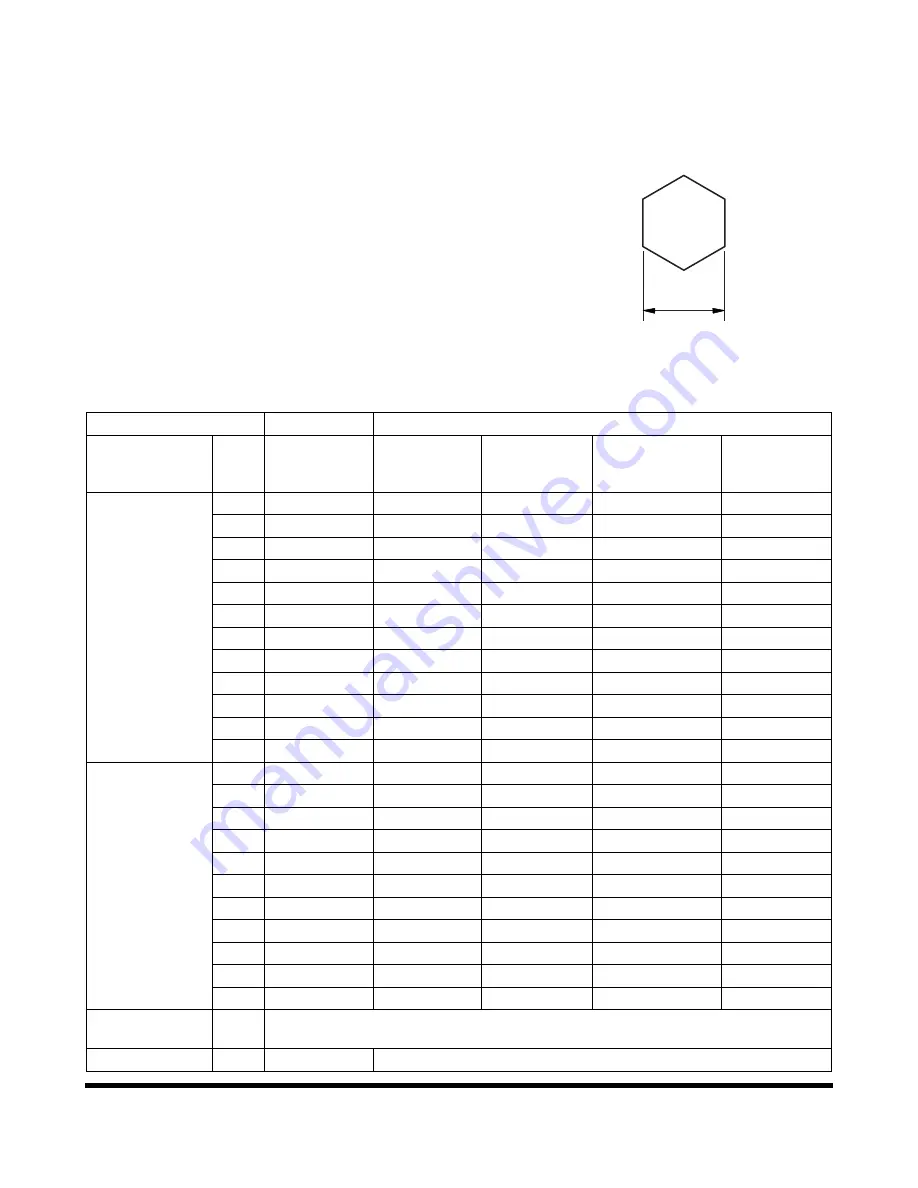
SP001945
Main Pump
Page 6
DISASSEMBLING AND
REASSEMBLING PROCEDURES
Tool
The tools necessary to disassemble / reassemble K7V pump are
shown in the following list.
The size of the bolts and plugs depend on the pump type.
