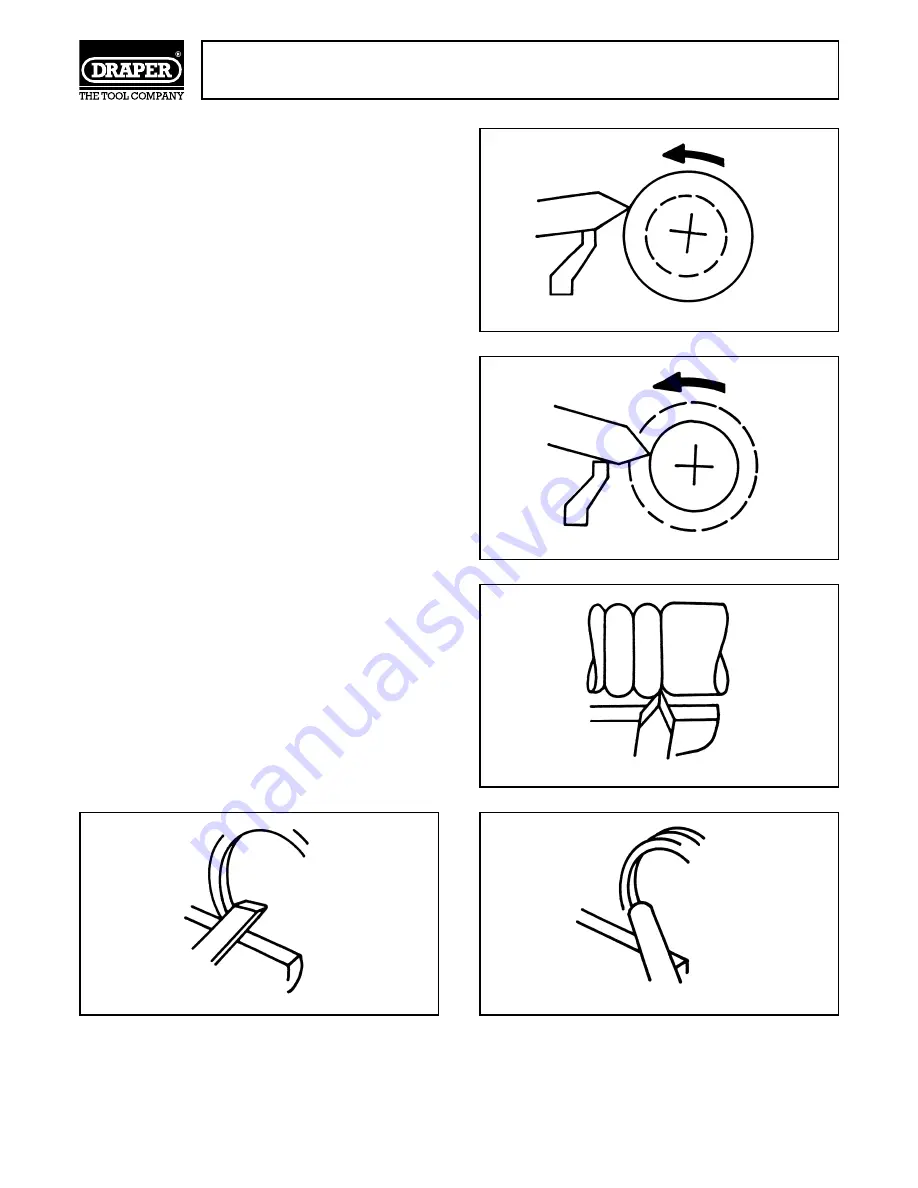
WOODTURNING OPERATIONS cont’d
USING A PARTING CHISEL
A parting chisel has one primary purpose – to cut
straight into the workpiece as deep as desired, or all
the way through the workpiece to make a cut off. This
is a very narrow chisel approximately
1
⁄
8
″
wide and is
shaped to cut its own clearance, so the cutting edge
will not burn. But when used as a scraper, it should
be backed off at regular intervals to prevent
overheating. See Figs. 53 and 54.
USING SCRAPING CHISELS
Finally, three more types of chisel should complete
the list of chisels for the average craftsman, these
and
1
⁄
2
″
spear point,
1
⁄
2
″
round nose and a 1
″
flat node.
Each of these chisels may be purchased in various
sizes, (refer to the Draper Catalogue) for special
jobs. All of these are very useful for diameter
scraping (see Figs. 55, 56 and 57) operations and for
circumference scraping, when cutting methods
cannot be employed.
The spear point chisel is used for fine scraping and
delicate operations such as the forming of beads,
parallel grooves and shallow vees. Edges and bowl
contours can be rounded with the round nose chisel.
Any flat surface can be scraped with the flat nose
chisel.
- 21-
Fig.53.
Fig.54.
Fig.55.
Fig.57.
Fig.56.
CUTTING
SCRAPING
SPEAR POINT
FLAT NOSE
ROUND NOSE