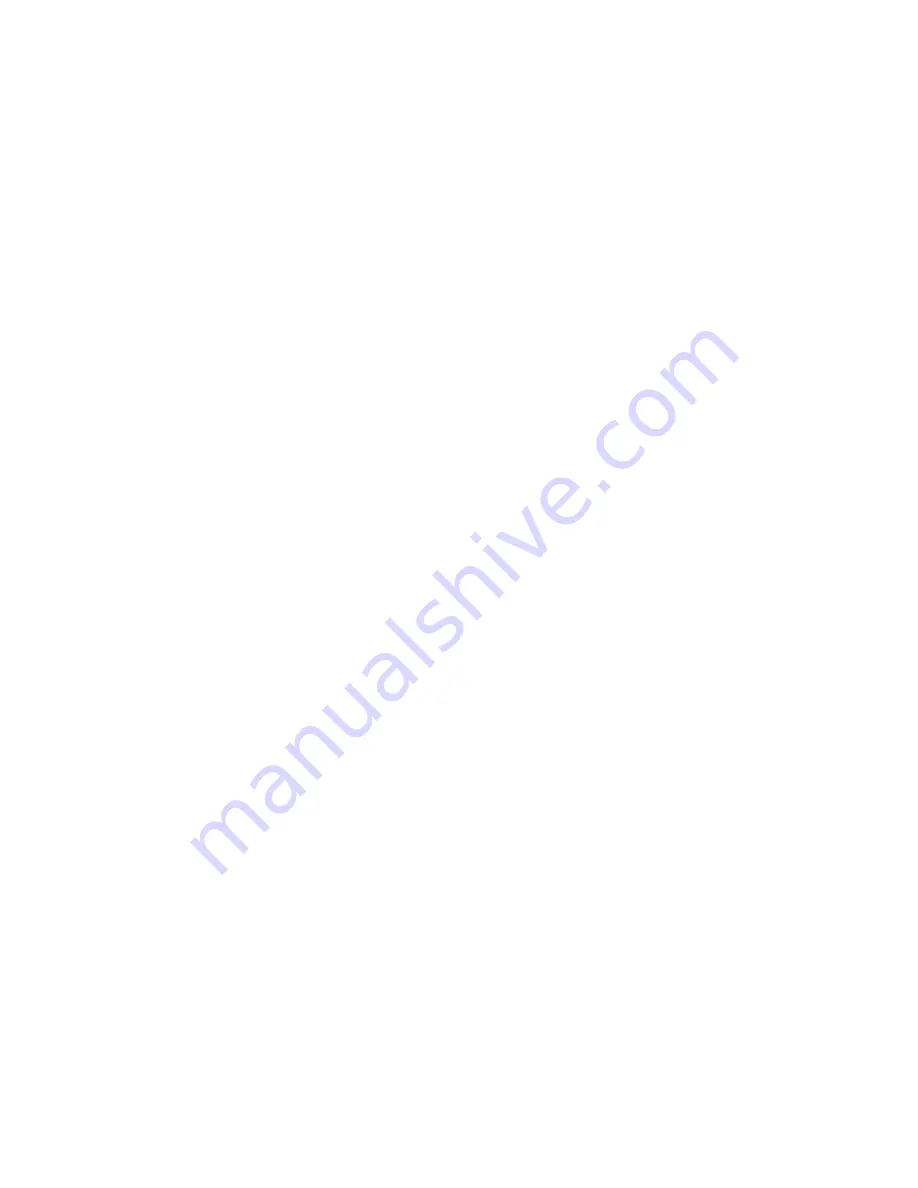
19
MN1620
Ordering Parts
When ordering parts for reducer, specify reducer size number,
reducer model number, part name, part number, and quantity. It
is strongly recommended that, when a pinion or gear is replaced,
the mating pinion or gear is replaced also.
If the large gear on the output hub must be replaced, it is
recommended that an output hub assembly consisting of a gear
assembled on a hub be ordered to ensure undamaged surfaces
on the output hub where the output seals rub. However, if it is
desired to use the old output hub, press the gear and bearing off
and examine the rubbing surface under the oil seal carefully for
possible scratching or other damage resulting from the pressing
operation. To prevent oil leakage at the shaft oil seals, the smooth
surface of the output hub must not be damaged.
If any parts must be pressed from a shaft or from the output hub,
this should be done before ordering parts to make sure that none
of the bearings or other parts are damaged in removal. Do not
press against rollers or cage of any bearing. Because old shaft
oil seals may be damaged in disassembly, it is advisable to order
replacements for these parts.
Removing Reducer from Shaft
WARNING: To ensure that drive is not unexpectedly started,
turn off and lock out or tag power source before proceeding.