FG015033
B
Figure 1
Tool Name & Size
Ο
Necessary
Part Name
Name
B
K7V63
Hexagon
socket head
cap screw
Pressure plug
(PT screw)
ROH plug
VP plug, UNF plug
(PF screw)
Hexagon
socket head
set screw
Allen wrench
2
−
−
−
M4
2.5
−
−
−
M5
3
−
−
−
M6
4
Ο
M5
Rc1/16
−
M8
5
Ο
M6
Rc1/8
−
M10
6
Ο
M8
Rc1/4
G1/4
M12, M14
8
Ο
M10
Rc3/8
G3/8
M16, M18
10
Ο
M12
Rc1/2
G1/2
M20
12
M14
−
−
−
14
Ο
M16, M18
Rc3
G3/4
−
17
Ο
M20, M22
Rc1
G1
−
19
M24, M27
−
−
−
Double ring
spanner, socket
wrench
Double
(single) open
end spanner
19
M12
−
G 1/4
−
22
−
−
3/4-16UNF
−
24
Ο
M16
−
−
−
27
M18
−
G 1/2
−
30
M20
−
−
−
32
−
−
1 1/16-12UN
−
36
−
−
G 3/4
−
41
Ο
−
−
G 1
−
46
M30
−
−
−
50
−
−
G1 1/4
−
55
M36
−
G1 1/2
−
Adjustable
angle wrench
-
Medium size, 1set
Torque wrench
−
Ο
Capable tightening with the specified torques
Summary of Contents for DX140LCR
Page 1: ...Shop Manual DX140R DX140LCR Serial Number 5001 and Up K1049551BE July 2011 EXCAVATOR ...
Page 2: ......
Page 4: ......
Page 6: ......
Page 9: ...1Safety ...
Page 10: ......
Page 12: ...SP002281 Track Excavator Safety Page 2 MEMO ...
Page 14: ...SP002281 Track Excavator Safety Page 4 MEMO ...
Page 57: ...1Specifications ...
Page 58: ......
Page 60: ...SP002379 Specification for DX140LCR Page 2 MEMO ...
Page 62: ...SP002379 Specification for DX140LCR Page 4 MEMO ...
Page 83: ...1General Maintenance ...
Page 84: ......
Page 86: ...SP000016 General Maintenance Procedures Page 2 MEMO ...
Page 88: ...SP000016 General Maintenance Procedures Page 4 MEMO ...
Page 104: ...SP000016 General Maintenance Procedures Page 20 ...
Page 105: ...SP000813 Page 1 Standard Torques SP000813 STANDARD TORQUESSP000813 Standard Torques Edition 1 ...
Page 106: ...SP000813 Standard Torques Page 2 MEMO ...
Page 108: ...SP000813 Standard Torques Page 4 MEMO ...
Page 121: ...1Upper Structure ...
Page 122: ......
Page 123: ...SP002282 Page 1 Cabin SP002282 CABIN SP002282 Cabin Edition 1 ...
Page 124: ...SP002282 Cabin Page 2 MEMO ...
Page 126: ...SP002282 Cabin Page 4 MEMO ...
Page 136: ...SP002282 Cabin Page 14 ...
Page 137: ...SP001939 Page 1 Counterweight SP001939 COUNTERWEIGHT SP001939 Counterweight Edition 1 ...
Page 138: ...SP001939 Counterweight Page 2 MEMO ...
Page 140: ...SP001939 Counterweight Page 4 MEMO ...
Page 147: ...SP001940 Page 1 Fuel Tank SP001940 FUEL TANK SP001940 Fuel Tank Edition 1 ...
Page 148: ...SP001940 Fuel Tank Page 2 MEMO ...
Page 150: ...SP001940 Fuel Tank Page 4 MEMO ...
Page 162: ...SP001940 Fuel Tank Page 16 ...
Page 164: ...SP000021 Fuel Transfer Pump Page 2 MEMO ...
Page 166: ...SP000021 Fuel Transfer Pump Page 4 MEMO ...
Page 171: ...SP001856 Page 1 Swing Bearing SP001856 SWING BEARING SP001856 Swing Bearing Edition 1 ...
Page 172: ...SP001856 Swing Bearing Page 2 MEMO ...
Page 174: ...SP001856 Swing Bearing Page 4 MEMO ...
