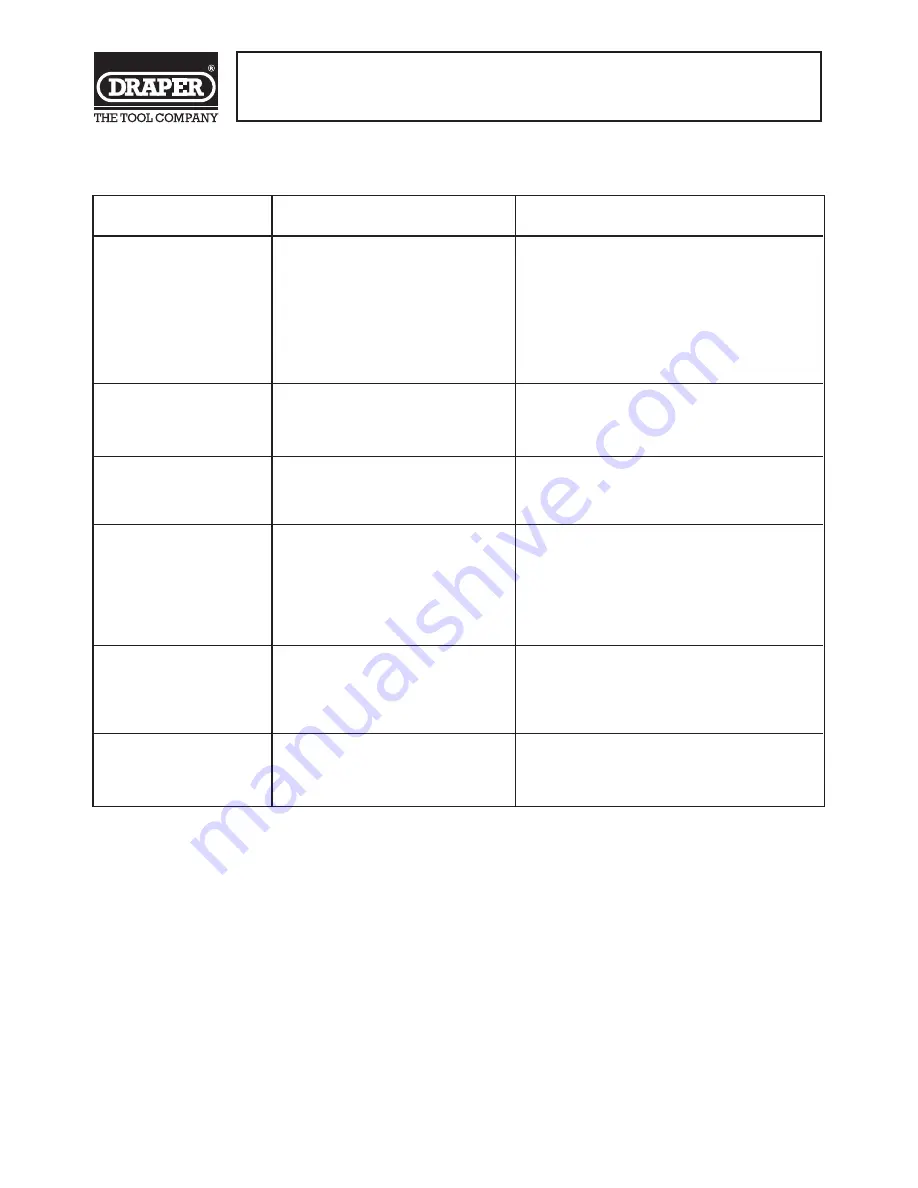
TROUBLESHOOTING
WARNING:
Please read the following instructions carefully, failure to do so could lead to serious personal injury. Read all these instructions
before operating this product and save these instructions.
IMPORTANT:
Draper Tools Limited recommends that this machine should not be modified or used for any application other than that for which it
was designed. If you are unsure of its relative applications do not hesitate to contact us in writing and we will advise you.
