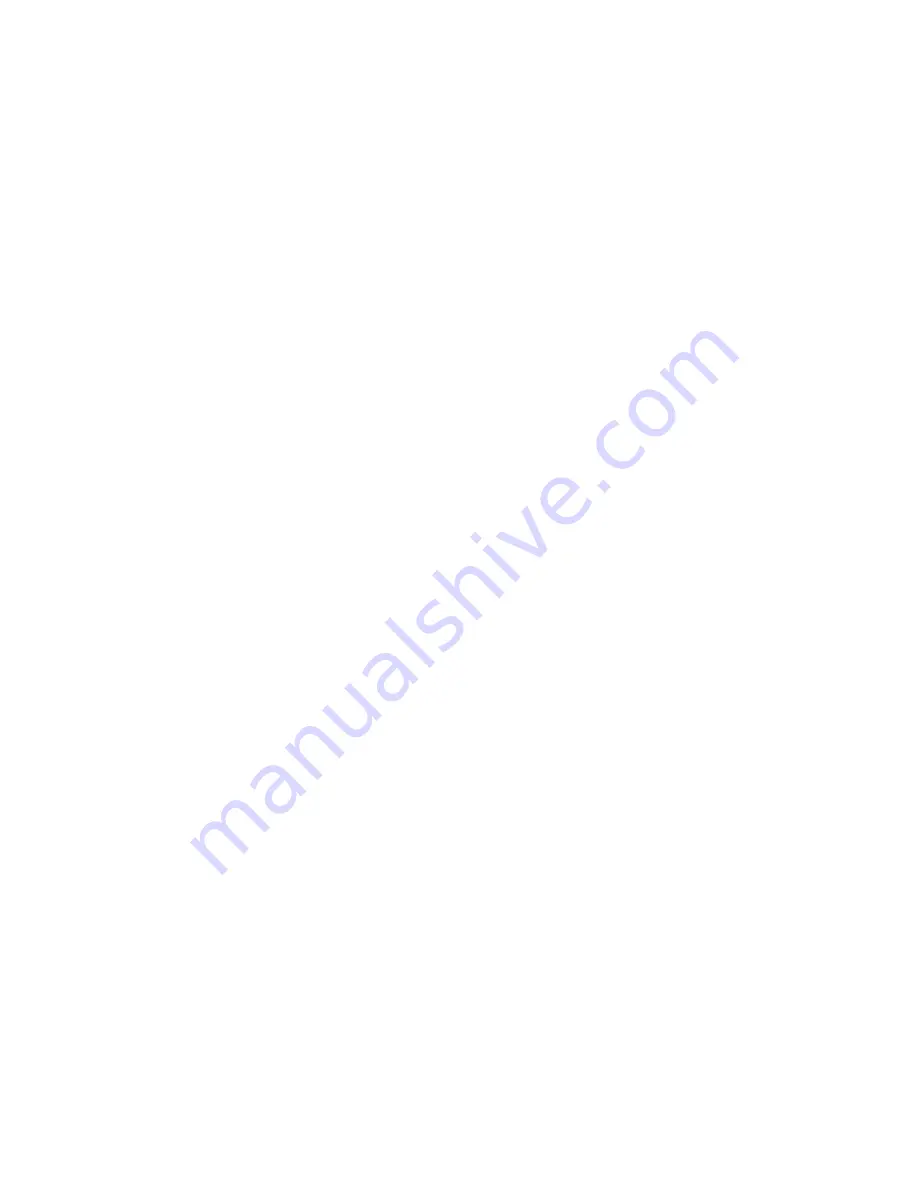
Threads damaged ......... A ................. Require repair.
Threads stripped (threads
missing) ............... A ............ Require replacement.
METAL AIR PIPES
See METAL AIR MANIFOLDS AND PIPES.
MIX CONTROL SOLENOIDS
MIX CONTROL SOLENOID INSPECTION
Condition Code Procedure
Attaching hardware
missing ................ C .......... Require replacement of
hardware.
Attaching hardware
threads damaged ........ A ... Require repair or replacement
of hardware.
Attaching hardware
threads stripped
(threads missing) ...... A ... Require repair or replacement
of hardware.
Connector broken ........ A .. Require repair or replacement.
