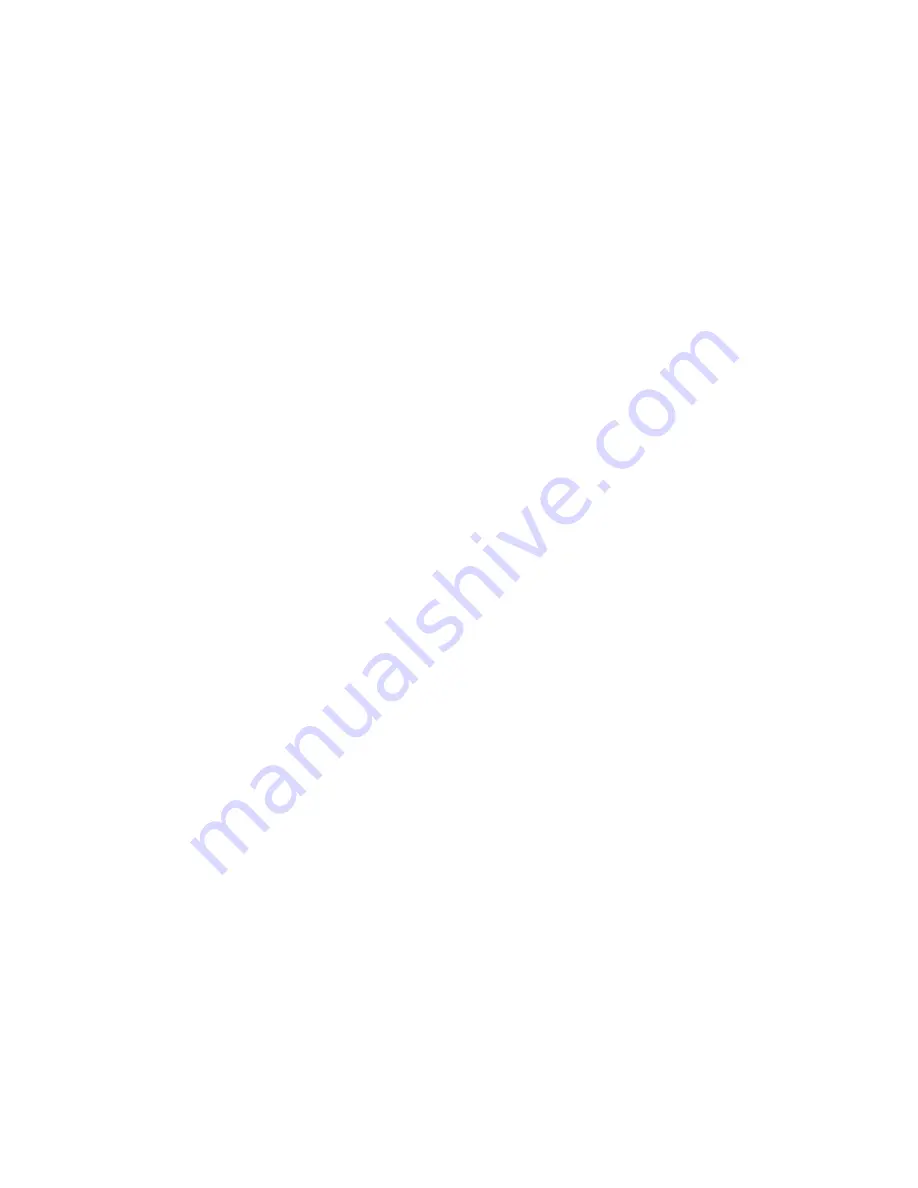
TABLE OF CONTENTS
Operation & Maintenance Manual
TITLE
PAGE
SAFETY..................................................................................................................................... 54
Instructions ................................................................................................................................ 55
General Repair ........................................................................................................................... 57
Environmental Pollution .............................................................................................................. 58
Engine Management................................................................................................................... 59
Prevention of Pollution ................................................................................................................ 60
Start and Shutdown .................................................................................................................... 61
Break-in Period of Engine............................................................................................................ 62
Inspection after Starting the Engine ............................................................................................. 63
Operation in Winter..................................................................................................................... 64
Regular Inspection...................................................................................................................... 65
Checking the Engine Oil........................................................................................................ 66
Replacement of Engine Oil .................................................................................................... 68
Coolant ................................................................................................................................ 70
Checking the Coolant...................................................................................................... 71
Replenishment of Coolant ............................................................................................... 74
Replacement of Coolant.................................................................................................. 75
Fuel System ................................................................................................................... 76
Summary of Contents for P185WDOU-T4F
Page 2: ......
Page 6: ...TABLE OF CONTENTS Operation Maintenance Manual TITLE PAGE...
Page 7: ...FOREWORD 9...
Page 10: ...12...
Page 11: ...SAFETY 13...
Page 19: ...SAFETY Operation Maintenance Manual Decals 21...
Page 20: ...Operation Maintenance Manual SAFETY 22...
Page 21: ...SAFETY Operation Maintenance Manual 23...
Page 22: ...24...
Page 23: ...NOISE EMISSION 25...
Page 30: ...32...
Page 31: ...GENERAL DATA 33...
Page 34: ...36...
Page 35: ...OPERATING INSTRUCTIONS 37...
Page 43: ...OPERATING INSTRUCTIONS Operation Maintenance Manual 45...
Page 51: ...ENGINE OPERATION 53...
Page 76: ...78...
Page 77: ...LUBRICATION 79...
Page 80: ...82...
Page 81: ...MAINTENANCE 83...
Page 90: ......
Page 91: ......
Page 92: ...94...
Page 93: ...TROUBLESHOOTING 95...
Page 102: ...104...