IMPORTANT NOTE:
Residual Risk. Although the safety instructions and operating manuals for our tools contain extensive instructions on safe working
with power tools, every power tool involves a certain residual risk which can not be completely excluded by safety mechanisms.
Power tools must therefore always be operated with caution!
1. KNOW YOUR COMPRESSOR
Before operating this compressor, read and fully
understand the starting, operating and stopping
sections in this manual. Read all labels affixed to
the compressor. Learn its applications and
limitations.
2. SERVICING AND MAINTENANCE
Do not service or maintain this compressor until
you have read and understood the maintenance
section of this manual.
3. CHECK DAMAGED PARTS
Before further use of this compressor, a guard or
any other part that is damaged should be
carefully checked to ensure that it will operate
correctly and perform its intended function.
Check for alignment of moving parts, breakage
of parts and any other conditions that may effect
its operation. A guard or other part that is
damaged should be properly repaired or
replaced.
4. DISCONNECT FROM POWER SUPPLY
Before servicing, maintaining or replacing
damaged parts ALWAYS disconnect the
compressor from the power supply.
5. EARTH
This compressor is equipped with an approved
3-core power cable. The green and yellow
conductor in the core is the earth wire. NEVER
connect the yellow and green wire to a live
terminal.
6. AVOID DANGEROUS ENVIRONMENTS
Do not use the compressor in damp or wet
locations or expose it to rain. Keep the work area
well lit. Provide adequate surrounding work
space.
*Not suitable for building sites.
7. KEEP GUARDS IN PLACE
8. AVOID ACCIDENTAL STARTING
Make sure the power supply switch is off before
connecting to the power supply.
9. KEEP CHILDREN AWAY AND MAKE
WORKSHOP CHILDPROOF
All visitors should be kept a safe distance from
the work area. The power tools and workshop
should be made childproof with padlocks,
master switches or by removing starter keys.
10. NEVER LEAVE THE COMPRESSOR
RUNNING UNATTENDED
Turn the power supply off. Do not leave the
compressor until it comes to a complete stop.
11. DO NOT OVERLOAD THE COMPRESSOR
Before operating any air tool, check that the free
air delivery (FAD) from the air compressor is
equal or greater than that of the air tool to be
used. NOTE: The compressor should not start
more than nine times in one hour.
12. AIR PRESSURE
Always check the air supply pressure is equal to
or less than the air tool manufacturers maximum
operating pressure.
13. USE SAFETY GOGGLES/MASK
Wear safety goggles (which comply to a
recognised standard) at all times. Normal
spectacles only have impact resistant lenses.
They are NOT safety glasses. Also use a face
mask if a cutting operation is dusty or if
spraying paint or other toxic substances.
14. USE RECOMMENDED ACCESSORIES
For a complete range of recommended
accessories please refer to your local Draper
stockist.
- 11 -
- 4 -
GENERAL SAFETY INSTRUCTIONS
FOR COMPRESSORS
USE ONLY ORIGINAL SPARE PARTS, AVAILABLE AT ALL AUTHORIZED SERVICE CENTRES.
FAULT
POSSIBLE CAUSE
REMEDY
Pressure drop in tank
Air leaks at connections
Allow the compressor to reach max.
pressure allowed. Switch it of and brush
a soapy water solution onto all air
connections. Look carefully for air bubbles
flowing out. Tighten those connections
where leaks are present.
If the problem is still present, contact the
After Sales Service.
The pressure switch
valve leaks when the
compressor is idle
Non-return valve seal defective
Contact your Local Service Centre
The compressor
stopped and does not
start
Overload cut-out tripped
See Page 8
The compressor does
not stop even though
the max. pressure
allowed has been
reached; the safety
valve operates
Incorrect Setting
Contact your Local Service Centre
The compressor does
not get to the set
pressure and
overheats
Compressor head gasket broken
or valve faulty
Contact your Local Service Centre
The compressor is
noisy with metallic
clangs
Bearing or connecting rod
seizure
Contact your Local Service Centre