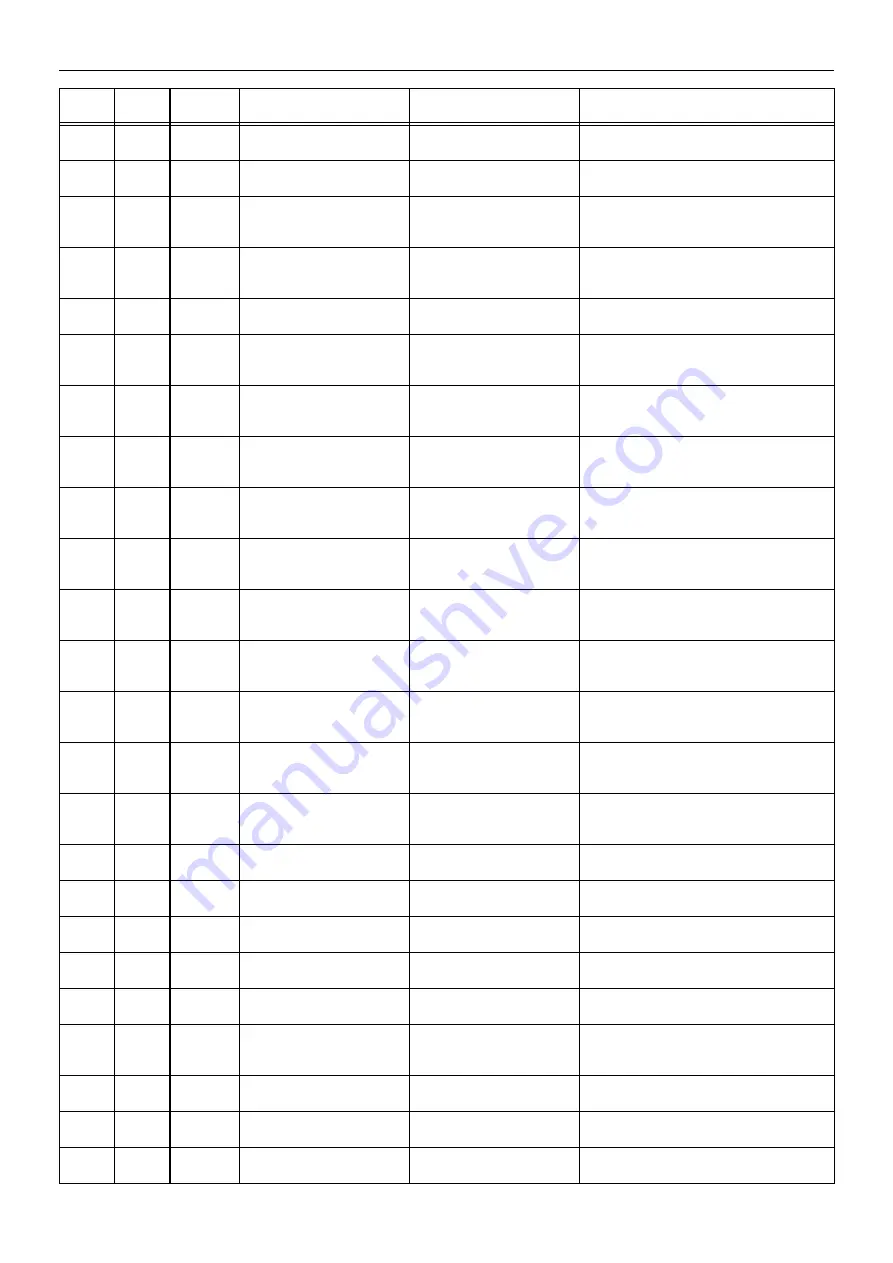
OPERATING INSTRUCTIONS
19
9/275, 9/305, 12/250, 17/240, 21/220
J1939
SPN
J1939
FMI
CUMMINS
CODE
J1939 SPN DESCRIPTION
J1939 FMI DESCRIPTION
CUMMINS DESCRIPTION
101
3
1843
Engine Crankcase Pressure
Voltage Above Normal, or
Shorted to HighSource
Crankcase Pressure Circuit - Voltage Above
Normal, or Shorted to High Source
101
4
1844
Engine Crankcase Pressure
Voltage Below Normal, or
Shorted to Low Source
Crankcase Pressure Circuit - Below Normal, or
Shorted to Low Source
101
15
1974
Engine Crankcase Pressure
Data Valid but Above Normal
Operating Range - Least
Severe Level
Crankcase Pressure - Data Valid But Above
Normal Operating Range - Least Severe Level
101
16
555
Engine Crankcase Pressure
Data Valid but Above Normal
Operating Range - Moderately
Severe Level
Crankcase Pressure - Data Valid But Above
Normal Operating Range - Moderately Severe
Level
102
2
2973
Engine Intake Manifold #1
Pressure
Data Erratic, Intermittent or
Incorrect
Intake Manifold Pressure Sensor Circuit - Data
Erratic, Intermittent, or Incorrect
102
3
122
Engine Intake Manifold #1
Pressure
Voltage Above Normal, or
Shorted to High Source
Intake Manifold Pressure Sensor Circuit -
Voltage Above Normal, or Shorted to High
Source
102
4
123
Engine Intake Manifold #1
Pressure
Voltage Below Normal, or
Shorted to Low Source
Intake Manifold Pressure Sensor Circuit -
Voltage Below Normal, or Shorted to Low
Source
102
18
125
Engine Intake Manifold #1
Pressure
Data Valid but Below Normal
Operating Range - Moderately
Severe Level
Intake Manifold 1 Pressure - Data Valid But
Below Normal Operating Range - Moderately
Severe Level
103
15
2288
Engine Turbocharger 1 Speed Data Valid but Above Normal
Operating Range Least
Severe Level
Turbocharger 1 Speed - Data Valid But Above
Normal Operating Range - Least Severe Level
103
16
595
Engine Turbocharger 1 Speed Data Valid but Above Normal
Operating Range - Moderately
Severe Level
Turbocharger #1 Speed High - Data Valid but
Above Normal Operational Range -
Moderately Severe Level
103
18
687
Engine Turbocharger 1 Speed Data Valid but Below Normal
Operating Range - Moderately
Severe Level
Turbocharger #1 Speed Low - Data Valid but
Below Normal Operational Range - Moderately
