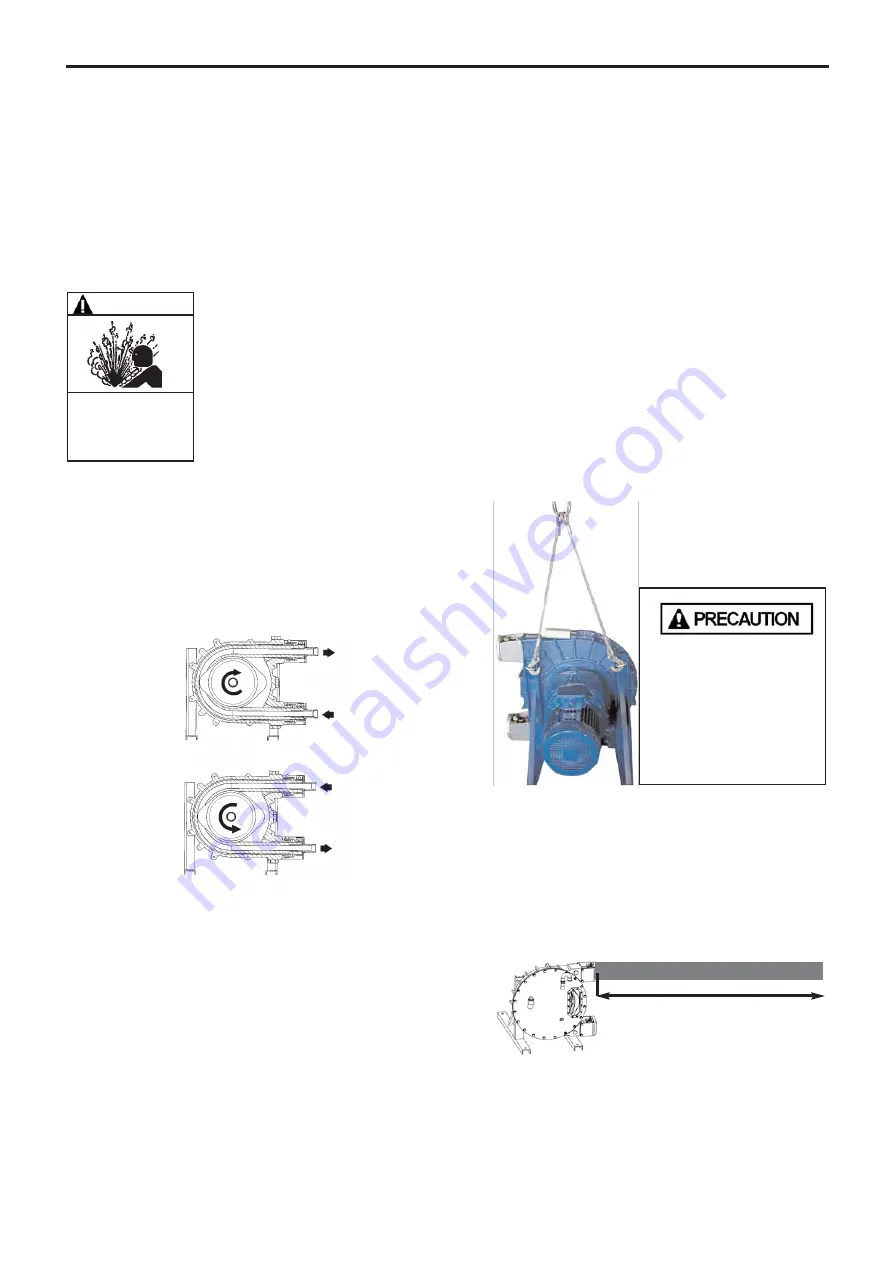
6/19
NT 1101-G00 08.10 AX40 - ASX40 e
If the liquid may freeze or solidify, prepare for draining
the piping by installing drain taps at the low points and
air vents at the high points.
In the case of a very high intake or if you wish to prevent
the piping from emptying at shutdown, you can install a
foot valve. It should have a large diameter so as not to
generate additional head loss.
2.6 Direction of rotation
The MOUVEX pump is reversible, this allows it to always
circulate the liquid in the desired direction by choosing
the corresponding direction of rotation.
The intake and discharge sides are determined as follows :
When an observer is placed on pump cover side (oppo-
site to the shaft output), if rotation takes place clockwise,
the intake is on the bottom, on the contrary if the rotation
is anticlockwise, the intake is on the top.
2.7 Liquids containing a high proportion of
particles
In the case where the pumped fluid contains particles,
use the upper flange as the inlet flange.
This facilitates discharge of the sediments formed by the
build-up of the particles contained in the fluid, so this
reduces friction between the hose and the shoes.
Therefore, the pump may be re-started more easily.
2.8 Working with vaccum on the suction side
Because of the operating principle of the pump, using it
with suction pressure lower than the atmospheric pres-
sure will cause a resulting loss of flow more or less in
line with the conditions of the application (hose material,
rotation speed, temperature, etc.).
In order for the pump to generate the normally required
flow, MOUVEX recommends using a vacuum draw kit
inside the body of the pump.
In all cases, when using a vaccum kit, suction pressure
must not be lower than -0,9 barg (-13 psig).
If a vacuum draw kit is not used on an ABAQUE pump
operating with suction pressure lower than atmospheric
pressure, MOUVEX no longer guarantees the perfor-
mance of the pump.
2.9 Handling
The maximum weight of the pump is :
• AX40 ..............................200 kg (441 lb)
• ASX40 ............................130 kg (287 lb)
2.10 Pump location
Provide sufficient clearance around the pump for main-
tenance operations.
Particularly, make sure that there is sufficient clearance
for replacing the hose; the distance between the pump
flanges and the closest obstacle must allow the hose to
be removed, as shown below :
Clockwise rotation
Anticlockwise rotation
1200 mm (47,244 in)
USE SUITABLE LIFTING
DEVICES FOR HANDLING.
USE THE LIFTING RINGS
PROVIDED.
FAILURE TO RELIEVE THE SYSTEM
PRESSURE PRIOR TO PERFORMING
ANY WORK ON THE PUMP OR THE
INSTALLATION CAN CAUSE PERSONAL
INJURY OR PROPERTY DAMAGE.
WARNING
Hazardous pressure
can cause
personal injury
or property damage.
2. INSTALLATION (continued)