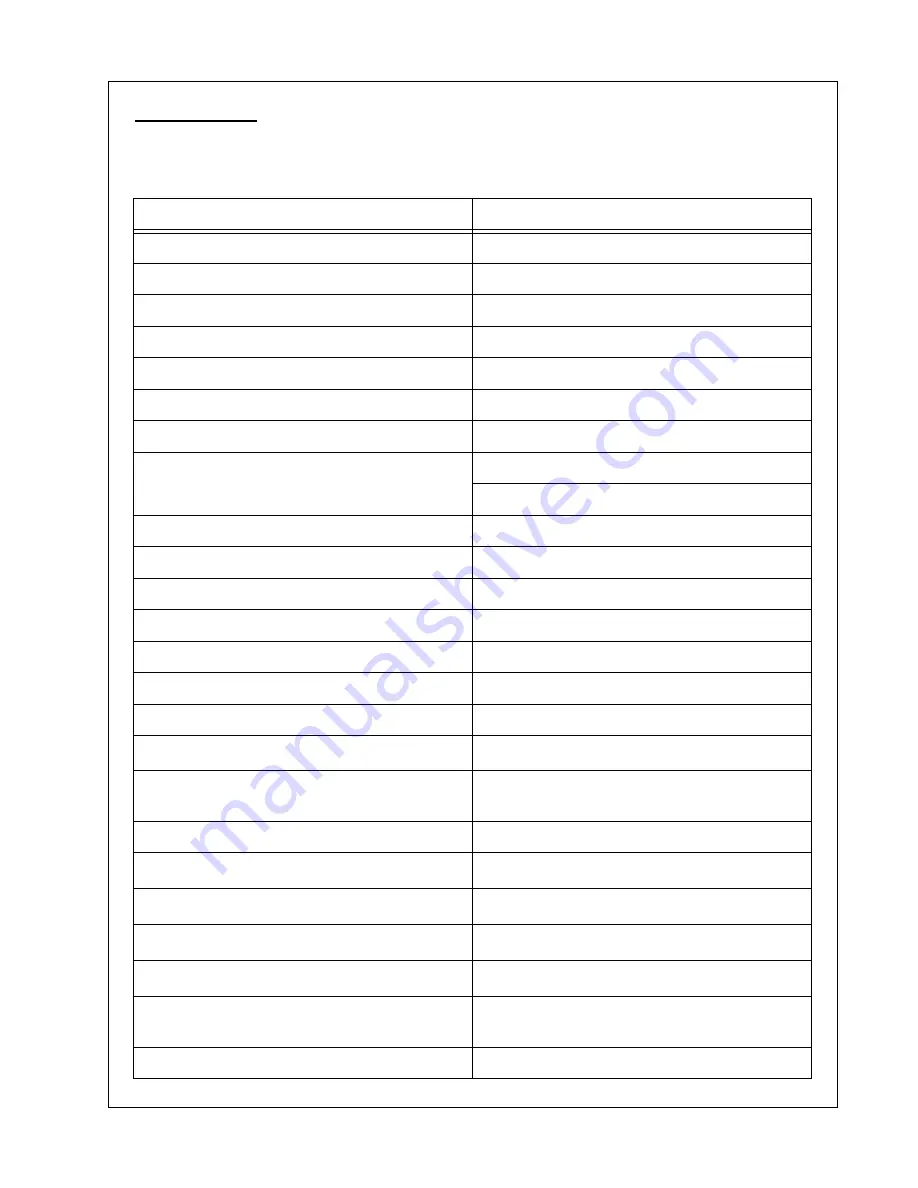
Lubrication
Operating & Maintenance Manual
Book: 23209307 (8-24-2010) Rev D
79
Specifications
General Engine Specifications.
ITEM
4IRD5AE
Number of Cylinders
4
Bore
106 mm (4.19 in.)
Stroke
127 mm (5.0 in.)