Remove all external loads from drive before removing or
servicing drive or accessories. Failure to observe these
precautions could result in bodily injury.
Taper Bushed
1. Disconnect and remove belt guard, v-drive, and motor mount
as required. Disconnect torque arm rod from reducer adapter.
2. Remove bushing screws.
3. Place the screws in the threaded holes provided in the
bushing flanges. Tighten the screws alternately and evenly
until the bushings are free on the shaft. For ease of tightening
screws, make sure screw threads and threaded holes in
bushing flanges are clean. A tap can be used to clean out the
threads. Use caution to use the proper size tap to prevent
damage to the threads.
4. Remove the outside bushing, the reducer, and then the
inboard bushing.
Disassembly
1. Drain all oil from the reducer.
2. Position the reducer on its side and remove all housing
bolts. Drive dowel pins from housing. Using the three pry
slots around the periphery of the flange, gently separate the
housing halves. Open housing evenly to prevent damage to
the parts inside.
3. Lift input shaft, all gear assemblies, and bearing assemblies
from housing.
4. Remove seals from housing.
5. Remove bearings from shafts and hubs. Be careful not to
scratch or damage any assembly or seal area during bearing
removal. The hub assembly can be disassembled for gear
replacement but if scratching or grooving occurs on the hub,
seal leakage will occur and the hub will need to be replaced.
Reassembly
1. Output Hub Assembly:
Heat gear to 162ºC to 176ºC to
shrink onto hub. Heat bearings to 132ºC to 143ºC to shrink
onto hub. Any injury to the hub surfaces where the oil seals
rub will cause leakage, making it necessary to use a new hub.
2. Countershaft Assembly:
Shaft and pinion are integral.
Press gear and bearings on shaft. Press against inner race
(not cage or rollers) of bearings.
3. Input Shaft Assembly:
Shaft and pinion are integral. Press
bearings on shaft. Press against inner race (not cage or
rollers) of bearings.
4. Drive the two dowel pins into place in the right-hand housing
half.
5. Place R.H. housing half on blocks to allow for protruding end
of output hub.
6. Install bearing cups in right-hand housing half, making sure
they are properly seated. The output hub assembly has
one bearing pressed against the gear and the other bearing
pressed against a shoulder on the hub. For double reduction
reducers, install the output hub assembly so that the end
where the bearing is pressed against the gear is up. For single
reduction reducers, install the output hub assembly so that
the end where the bearing is pressed against the gear is
down.
7. Mesh output hub gear and small countershaft gear together
and set in place in housing. Set input shaft assembly in place
in the housing. Make sure bearing rollers (cones) are properly
seated in their cups. Set bearing cups for left-hand housing
half in place on their rollers.
8. Making sure both housing halves are clean, set lefthand
housing half into position and tap with a soft hammer
(rawhide, not lead hammer) until housing bolts can be used
to draw housing halves together. Make sure reducer shafts do
not bind while tightening housing bolts.
9. Rotate the input shaft and seat all bearings with a soft
hammer. Using a magnetic base and indicator, measure and
record the endplay of the input shaft, countershaft, and output
hub. Remove left housing half and shim behind the bearing
cup as required to achieve the correct bearing endplay or
preload per Table 10. Repeat this process and check endplay
until proper endplay is obtained. Note that the output shaft is
preloaded. After endplay is determined, add the correct shim
thickness to the endplay reading to obtain the correct preload.
10. Remove left housing half and clean housing flange surfaces
on both halves, making sure not to nick or scratch flange face.
Place a 3.0mm bead of Dow RTV732 sealant or equivalent
on flange face (make sure RTV is placed around bolt holes
and inside of flange face). Place left housing half into position
and tap with a soft hammer (rawhide, not lead hammer) until
housing bolts can be used to draw housing halves together.
Torque housing bolts per torque values listed in Table 11.
11. Install input seal, output seals, and auxiliary seals. Extreme
care should be used when installing seals to avoid damage
due to contact with sharp edges on the input shaft or output
hub. The possibility of damage and consequent oil leakage
can be decreased by covering all sharp edges with tape prior
to seal installation. Lightly coat the seal lips with Mobilith AW2
All-Purpose grease or equivalent. Seals should be pressed
or tapped with a soft hammer evenly into place in the reducer
housing, applying pressure only on the outer edge of the
seals. A slight oil leakage at the seals may be evident during
initial running, but should disappear unless seals have been
damaged.
12. Install bushing backup plates and snap rings on Taper
Bushed reducers or hub collars on straight bore reducers.
Summary of Contents for Ratios 15
Page 31: ...31 MN1620...