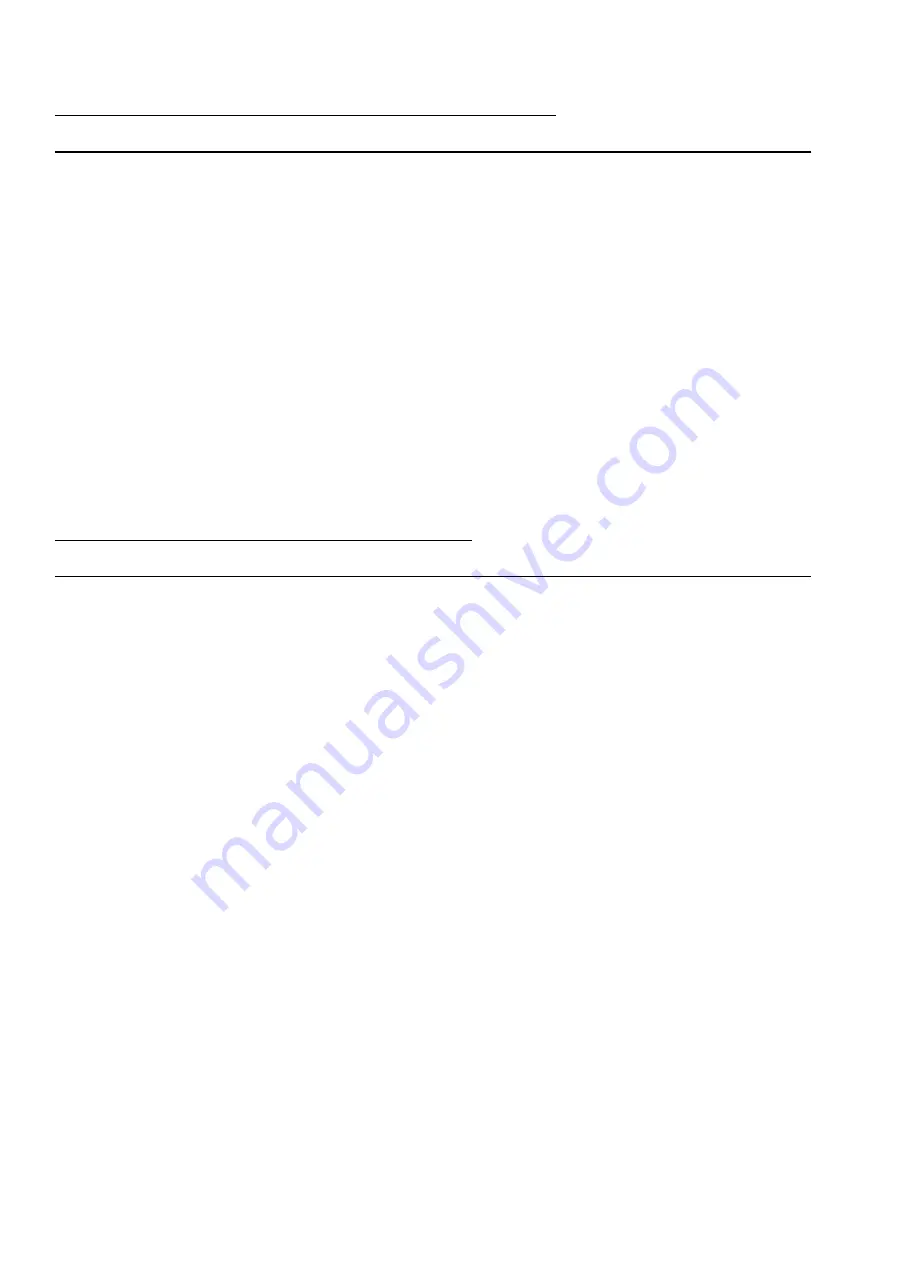
16
WILDEN PUMP & ENGINEERING, LLC
WIL-10260-E-02
SECTION 7F – AIR-CONTROLLED
TROUBLESHOOTING
Pump will not run or runs slowly.
1. Check air inlet screen and air filter for debris.
2. Check for sticking air valve, flush air valve in solvent.
3. Check for worn out air valve. If piston face in air valve is
shiny instead of dull, air valve is probably worn beyond
working tolerances and must be replaced.