Severe Level
105
0
155
Engine Intake Manifold 1
Temperature
Data Valid but Above Normal
Operational Range - Most
Severe Level
Intake Manifold Air Temperature High - Data
Valid but Above Normal Operational Range -
Most Severe Level
105
3
153
Engine Intake Manifold 1
Temperature
Voltage Above Normal, or
Shorted to High Source
Intake Manifold Air Temperature Sensor Circuit
- Voltage Above Normal, or Shorted to High
Source
105
4
154
Engine Intake Manifold 1
Temperature
Voltage Below Normal, or
Shorted to Low Source
Intake Manifold Air Temperature Sensor Circuit
- Voltage Below Normal, or Shorted to Low
Source
105
16
488
Engine Intake Manifold 1
Temperature
Data Valid but Above Normal
Operating Range - Moderately
Severe Level
Intake Manifold 1 Temperature - Data Valid but
Above Normal Operational Range -
Moderately Severe Level
108
2
295
Barometric Pressure
Data Erratic, Intermittent or
Incorrect
Barometric Pressure Sensor Circuit - Data
Erratic, Intermittent, or Incorrect
108
3
221
Barometric Pressure
Voltage Above Normal, or
Shorted to High Source
Barometric Pressure Sensor Circuit - Voltage
Above Normal, or Shorted to High Source
108
4
222
Barometric Pressure
Voltage Below Normal, or
Shorted to Low Source
Barometric Pressure Sensor Circuit - Voltage
Below Normal, or Shorted to Low Source
108
9
3372
Barometric Pressure
Abnormal Update Rate
Turbocharger 1 Compressor Inlet Pressure -
Abnormal Update Rate
108
19
3373
Barometric Pressure
Received Network Data in
Error
Turbocharger 1 Compressor Inlet Pressure -
Received Network Data In Error
110
0
151
Engine Coolant Temperature
Data Valid but Above Normal
Operational Range - Most
Severe Level
Coolant Temperature High - Data Valid but
Above Normal Operational Range - Most
Severe Level
110
3
144
Engine Coolant Temperature
Voltage Above Normal, or
Shorted to High Source
Coolant Temperature Sensor Circuit - Voltage
Above Normal, or Shorted to High Source
110
4
145
Engine Coolant Temperature
Voltage Below Normal, or
Shorted to Low Source
Coolant Temperature Sensor Circuit - Voltage
Below Normal, or Shorted to Low Source
110
14
1847
Engine Coolant Temperature
Special Instructions
Engine Coolant Temperature - Special
Instructions