Displacement
4.5 L (276 cu in.)
Compression Ratio
17.0:1
Aspiration
Turbocharged
Engine Firing Order
1-3-4-2
Valves Per Cylinder
1 Intake
1 Exhaust
Valve Clearance (Cold)
Intake (Checking)
0.31-0.38 mm (0.012-0.015 in)
Exhaust (Adjusting)
0.36 mm (0.014 in.)
Intake (Checking)
0.31-0.38 mm (0.012-0.015 in)
Exhaust (Checking)
0.41-0.48 mm (0.016-0.019 in)
Intake (Adjusting)
0.36 mm (0.014 in.)
Exhaust (Adjusting)
0.46 mm (0.018 in.)
Max. Crank Pressure
0.5 kPa (2 H
2
O)
Vibration Damper Maximum
Radial Runout
1.50 mm (0.060 in.)
Governor Regulation (Industrial)
7-10%
Thermostat Start To Open
82
°
C
Temperature
(180
°
F)
Thermostat Fully Open
94
°
c
Temperature
(202
°
F)
Oil Pressure At Rated
Speed, Full Load (+15 psi)
345 kPa
(50 psi)
Oil Pressure At Low Idle (Minimum)
105 kPa (15 psi)
Summary of Contents for HP375WJD
Page 2: ...2 ...
Page 7: ...7 TABLE OF CONTENTS Operating Maintenance Manual TITLE PAGE ...
Page 8: ...8 ...
Page 9: ...Book 23209307 8 24 2010 Rev D 9 Foreword ...
Page 12: ...12 Book 23209307 8 24 2010 Rev D ...
Page 13: ...Book 23209307 8 24 2010 Rev D 13 Decals ...
Page 15: ...Decals Operating Maintenance Manual Book 23209307 8 24 2010 Rev D 15 ...
Page 16: ...Operating Maintenance Manual Decals 16 Book 23209307 8 24 2010 Rev D ...
Page 17: ...Decals Operating Maintenance Manual Book 23209307 8 24 2010 Rev D 17 ...
Page 19: ...Decals Operating Maintenance Manual Book 23209307 8 24 2010 Rev D 19 ...
Page 20: ...Operating Maintenance Manual Decals 20 Book 23209307 8 24 2010 Rev D ...
Page 22: ...Operating Maintenance Manual Decals 22 Book 23209307 8 24 2010 Rev D ...
Page 23: ...Book 23209307 8 24 2010 Rev D 23 Noise Emission ...
Page 28: ...28 Book 23209307 8 24 2010 Rev D ...
Page 29: ...Book 23209307 8 24 2010 Rev D 29 Safety ...
Page 34: ...34 Book 23209307 8 24 2010 Rev D ...
Page 35: ...Book 23209307 8 24 2010 Rev D 35 General Arrangement ...
Page 43: ...Book 23209307 8 24 2010 Rev D 43 Operating Instructions ...
Page 61: ...Book 23209307 8 24 2010 Rev D 61 Lubrication ...
Page 82: ...82 Book 23209307 8 24 2010 Rev D ...
Page 83: ...Book 23209307 8 24 2010 Rev D 83 Maintenance ...
Page 101: ...Maintenance Operating Maintenance Manual Book 23209307 8 24 2010 Rev D 101 ...
Page 102: ...Operating Maintenance Manual Maintenance 102 Book 23209307 8 24 2010 Rev D ...
Page 105: ...Book 23209307 8 24 2010 Rev D 105 Machine Systems ...
Page 110: ...Operating Maintenance Manual Machine Systems 110 Book 23209307 8 24 2010 Rev D ...
Page 111: ...Book 23209307 8 24 2010 Rev D 111 Service Tools ...
Page 117: ...Book 23209307 8 24 2010 Rev D 117 Fault Finding ...
Page 122: ...122 22442578 ...
Page 123: ...Book 23209307 8 24 2010 Rev D 123 Options ...
Page 126: ...126 Book 23209307 8 24 2010 Rev D ...