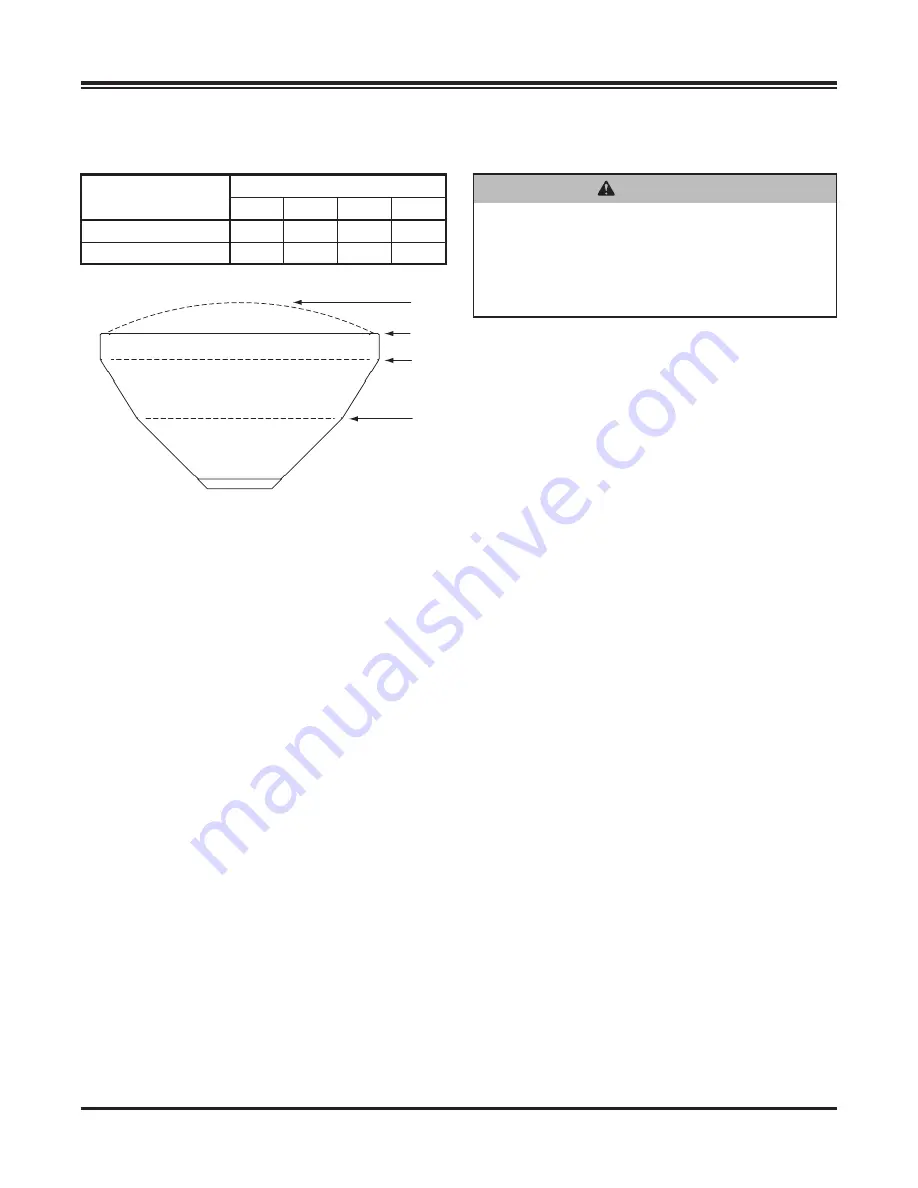
Lit. No. 74125/74126, Rev. 00
11
July 1, 2020
DETERMINING VEHICLE PAYLOAD
1. Install the hopper spreader and optional
equipment according to the Installation
Instructions.
2. Install or attach any other equipment that will be
on the vehicle while the hopper spreader will be in
use (step bumper, trailer hitch, snowplows, etc.).
Fill gas tanks.
3. Obtain the Gross Vehicle Weight Rating (GVWR),
Front Gross Axle Weight Rating (FGAWR), and
Rear Gross Axle Weight Rating (RGAWR) from
the certification label located inside the driver-side
door jamb or door.
4. With the occupants in the truck for normal hopper
spreader operation, weigh the vehicle to obtain
gross vehicle weight (GVW).
5. Subtract the GVW from the GVWR to determine
the available material payload.
6. Obtain the weight per cubic yard (lb/yd
3
) of the
desired material. Divide the weight into the
payload to determine the maximum volume of
material that can be carried.
7. Refer to the Load Volume table and diagrams to
determine the maximum fill level for the material.
8. Fill the hopper with material to the calculated level.
Reweigh the vehicle with occupants and verify that
the Loaded Gross Vehicle Weight, Front Gross
Axle Weight, and Rear Gross Axle Weight are less
than the vehicle's ratings.
9. Repeat Steps 6–8 for each type of material.
The worksheet for Determining Vehicle Payload (next
page) includes an example.
WARNING
Overloading could result in an accident or
damage. Do not exceed GVWR or GAWR
ratings as found on the driver‑side door
cornerpost of the vehicle. See Loading
section to determine maximum volumes of
spreading material.
LOADING
Hopper
Model
Load Volume (yd
3
)
A
B
C
D
0.35 yd³
0.4
0.35
0.2
0.03
0.7 yd³
0.85
0.7
0.4
0.06
LOAD VOLUME
A
B
C
D
A: Rounded Load
B: Struck Load
C: Second Bump
D: First Bump
Summary of Contents for Western Striker 98805
Page 2: ......
Page 6: ...Lit No 74125 74126 Rev 00 6 July 1 2020 0 7 yd hoppers only 0 35 yd hoppers have no cross bar...
Page 33: ...Lit No 74125 74126 Rev 00 33 July 1 2020 This page intentionally left blank...
Page 34: ...Lit No 74125 74126 Rev 00 34 July 1 2020 This page intentionally left blank...
Page 35: ...Lit No 74125 74126 Rev 00 35 July 1 2020 This page intentionally left blank...