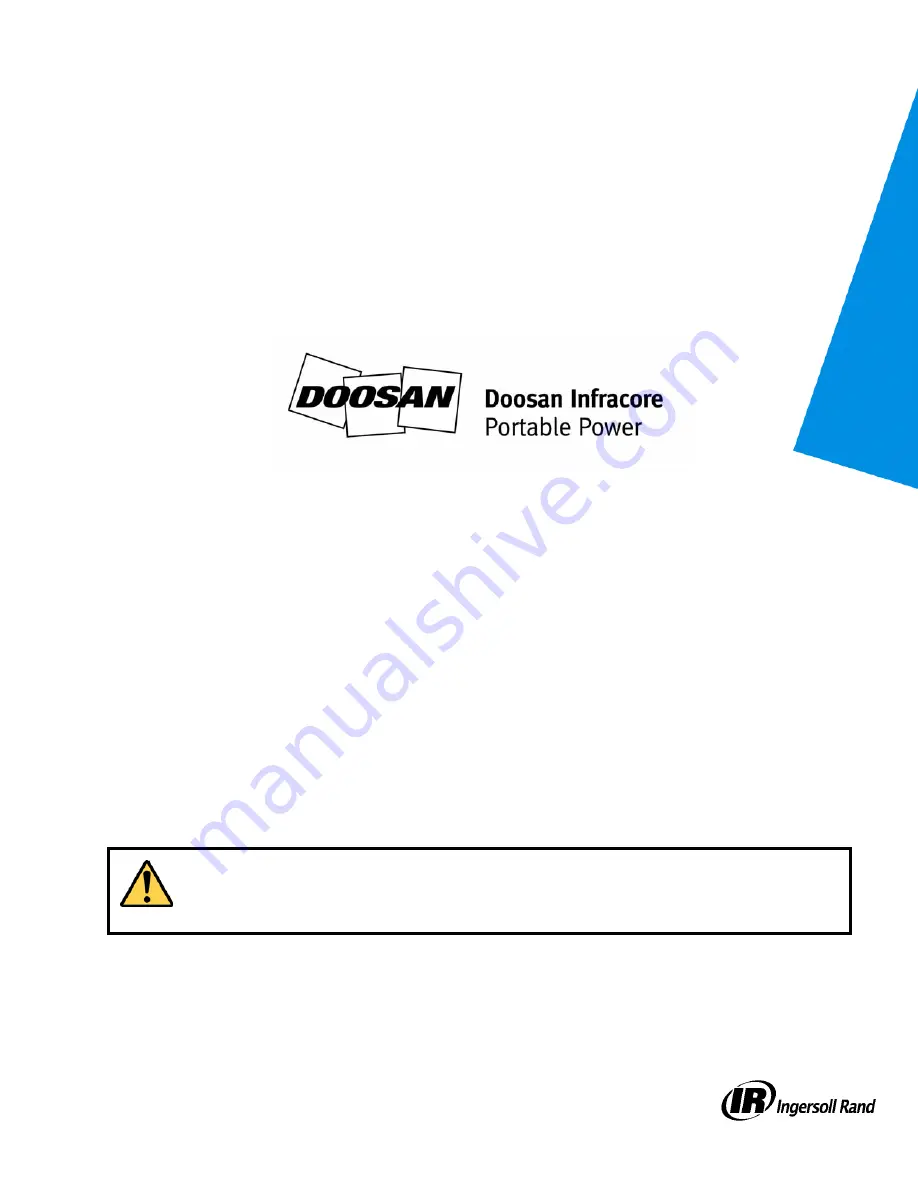
Doosan Infracore Portable Power
1293 Glenway Drive
Statesville, N.C. 28625
www.doosanportablepower.com
Book: 22610380 (4-09) Rev A
This manual contains important safety information.
Do not destroy this manual.
This manual must be available to the personnel who operate and maintain this machine.
OPERATION, MAINTENANCE
COMPRESSOR MODELS
P185WJD (E)
XP185WJD-T1 (222)
MANUAL
Summary of Contents for P185WJD
Page 2: ...2...
Page 5: ...Book 22610380 4 09 Rev A 3 Foreword...
Page 8: ...6 Book 22610380 4 09 Rev A...
Page 9: ...Book 22610380 4 09 Rev A 7 Drawbar Notice...
Page 11: ...Book 22610380 4 09 Rev A 9 Safety...
Page 14: ...Operating Maintenance Manual Safety 12 Book 22610380 4 09 Rev A...
Page 15: ...Safety Operating Maintenance Manual Book 22610380 4 09 Rev A 13...
Page 16: ...Operating Maintenance Manual Safety 14 Book 22610380 4 09 Rev A...
Page 18: ...Operating Maintenance Manual Safety 16 Book 22610380 4 09 Rev A maintenance information...
Page 20: ...Operating Maintenance Manual Safety 18 Book 22610380 4 09 Rev A...
Page 21: ...Book 22610380 4 09 Rev A 19 Section 3 Noise Emission...
Page 26: ...Operating Maintenance Manual Noise Emission 24 Book 22610380 4 09 Rev A...
Page 27: ...Book 22610380 4 09 Rev A 25 Section 4 General Data...
Page 30: ...Operating Maintenance Manual General Data 28 Book 22610380 4 09 Rev A...
Page 31: ...29 OPERATION...
Page 39: ...OPERATION Operating Maintenance Manual 37...
Page 40: ...39 Section 6 MAINTENANCE...
Page 48: ...47 Section 7 LUBRICATION...
Page 50: ...LUBRICATION Operating Maintenance Manual 49...
Page 51: ...51 Trouble Shooting...