Page 180: ...SP001856 Swing Bearing Page 10 ...
Page 182: ...SP000921 Swing Reduction Gear Page 2 MEMO ...
Page 184: ...SP000921 Swing Reduction Gear Page 4 MEMO ...
Page 186: ...SP000921 Swing Reduction Gear Page 6 ...
Page 192: ...SP000921 Swing Reduction Gear Page 12 Figure 7 ...
Page 222: ...SP000921 Swing Reduction Gear Page 42 ...
Page 223: ...1Lower Structure and Chassis ...
Page 224: ......
Page 225: ...SP001941 Page 1 Track Assembly SP001941 TRACK ASSEMBLY SP001941 Track Assembly Edition 1 ...
Page 226: ...SP001941 Track Assembly Page 2 MEMO ...
Page 228: ...SP001941 Track Assembly Page 4 MEMO ...
Page 234: ...SP001941 Track Assembly Page 10 Track Shoe 8 7 2 10 11 9 FG003910 1 3 6 4 5 Figure 4 ...
Page 255: ...1Engine and Drive Train ...
Page 256: ......
Page 257: ...SP001671 Page 1 QSB4 5 Engine SP001671 QSB4 5 ENGINESP001671 QSB4 5 Engine Edition 1 ...
Page 258: ...SP001671 QSB4 5 Engine Page 2 MEMO ...
Page 264: ...SP001671 QSB4 5 Engine Page 8 QSB4 5 ENGINE Figure 1 ...
Page 311: ...SP001671 Page 55 QSB4 5 Engine Figure 32 ...
Page 532: ...SP001326 Drive Coupling Main Pump Page 2 MEMO ...
Page 534: ...SP001326 Drive Coupling Main Pump Page 4 MEMO ...
Page 536: ...SP001326 Drive Coupling Main Pump Page 6 ...
Page 542: ...SP001326 Drive Coupling Main Pump Page 12 ...
Page 543: ...1Hydraulics ...
Page 544: ......
Page 546: ...SP001942 Hydraulic System Troubleshooting Testing and Adjustment Page 2 MEMO ...
Page 580: ...SP001942 Hydraulic System Troubleshooting Testing and Adjustment Page 36 ...
Page 581: ...SP000028 Page 1 Accumulator SP000028 ACCUMULATOR SP000028 Accumulator Edition 1 ...
Page 582: ...SP000028 Accumulator Page 2 MEMO ...
Page 584: ...SP000028 Accumulator Page 4 MEMO ...
Page 590: ...SP000029 Center Joint Swivel Page 2 MEMO ...
Page 592: ...SP000029 Center Joint Swivel Page 4 MEMO ...
Page 599: ...SP000030 Page 1 Cylinders SP000030 CYLINDERS SP000030 Cylinders Edition 1 ...
Page 600: ...SP000030 Cylinders Page 2 MEMO ...
Page 602: ...SP000030 Cylinders Page 4 MEMO ...
Page 628: ...SP000030 Cylinders Page 30 ...
Page 629: ...SP001943 Page 1 Swing Motor SP001943 SWING MOTOR SP001943 Swing Motor Edition 1 ...
Page 630: ...SP001943 Swing Motor Page 2 MEMO ...
Page 632: ...SP001943 Swing Motor Page 4 MEMO ...
Page 664: ...SP001943 Swing Motor Page 36 ...
Page 665: ...SP001346 Page 1 Travel Moter SP001346 TRAVEL MOTER SP001346 Travel Moter Edition 1 ...
Page 666: ...SP001346 Travel Moter Page 2 MEMO ...
Page 671: ...SP001346 Page 7 Travel Moter EXTERNAL DIMENSIONS Figure 1 ...
Page 672: ...SP001346 Travel Moter Page 8 GENERAL DESCRIPTION Figure 2 ...
Page 680: ...SP001346 Travel Moter Page 16 Figure 6 ...
Page 736: ...SP001346 Travel Moter Page 72 ...
Page 737: ...SP001945 Page 1 Main Pump SP001945 MAIN PUMP SP001945 Main Pump Edition 1 ...
