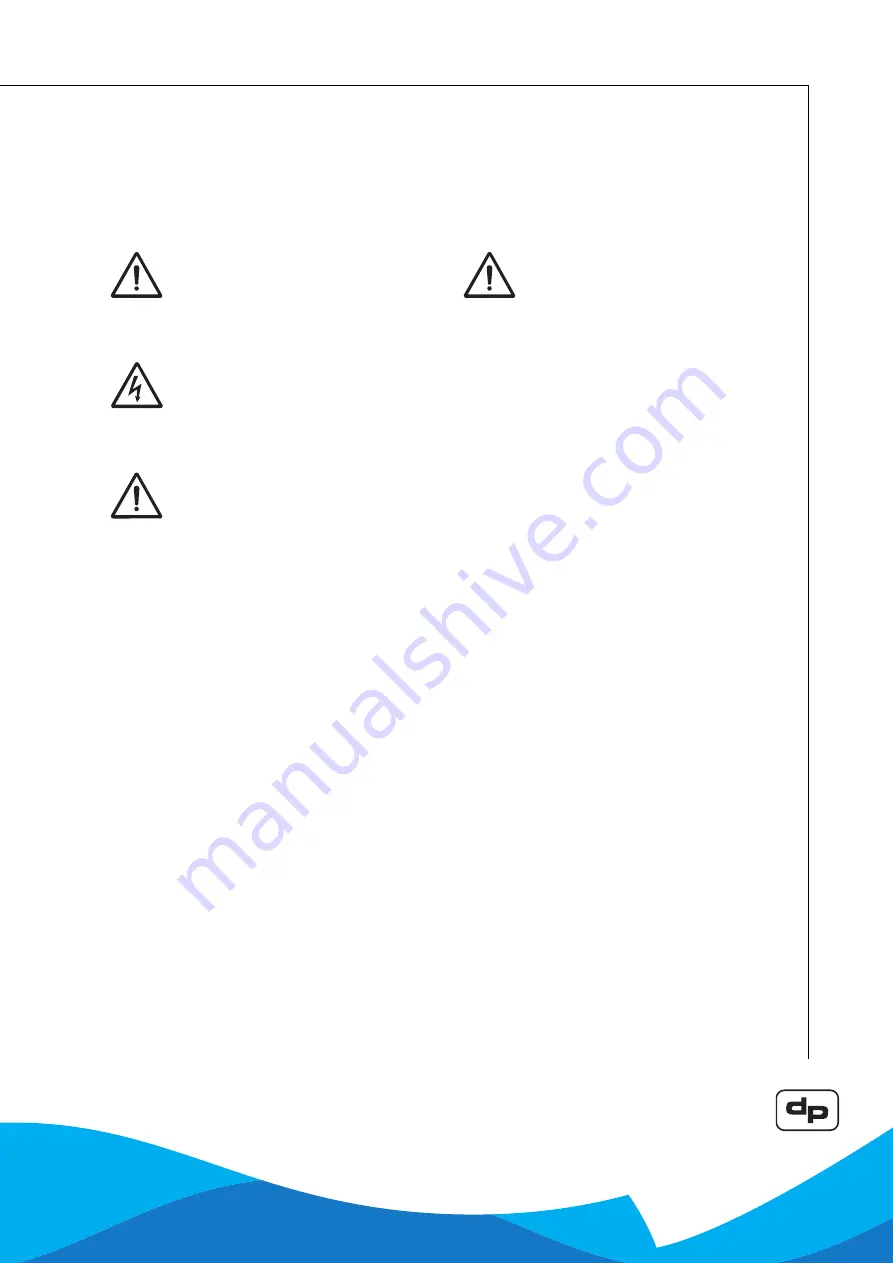
11
5
Installation
5.1
Mechanical installation
WARNING
Remove all cables and hoisting chains
from the pump sump. Prevent thus that
they can be sucked and damaged by
the pump.
WARNING
Never allow the pump to drop from the
feeder cable or delivery pipe. Use a
chain or a sufficiently strong cable that
is attached to the grip of the pump.
WARNING
Do not use the pump in locations where
there is freezing danger.
•
Take the pump out of the packaging and check
for any transportation damage.
•
Check whether the delivery is complete based
on the included Production Order Combination
List. Contact DP-Pumps if the delivery is
damaged and/or incomplete.
•
Position and assemble the pump system on a
suitable surface or suspend the pump using the
grip.
•
Position the pump on a paved surface when
there is mud and sand.
•
Check whether the pump impeller can turn
freely.
•
Make sure that the distance between the bottom
and the supply (A) is at least the same as the
free passage, see the technical information.
•
Assemble, if required, a non-return valve in the
delivery pipe to prevent liquid flowing back. The
swing check valve must be installed at least 2 m
from the pump for the “A" version pump.
•
Assemble (if possible) a globe valve on the
delivery side.
•
Install the highest point of the delivery pipe
above the drain pipes of the street (ground level)
to make sure that a drain return flow is not
possible.
5.2
Electrical installation
WARNING
Only authorised personnel are allowed
to make electrical connections to the
motor in accordance with local
regulations.
Electrical connections:
•
Make sure that the motor specifications
correspond with the power supply to which the
pump motor is connected. Consult "Electrical
diagrams" in the annexes for the correct
connection diagram.
•
Connect the motor using a motor safety switch.
The setting must be the same as the motor
amperage as listed on the identification label in
relation to a direct start (DOL; Direct On Line).
•
Connect the pump in accordance with the
electrical diagram that can be found in the
junction box.
•
When the pump is being connected through a
frequency transformer, the motor must be
provided with a suitable “shielded” cable
specially for this situation. The temperature
protection in the pump must also be connected
to the frequency transformer. Range 30-50 Hz