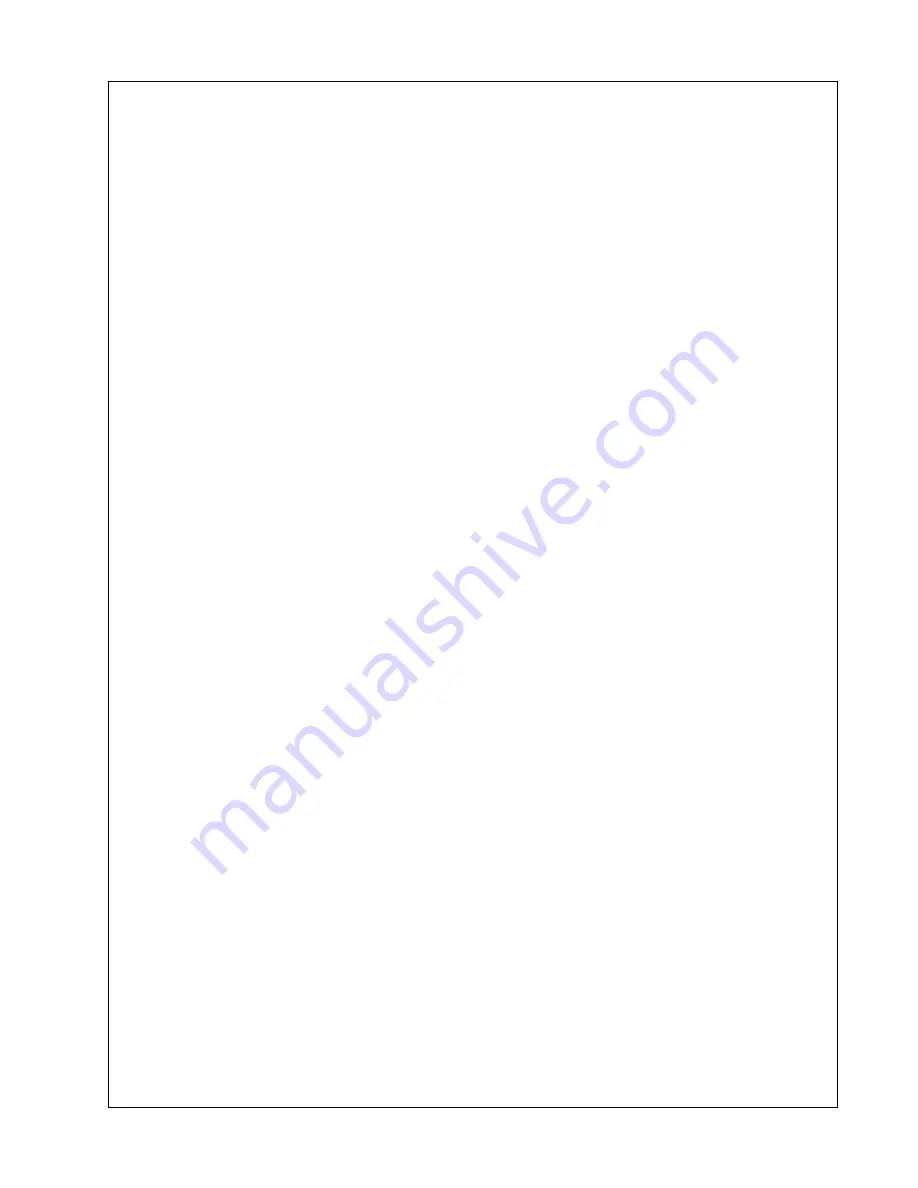
Machine Systems
Operating & Maintenance Manual
Book: 22846471 (3-09-07) Rev. B
75
A PWM (Pulse Width Modulated) throttle is used to communicate with the CAT engine. The
WEDGE controller receives diagnostic and run time data from the engine over the J1939 CAN
network. A PWM throttle interface is used with the engine. Figure 2-2 shows the connections
between the WEDGE controller and the engine controller.
It has a base frequency of 500 Hz and the duty cycle varies from 10% to 90%.
Figure 2-2 shows the signals between the engine controller and the WEDGE controller.
Sensors and Transducers
The electronics system contains sensors and transducers that are used to collect data from
the compressor. The temperature is measured by a thermistor. This device exhibits a change
in resistance as the temperature changes. The resistance causes an input voltage change to
the WEDGE controller input and is interpreted as a temperature change.
The electronics system also uses pressure transducers to measure compressor pressure
changes. These devices have an output signal of .45 VDC to 4.5 VDC, corresponding to 0 psi
and the maximum measured psi for a particular device. The maximum pressure transducer
ranges are 100, 225 and 500 psi. The 100, 225 and 500 psi devices are gauge pressure
devices. These transducers are provided with 5 VDC excitation to power the device. These
are three wire devices: excitation, signal and ground.
Digital Inputs and Outputs
The WEDGE controller scans digital inputs such as switch contacts. These are either "ON"
(24VDC) or "OFF" (0 VDC). These digital inputs are connected to switches within the package
such as the key start switch, air filter switches and IQ filter switches.
The WEDGE controller provides 24 VDC digital outputs to control solenoids, start compressor
and DC heaters. These are 24 VDC "ON" and 0 VDC "OFF". They are current limited and
short circuit protected.
Controller Outputs
The WEDGE controller has three types of outputs: frequency, pulse width modulated (PWM)
and 24 VDC digital (ON /OFF). The frequency output is used as a throttle signal for the engine.
The PWM signal is used as a throttle signal for the Caterpillar engine. It has a base frequency
of 500 Hz and the duty cycle varies from 10% to 90%.
Pressure Control
The discharge pressure is controlled by manipulating the engine speed and compressor inlet
valve position. The inlet valve position is controlled pneumatically and the engine speed is
determined by the WEDGE controller. The WEDGE measures the pneumatic system
regulation pressure and computes an engine throttle setting. This throttle setting is sent to the
engine via the frequency throttle, PWM or J1939 throttle, depending on which technique is
used. The engine controller will control engine speed to this throttle setting.
Book:46623600 (10-12-2012) Rev. A
Summary of Contents for HP900
Page 2: ...2...
Page 8: ...Book 22846471 3 09 07 Rev B 7 Foreword Book 46623600 10 07 2012 Rev A...
Page 12: ...Book 22846471 3 09 07 Rev B 11 Safety Book 46623600 10 12 2012 Rev A...
Page 20: ...Book 22846471 3 09 07 Rev B 19 Noise Emission...
Page 26: ...Book 22846471 3 09 07 Rev B 25 General Information Book 46623600 10 12 2012 Rev A...
Page 32: ...Book 22846471 3 09 07 Rev B 31 Operating Instructions Book 46623600 10 12 2012 Rev A...
Page 50: ...Book 22846471 3 09 07 Rev B 49 Maintenance Book 46623600 10 12 2012 Rev A...
Page 71: ...70 Always use Ingersoll Rand Replacement parts Always Use DOOSAN Replacement Parts...
Page 72: ...Book 22846471 3 09 07 Rev B 71 Machine Systems Book 46623600 10 12 2012 Rev A...
Page 78: ...Book 22846471 3 09 07 Rev B 77 Fault Finding Book 46623600 10 12 2012 Rev A...
Page 84: ...Book 22846471 3 09 07 Rev B 83 Options Book 46623600 10 12 2012 Rev A...