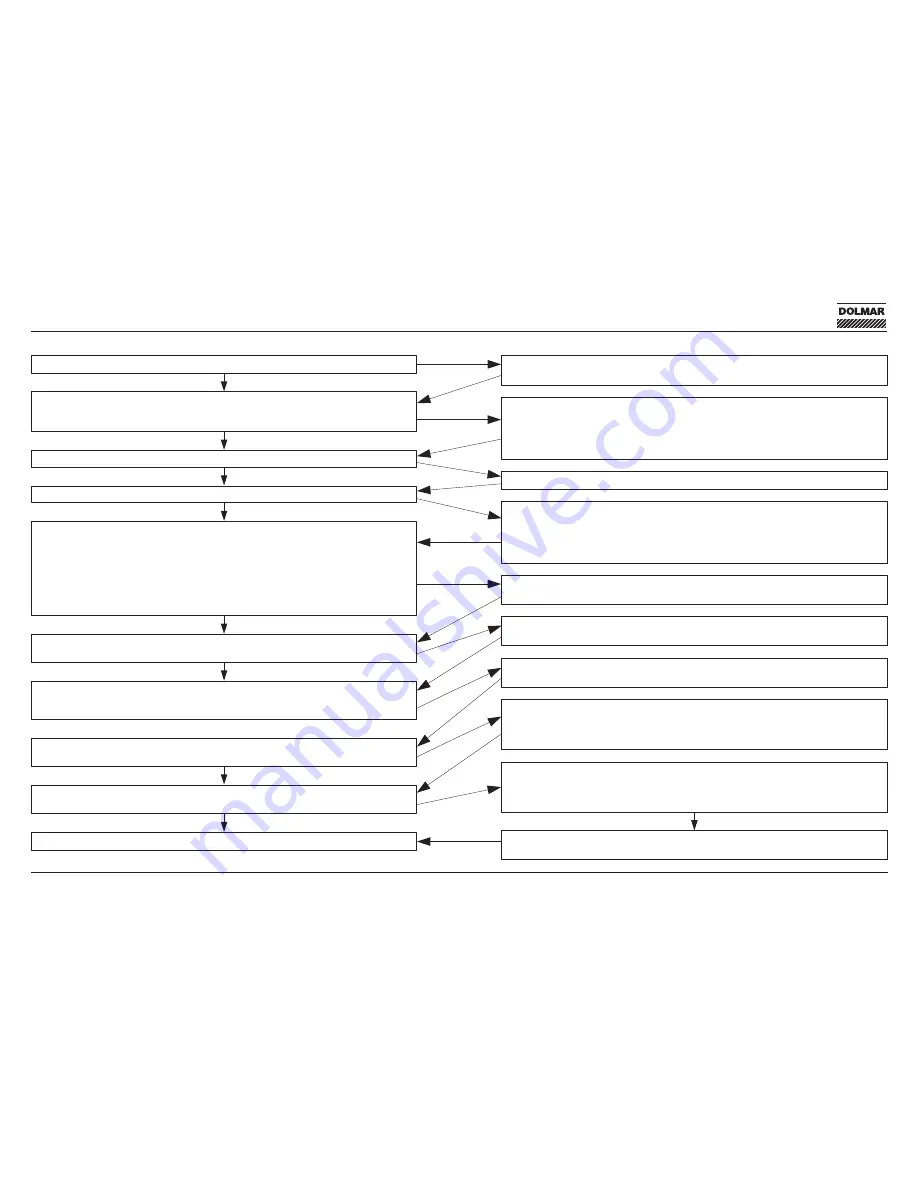
24
Repair Manual PS-6400/PS-7300/PS-7900
yes
Is the ignition plug dry and correctly fastened?
Is the distance between the electrodes correct? (Should be 0.5 mm)
Is the ignition plug full of oil and sooted?
Install ignition testing lamp.
Alternatively insert combination wrench between cylinder and hood, wrench must have
metallic contact with the cylinder. Caution: Do not insert the wrench into the ignition
plug hole or hold with hand.
Push the removed ignition plug with insulated pliers against the wrench.
Caution: Do not hold the ignition plug directly against the hole. Low-speed detonation!
Pull quickly on the starting rope. Is there an ignition sparc?
Are there damages on the insulation of the high-voltage cables or the ignition plug
cable?
Remove the stop switch and set to ON. Does the switch have a low resistance? 10
Kilo Ohm or less?
Is the distance between the pole wheel and the ignition module greater than 0.3 mm?
Remove pole wheel and check. Is the pole wheel damaged? Is the spring fro
positioning damaged?
Continue with trouble shooting in fuel system (tank, fuel hose, carburetor).
Remove ignition plug. Is ignition plug damaged? has a wrong ignition plug been
used? Are the electrodes sooted?
no
yes
no
yes
no
no
no
no
no
no
no
no
yes
yes
yes
yes
yes
yes
no
no
no
Dry plug and fasten firmly on ignition plug. If needed, replace plug or spring in the
ignition plug.
Replace ignition plug. Use ONLY ignition plugs approved by DOLMAR. See operating
manual! Otherwise the ignition module might get damaged remove the causes for
sooted electrodes (bad two-tact oil), wrong mix, defect air filter). Use DOLMAR
high-performance two-tact oil.
Adjust ignition distance.
Wash ignition plug in acetone.
Do not sand blast!
If needed, replace ignition plug.
Remove cause: wrong carburetor setting, too much motor oil in fuel, frequent short
operations.
Replace ignition plug and check ignition module for corrosion, if needed replace. Has
the defect been removed.
Replace ignition cable and/or short-circuit cable. Has the defect been removed.
Replace stop switch
Has the defect been removed?
Check radial play of driving shaft and repair bearing if needed. Replace ignition
module if traces of overheating become visible. Distance pole wheel – adjust ignition
module correctly.
Replace pole wheel or spring. Wash cone seat at drive shaft and pole wheel before
installation with acetone or alcohol to remove any grease. Heed the torque of the
fastening nut! Has the defect been removed?
Replace ignition module. Has the defect been removed.?
no
07
I G N I T I O N S Y S T E M
Inspecting the ignition system