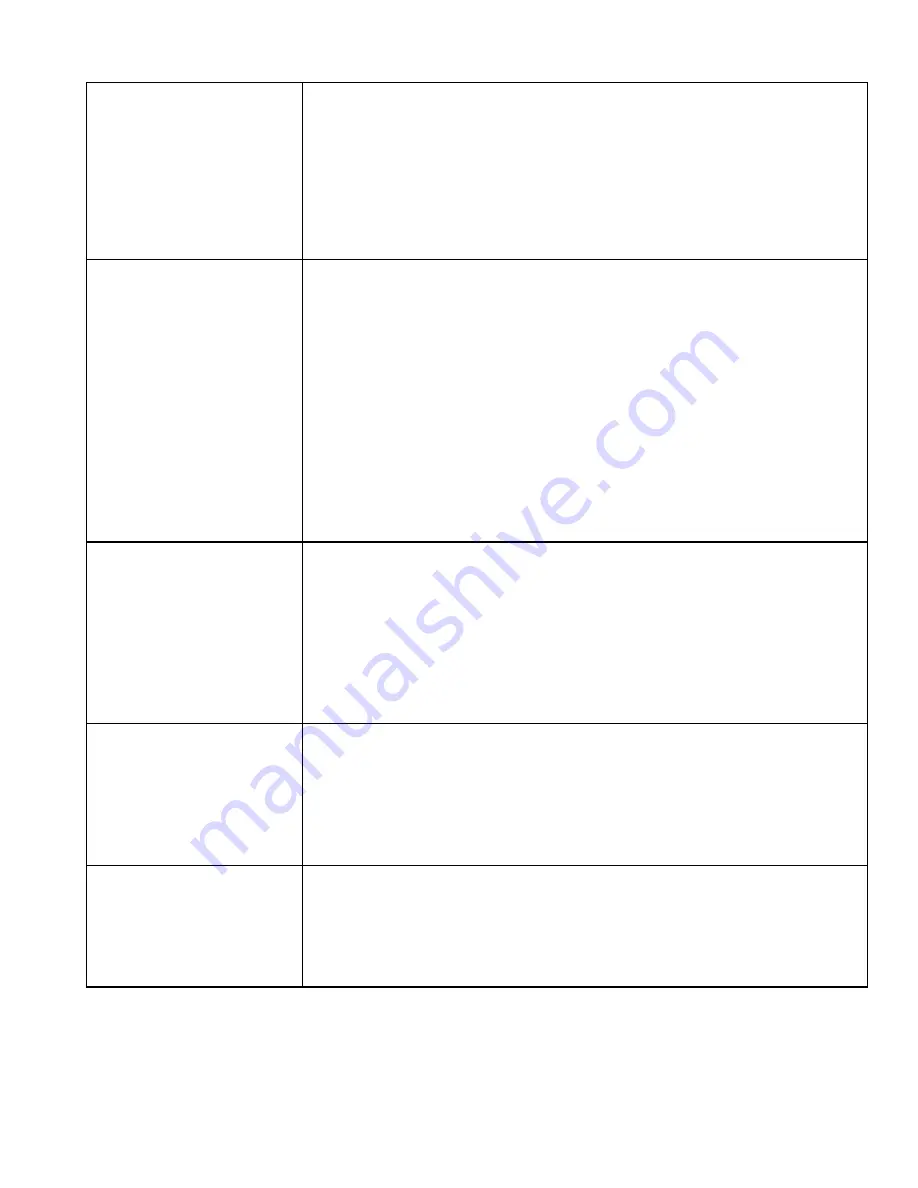
201-D00 page 11/12
TROUBLESHOOTING
continued
Reduced Capacity
1. Pump speed too low.
2. Suction valves not fully open.
3. Air leaks in the suction line.
4. Excessive restriction in the suction line (i.e.: undersized piping, too many elbows &
fittings, clogged strainer, etc.).
5. Damaged or worn parts.
6. Excessive restriction in discharge line causing partial flow through the relief valve.
7. Relief Valve worn, set too low, or not seating properly.
8. Vanes installed incorrectly (see "Vane Replacement").
Noise
1. Excessive vacuum on the pump due to:
a. Undersized or restricted fittings in the suction line.
b. Pump speed too fast for the viscosity or volatility of the liquid.
c.
Pump too far from fluid source.
2. Running the pump for extended periods with a closed discharge line.
3. Pump not securely mounted.
4. Improper drive line (see "Pump Drive").
5. Bearings worn or damaged.
6. Vibration from improperly anchored piping.
7. Bent shaft, or drive coupling misaligned.
8. Excessively worn rotor.
9. Malfunctioning valve in the system.
10. Relief valve setting too low.
11. Damaged vanes (see following category).
Damaged Vanes
1. Foreign
objects
entering the pump.
2. Running the pump dry for extended periods of time.
3. Cavitation.
4. Viscosity too high for the vanes and /or the pump speed.
5. Incompatibility
with the liquids pumped.
6. Excessive
heat.
7. Settled or solidified material in the pump at start-up.
8. Hydraulic hammer - pressure spikes.
9. Vanes installed incorrectly (see"Vane Replacement").
Broken Shaft
1. Foreign
objects
entering the pump.
2. Viscosity too high for the pump speed.
3. Relief valve not opening.
4. Hydraulic hammer - pressure spikes.
5. Pump/driver
misalignment.
6. Excessively worn vanes or vane slots.
7. Settled or solidified material in the pump at start-up.
Mechanical Seal Leakage
1. O-rings not compatible with the liquids pumped.
2. O-rings nicked, cut or twisted.
3. Shaft at seal area damaged, worn or dirty.
4. Ball bearings overgreased.
5. Excessive
cavitation.
6. Mechanical seal faces cracked, scratched, pitted or dirty.