Page 738: ...SP001945 Main Pump Page 2 MEMO ...
Page 740: ...SP001945 Main Pump Page 4 ...
Page 752: ...SP001945 Main Pump Page 16 Installation of Tandem Type Double pump Figure 25 ...
Page 753: ...SP001945 Page 17 Main Pump Construction of Tandem Type Double Pump Figure 26 ...
Page 756: ...SP001029 Main Control Valve Page 2 MEMO ...
Page 758: ...SP001029 Main Control Valve Page 4 MEMO ...
Page 760: ...SP001029 Main Control Valve Page 6 GENERAL DESCRIPTION Figure 1 ...
Page 774: ...SP001029 Main Control Valve Page 20 Figure 19 Figure 20 ...
Page 806: ...SP001646 Remote Control Valve Work Lever Joystick Page 2 MEMO ...
Page 808: ...SP001646 Remote Control Valve Work Lever Joystick Page 4 MEMO ...
Page 810: ...SP001646 Remote Control Valve Work Lever Joystick Page 6 ...
Page 812: ...SP001646 Remote Control Valve Work Lever Joystick Page 8 Parts List Figure 1 ...
Page 826: ...SP001646 Remote Control Valve Work Lever Joystick Page 22 ...
Page 828: ...SP002262 Travel Control Valve with Damper Page 2 MEMO ...
Page 830: ...SP002262 Travel Control Valve with Damper Page 4 MEMO ...
Page 832: ...SP002262 Travel Control Valve with Damper Page 6 ...
Page 836: ...SP002262 Travel Control Valve with Damper Page 10 ...
Page 838: ...SP002262 Travel Control Valve with Damper Page 12 Parts List Figure 3 ...
Page 852: ...SP002262 Travel Control Valve with Damper Page 26 ...
Page 854: ...SP001944 Solenoid Valve Assembly Page 2 MEMO ...
Page 856: ...SP001944 Solenoid Valve Assembly Page 4 MEMO ...
Page 863: ...SP001944 Page 11 Solenoid Valve Assembly Solenoid Valve Diagram Figure 3 ...
Page 866: ...SP001944 Solenoid Valve Assembly Page 14 ...
Page 868: ...SP000192 Breaker EPPR Valve Opt Page 2 MEMO ...
Page 870: ...SP000192 Breaker EPPR Valve Opt Page 4 MEMO ...
Page 880: ...SP002383 Hydraulic Schematic DX140LCR Page 2 MEMO ...
Page 882: ...SP002383 Hydraulic Schematic DX140LCR Page 4 MEMO ...
Page 884: ...SP002383 Hydraulic Schematic DX140LCR Page 6 ...
Page 886: ...1Electrical System ...
Page 887: ......
Page 889: ...SP001949 Electrical System Page 2 MEMO ...
Page 892: ...SP001949 Electrical System Page 5 MEMO ...
Page 948: ...SP001949 Page 61 Electrical System ...
Page 962: ...SP001949 Page 75 Electrical System ...
Page 1001: ...SP002271 Electrical Schematic DX140LCR Page 2 MEMO ...
Page 1003: ...SP002271 Electrical Schematic DX140LCR Page 4 MEMO ...
Page 1005: ...SP002271 Electrical Schematic DX140LCR Page 6 ...
Page 1007: ...1Attachments ...
Page 1008: ......
Page 1009: ...SP002378 Page 1 Boom and Arm SP002378 Boom and Arm Edition 1 ...
Page 1010: ...SP002378 Boom and Arm Page 2 MEMO ...
Page 1012: ...SP002378 Boom and Arm Page 4 MEMO ...
Page 1020: ...SP002378 Boom and Arm Page 12 ...
Page 1021: ...Bucket Page 1 SP000939 SP000939 BUCKET SP000939 1Bucket Edition 1 ...
Page 1022: ...Bucket SP000939 Page 2 MEMO ...
Page 1024: ...Bucket SP000939 Page 4 MEMO ...
Page 1031: ......
Page 1032: ...2905 Shawnee Industrial Way Suite 100 Suwanee GA 30024 ...