Connector (Weatherpack
type) leaking .......... A .. Require repair or replacement.
Connector melted ........ A ........... ( 1) Require repair or
replacement.
Connector missing ....... C ............ Require replacement.
Contaminated ............ A ........... ( 2) Require repair or
replacement.
Inoperative ............. B ........... ( 3) Require repair or
replacement. Further
inspection required.
Leaking ................. A .. Require repair or replacement.
Missing ................. C ............ Require replacement.
Resistance out of
specification .......... B .. Require repair or replacement.
Restricted, affecting
performance ............ A .. Require repair or replacement.
Terminal broken ......... A .. Require repair or replacement.
Terminal burned, affecting
performance ............ A ........... ( 1) Require repair or
replacement.
Terminal burned, not
affecting performance .. 2 .. Suggest repair or replacement.
Terminal corroded,
affecting performance .. A .. Require repair or replacement.
Terminal corroded, not
affecting performance .. 2 .. Suggest repair or replacement.
Terminal loose, affecting
performance ............ B .. Require repair or replacement.
Terminal loose, not
affecting performance .. 1 .. Suggest repair or replacement.
Threads damaged ......... A .. Require repair or replacement.
Threads stripped (threads
missing) ............... A ............ Require replacement.
Wire lead conductors
exposed ................ B .. Require repair or replacement.
Wire lead corroded ...... A .. Require repair or replacement.
Wire lead open .......... A .. Require repair or replacement.
Summary of Contents for R1500 1999
Page 46: ...Fig 2 Blower Motor System Diagnosis Except RWD Van Courtesy of Chrysler Corp...
Page 47: ...Fig 3 Blower Motor Control System Diagnosis RWD Van Courtesy of Chrysler Corp...
Page 48: ...Fig 4 Blower Motor Noise Vibration Diagnosis Courtesy of Chrysler Corp...
Page 49: ...Fig 5 A C Compressor Compressor Clutch Diagnosis 1 Of 2 Courtesy of Chrysler Corp...
Page 50: ...Fig 6 A C Compressor Compressor Clutch Diagnosis 2 Of 2 Courtesy of Chrysler Corp...
Page 51: ...Fig 7 A C Diagnosis Fixed Displacement Compressors Courtesy of Chrysler Corp...
Page 102: ...Fig 4 A C Heater Housing Removal Installation Dakota Durango Front Courtesy of Chrysler Corp...
Page 113: ...Fig 11 Manual A C Heater System Wiring Diagram Durango Rear Blower...
Page 114: ...Fig 12 Manual A C Heater System Wiring Diagram Durango...
Page 115: ...Fig 13 Manual A C Heater System Wiring Diagram Dakota 2 5L...
Page 116: ...Fig 14 Manual A C Heater System Wiring Diagram Dakota 3 9L 5 2L 5 9L...
Page 117: ...Fig 15 Manual A C Heater System Wiring Diagram Ram Pickup...
Page 122: ...Fig 2 Blower Motor System Diagnosis Except RWD Van Courtesy of Chrysler Corp...
Page 123: ...Fig 3 Blower Motor Control System Diagnosis RWD Van Courtesy of Chrysler Corp...
Page 124: ...Fig 4 Blower Motor Noise Vibration Diagnosis Courtesy of Chrysler Corp...
Page 125: ...Fig 5 A C Compressor Compressor Clutch Diagnosis 1 Of 2 Courtesy of Chrysler Corp...
Page 126: ...Fig 6 A C Compressor Compressor Clutch Diagnosis 2 Of 2 Courtesy of Chrysler Corp...
Page 127: ...Fig 7 A C Diagnosis Fixed Displacement Compressors Courtesy of Chrysler Corp...
Page 135: ...Fig 7 Locating Service Valves Caravan Town Country Voyager Courtesy of chrysler corp...
Page 136: ...Fig 8 Locating Service Valves Windstar Courtesy of ford motor co SERVICE EQUIPMENT...
Page 140: ...Fig 10 Some Moisture In R 134a System Fig 11 Low R 134a Charge...
Page 141: ...Fig 12 Poor R 134a Refrigerant Circulation Fig 13 No R 134a Refrigerant Circulation...
Page 142: ...Fig 14 Insufficient Cooling Of Condenser Or R 134a Refrigerant Overcharge...