4. Check center block Glyd™ rings. If worn excessively, they
will not seal and air will simply flow through pump and out
air exhaust. Use only Wilden Glyd™ rings as they are of
special construction and ISO 15-5 wt oil with arctic char-
acteristics.
5. Check for rotating piston in air valve.
6. Check type of lubricant being used. A higher viscosity
oil than suggested may cause the piston to stick or run
erratically. Wilden suggests the use of a hydraulic oil with
arctic characteristics (ISO 15-5 wt).
Pump runs but little or no product flows.
1. Check for pump cavitation; slow pump speed down to
match thickness of material being pumped.
2. Check for sticking ball checks. If material being pumped
is not compatible with pump elastomers, swelling may
occur. Replace ball checks and o-rings with proper elas-
tomers.
3. Check to make sure all suction connections are air tight,
especially clamp bands around intake balls.
Pump air valve freezes.
Check for excessive moisture in compressed air. Either
install dryer or hot air generator for compressed air.
Air bubbles in pump discharge.
1. Check for ruptured diaphragm.
2. Check tightness of clamp bands, especially at intake
manifold.
Product comes out air exhaust.
1. Check for diaphragm rupture.
2. Check tightness of piston plates to shaft.
Pump rattles.
1. See E9 Troubleshooting Guide.
2. Create false discharge head or suction lift.
SECTION 7G – ACCU-FLO™
TROUBLESHOOTING
Pump will not run.
1. Check for pressurized air at the inlet. (Min. 3.1 bar [45
psig].)
2. Check air inlet and filter for debris.
3. Connect a test lamp to the two wires which run to pump
and ensure that the lamp cycles on and off.
4. Make sure that the air valve manual override (small red
knob on front of valve) is switched to the “0” position.
5. Check pilot pressure vent at the top of the operator/coil
assembly to ensure that it is not clogged.
6. Check for a worn out air valve. If air continually blows out
the exhaust in very large quantities, the air valve seals
may be worn beyond their ability to function. In this case,
the valve must be replaced.
NOTE: Before the valve is scrapped, it is possible that it may
be saved by completely disassembling the valve, cleaning all
components and relubricating the valve.
Pump runs but little or no fluid comes out.
1. Check that the discharge isolation valve is not closed.
2. Check that the electronic signal is slow enough that the
pump is able to complete each physical stroke before
it is signaled to change direction. The time required to
complete the stroke is determined by a variety of factors
which include fluid viscosity and head pressure. The shaft
can be viewed if the muffler is removed to verify that the
pump is stroking.
3. Check for pump cavitation; slow pump speed down to
match the thickness of the material being pumped.
4. Check for sticking ball check valves. If the material being
pumped is not compatible with the pump elastomers,
swelling may occur. Replace ball check valves and o-ring
with the proper elastomers.
5. Check to make sure that all suction connections are air
tight, and that the clamp bands are properly tightened.
Pump air passages blocked with ice.
Check for excessive moisture in compressed air line. As
the air expands out the exhaust during the operation of
the pump, water vapor entrapped in the compressed air
can freeze and block the air passageways in the pump.
If this occurs, it may be necessary to install a coalescing
filter, an air dryer, or a hot air generator for the compressed
air.
Air bubbles in pump discharge.
1. Check for ruptured diaphragm.
2. Check tightness of clamp bands, and the integrity of the
o-rings, especially at intake manifold.
Product comes out air exhaust.
1. Check for diaphragm rupture.
2. Check tightness of piston plates to shaft.
Pump rattles.
1. See E9 Troubleshooting Guide.
2. Create false discharge head or suction lift.
Solenoid buzzes or solenoid burnout.
1. Incorrect voltage, faulty or dirty solenoid.
Solenoid valve fails to shift electrically but shifts with
manual override.
1. Incorrect voltage, defective coil or wiring.
Solenoid valve fails to shift electrically or with manual
override.
1. Inadequate air supply, contamination, inadequate or
improper lubrication, mechanical binding in the valve.
Valve shifts but fails to return.
1. Broken spring, mechanical binding.
Excessive leaking from air valve vent.
1. Worn seals in air valve.