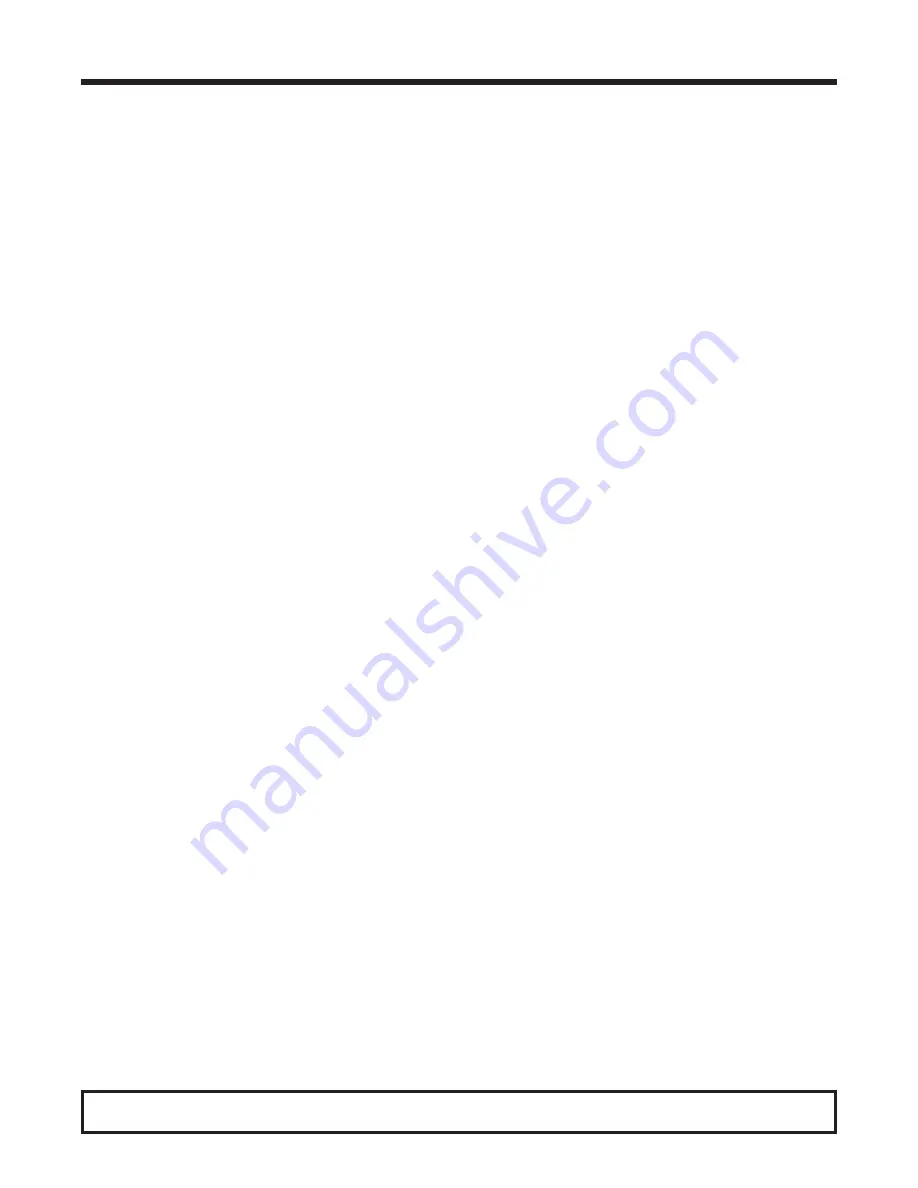
17
For your nearest Roots office contact information, please consult the last page of this document.
Coating
The coating is basically a fine-grained natural graphite*. It is
applied as several coats. Coating applied after the
machine’s internal clearances and impeller timing are estab-
lished. The effect of coating is to close up internal clear-
ances, decreasing slip and increasing flow and efficiency at
any given speed. Exhaust air may carry some coating parti-
cles.
Characteristics of Machines with Coated Internal
Service
Machines with internal abradable coating are for use with
clean, dry air only.
