
1-800-597-6170 or 1-541-552-1301.
Watch Professional Tool Manufacturing LLC
for new innovative products.
http://www.drilldr.com
Fig. 30
Reverse the grinding wheel before you replace it.
The grinding wheel supplied with the Drill Doctor® is
designed to give you long and trouble-free service, on
average over 200 sharpenings. Eventually, you will
need to replace the wheel. However, before you replace
the wheel you can flip it over. Drill point burning and
an increase in drill bit sharpening time are indicators
that the wheel needs replacement. See page 7
You can take less material off of a drill bit. The
sharpener will remove approximately .015” to .025”
depending upon the point angle that is sharpened. To
align the drill bit to remove less material, merely insert
a shim or feeler gauge between the drill bit point and
the metal stop where the drill bit normally touches dur-
ing alignment.
10
Negative Relief
Correct Relief
Fig. 31