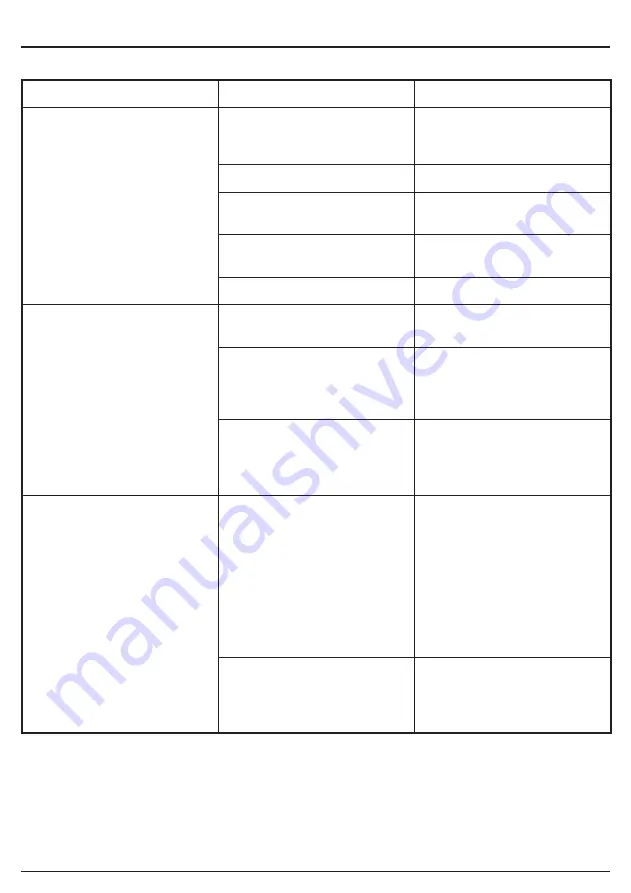
10. MAINTENANCE AND TROUBLESHOOTING
– 15 –
10.1 TROUBLESHOOTING GUIDE
Problem
Possible Cause
Remedy
Compressor will not run.
1. No electrical power.
1. Plugged in? Check fuse/
breaker or motor
overload.
2. Blown fuse.
2. Replace blown fuse.
3. Breaker open.
3. Reset, determine cause of
problem.
4. Thermal overload open.
4. Motor will restart when
cool.
5. Pressure switch bad.
5. Replace.
Motor operating, but cannot
run or runs slowly.
1. Defective check valve or
unloaded.
1. Replace or repair.
2. Poor contacts, line voltage
low.
2. Check connections,
eliminate extension cork if
used, check circuit with
voltmeter.
3. Shortened or open motor
winding.
3. Replace motor.
Danger! Do not
disassemble check valve
with air in tank – bleed tank.
1. Incorrect size fuse, circuit
overloaded.
1. Check for proper fuse,
use time-delay fuse.
Disconnect other electrical
appliances from circuit or
operate compressor on its
own branch circuit.
Disconnect other electrical
appliances from circuit or
operate compressor on its
own branch circuit.
Fuses blow/circuit breaker
trips repeatedly.
Caution! Never use an
extension cord with this
product.
2. Defective check valve or
unloaded.
2. Replace or repair.
Danger! Do not
disassemble check valve
with air in tank – bleed tank.