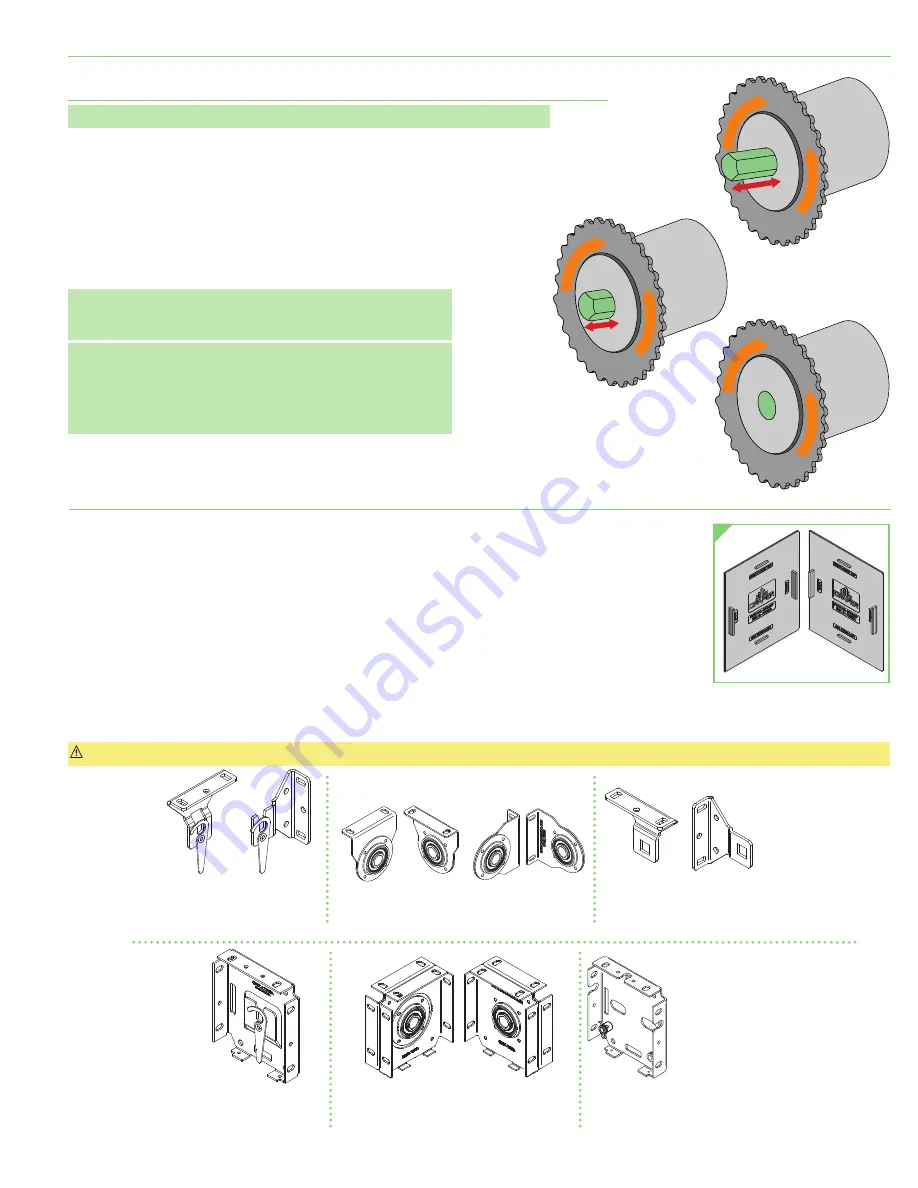
Motor End
Endcap
Idler End
Endcap
Coupler Bracket
Assembly-Fascia/Headbox
Motor End Bracket
Ceiling
Wall
Idler End Bracket
Ceiling
Wall
Coupler Bracket Assembly
Ceiling
Wall
Figure 1
Figure 2
R
E
T
R
A
C
T
E
X
T
E
ND
R
E
T
R
A
C
T
E
X
T
E
ND
R
E
T
R
A
C
T
E
X
T
E
ND
Figure 3
Section 1 -
Operating the Retractable Coupler Shaft
Please Note:
Custom products/installations may not be reflected by this document.
Draper
®
Coupled FlexShades utilize a locking retractable shaft
(Fig. 1)
to hold roller assemblies in
place and link panels together. The retractable coupler shaft on has three distinct positions: fully
extended, intermediate, and fully retracted.
1.
To retract the coupler shaft from fully extended to the intermediate position, grasp the
roller with one hand while rotating the metal ring counterclockwise
(as viewed facing the
coupler assembly)
approximately ½ of a turn with the other; this will leave the shaft extended
approximately ½".
2.
To retract the coupler shaft fully, rotate the metal ring counterclockwise
(as viewed facing the
coupler assembly)
an additional
1/3
"of a turn.
3.
To lock shaft in place when extended, rotate metal ring clockwise ¼ turn.
Please Note:
There is no retractable shaft in the idler end assembly on the
idler end shade
(furthest from the operator)
. This idler assembly utilizes a
sliding pin and retainer clip.
Please Note:
These instruction steps are for installing endcaps/brackets
one at a time. Brackets/endcaps may also all be installed at the same time,
prior to installing roller/fabric assemblies. If brackets/endcaps are installed
first, please be certain of measurements and locations. For best results,
assemble the unit on a flat, clean surface and verify measurements before
attaching brackets/endcaps.
Section 2 -
Operator End Bracket/Endcap Assembly
1.
Before mounting shades, verify measurements on the card provided with the shade, and ensure the brackets are installed
at the correct width.
2.
Measure and mark wall, jamb or ceiling for placement of mounting brackets or endcaps. Mark a level line across all
windows to ensure a level installation. Mark the outer edges of the operator- and idler-end brackets or endcaps, and the
center locations of the coupler brackets. Locations are determined by:
A
Operator-end panel width;
B
Intermediate panel width
(s)
; and
C
Idler-end panel width.
3. ENDCAP, FASCIA OR HEADBOX UNITS:
Install the endcap covers onto both the operator- and idler-end endcaps. Please
note the correct orientation of the covers as indicated on the inside face
(Fig. 2)
.
4. HEADBOX UNITS:
Follow Step 2 above, marking and drilling holes in headbox for hardware, then install the headbox.
Installer is responsible for selecting mounting hardware appropriate for site conditions.
5.
Mount the operator-end bracket/endcap assembly
(Fig. 3 for bracket and endcap types)
. Make sure the outside edge is aligned with the marked location.
Installer is
responsible for selecting mounting hardware appropriate for site conditions.
Caution:
DO NOT use wall brackets for ceiling installations, and DO NOT use ceiling brackets for wall installations.
page 3 of 10
Motorized FlexShade
®
(Coupled)