After coating, it is not practical to try to measure clearances
involving these surfaces before or after running the machine.
After coating and before running, some coated surfaces may
even be touching. After running, the coated surfaces may
have abraded areas and scratches, due to run-in contact
between the surfaces.
Do not attempt to measure clearances involving coated sur-
faces as a basis for setting impellers in relation to the cylin-
der bore, headplates, or each other (fronts and backs).
Clearance settings can be made accurately only with uncoat-
ed parts.
Cleaning and Preservation
Where internal, inspection indicates a need for cleaning coat-
ed surfaces of dirt, dust, etc., wipe clean only with a clean,
dry rag. Do not use a solvent or cleaner of any kind or allow
a solvent or cleaner to reach these surfaces while cleaning
uncoated surfaces.
If internal protection from rust or corrosion is required due,
for example, to removal of the machine from service, or if
the internal protections furnished as shipped by the factory
has been removed, do not use a liquid preservative of any
kind on these coated surfaces. Bags of vapor inhibitor pow-
der, such as Shell Oil Company VPI No. 250 may be used
internally, with
all
machine openings sealed with vapor barri-
er paper or tape.
Trouble Shooting Check List
This list in standard instructions applies, except note that in
those lists and in various locations throughout the standard
instruction manuals for uncoated machines, rubbing, knock-
ing, contact and wear between internal surfaces are men-
tioned as trouble indicators. This is with respect to metal-to-
metal interference. Coated surfaces can have very close
clearances and will wear in, or abrade, between surfaces,
showing rub or scratch marks which are normal conditions.
These can usually be differentiated from metal-to-metal con-
tact.
Cleaning, Coating & Curing Procedures for
Applying Abradable Coating
General.
These procedures are for coating new uncoated
repair parts, spot repair of coating, or renewal. If setting
clearances and timing are involved, this should be done
before the new parts are coated. Subsequent cleaning and
coating may involve at least partial disassembly for proper
cleaning without damaging the coating of other original parts
still coated, and to apply coating properly.
Normally, for new uncoated surfaces, three coats are applied
and each coat must be properly cured.
Cleaning Before Coating
For new uncoated surfaces, apply the cleaner with a clean,
“soaked” rag. Apply the cleaner liberally, allow to set for one
to two minutes, then wipe off. Repeat if necessary. Avoid
cleaning surfaces which will not be coated.
Wiping off with a clean, dry rag is the only cleaning allowable
for spot repair or renewal of existing coating except in the
case of a small area of grease or similar substance where
scraping clean before reaching bare metal may be attempted.
If too dirty to clean by these methods, disassembly will be
required to remove the coating entirely, solvent clean, and
recoat.
Preparation of Coating Material
The graphite suspended in the material settles out in a fairly
short time and the can must be shaken well, and also fre-
quently, during spray application. Generally, the initial shak-
ing should continue until the ball in the can rattles freely and
should then continue for at least five minutes more.
Coating General
Procedures for application are for one coat, but when multi-
ple coats are to be applied, EACH coat must be completely
cured per CURE procedure described following, before apply-
ing the next coat.
Coating Application
See notes on can concerning ventilation and inflammability.
Each layer of coating should be applied as evenly as possi-
ble. Note directions on the curing of each coating layer
applied before applying subsequent coats.
The best distance of spray can nozzle to surface being coated
is 8” to 12”. Try to maintain this distance wherever space
conditions allow it.
Coating Cure
This procedure is for
EACH
coat. When multiple coats are to
be applied, this curing procedure must be used on
EACH
coat before the next coat is applied. Keep coated parts clean
during curing.
Note that coated parts may feel dry or “tack free” after a few
minutes, but the coat will not have the
CURE
that is required.
Curing Procedures
Alternate #1
Let set for 1-1/2 hours, minimum, at normal room tempera-
ture (not less than 70°F).
DVJ & DPJ Blowers are Supplied with Internal Abradable Graphite-Based Coating
*Abradable coating applied to impellers is Slip Plate #3 as manufactured by Superior Graphite Co. For a material safety
data sheet, go to www.slipplate.com. Study material safety data sheet before working with Slip Plate #3.