Page 143: ...Fig 15 Air In R 134a System...
Page 146: ...Fig 18 Removing Orifice Tube Typical Courtesy of ford motor co...
Page 156: ...Fig 22 Permanent A C System Filters Courtesy of ford motor co...
Page 192: ...Fig 16 Identifying Data Link Connector DLC Terminals Courtesy of DaimlerChrysler Corp...
Page 193: ...Fig 17 Identifying Fuses Junction Block Courtesy of DaimlerChrysler Corp...
Page 209: ...WIRING DIAGRAMS Fig 20 Air Bag System Wiring Diagram...
Page 216: ...Fig 5 Anti Theft System Wiring Diagram Ram Pickup...
Page 217: ...Fig 6 Anti Theft System Wiring Diagram Ram Van Ram Wagon...
Page 225: ...Fig 2 Identifying Data Link Connector DLC Terminals Courtesy of DaimlerChrysler Corp...
Page 273: ...Fig 13 Transmission Wiring Diagram Dakota...
Page 274: ...Fig 14 Transmission Wiring Diagram Durango...
Page 275: ...Fig 15 Transmission Wiring Diagram Pickup 3 9L 5 2L 5 9L 8 0L 1 Of 2...
Page 276: ...Fig 16 Transmission Wiring Diagram Pickup 3 9L 5 2L 5 9L 8 0L 2 Of 2...
Page 277: ...Fig 17 Transmission Wiring Diagram Pickup 5 9L Diesel 1 Of 2...
Page 278: ...Fig 18 Transmission Wiring Diagram Pickup 5 9L Diesel 2 Of 2...
Page 279: ...Fig 19 Transmission Wiring Diagram Ram Van Wagon 1 Of 2...
Page 280: ...Fig 20 Transmission Wiring Diagram Ram Van Wagon 2 Of 2...
Page 281: ...Fig 21 Transmission Wiring Diagram Jeep Grand Cherokee...
Page 285: ...Fig 4 Locating Intake Manifold Air Temperature Sensor Courtesy of Chrysler Corp...
Page 286: ...Fig 5 Locating Intake Manifold Air Heater Relays Courtesy of Chrysler Corp...
Page 403: ...Fig 5 Cruise Control System Wiring Diagram Dakota...
Page 404: ...Fig 6 Cruise Control System Wiring Diagram Durango...
Page 405: ...Fig 7 Cruise Control System Wiring Diagram Ram Pickup...
Page 406: ...Fig 8 Cruise Control System Wiring Diagram Ram Van Ram Wagon...
Page 454: ...Fig 1 Exploded View Of Trac Lok Differential Courtesy of Chrysler Corp...
Page 469: ...Fig 12 Double Cardan Constant Velocity CV U Joint Dakota Ram Pickup Courtesy of Chrysler Corp...
Page 513: ...Idle Air Control Motor 3 9L On throttle body...
Page 514: ...Idle Air Control Motor 5 2L On throttle body...
Page 515: ...Idle Air Control Motor 5 9L On throttle body Idle Air Control Motor 8 0L On throttle body...
Page 517: ...Crankshaft Position Sensor 3 9L Right rear of engine block...
Page 518: ...Crankshaft Position Sensor 5 2L Right rear of engine block...
Page 524: ...Intake Air Temperature Sensor Diesel In left rear side of intake manifold...
Page 525: ...Intake Air Temperature Sensor 3 9L In right front side of intake manifold...
Page 526: ...Intake Air Temperature Sensor 5 2L In right front side of intake manifold...
Page 527: ...Intake Air Temperature Sensor 5 9L In right front side of intake manifold...
Page 529: ...Manifold Absolute Pressure MAP Sensor 5 2L On throttle body...
Page 530: ...Manifold Absolute Pressure MAP Sensor 5 9L On throttle body...
Page 531: ...Manifold Absolute Pressure MAP Sensor 8 0L On right upper side of intake manifold...
Page 533: ...Throttle Position TP Sensor 3 9L On throttle body...
Page 534: ...Throttle Position TP Sensor 5 2L On throttle body...
Page 535: ...Throttle Position TP Sensor 5 9L On throttle body...
Page 537: ...Water In Fuel Sensor Diesel At bottom of fuel filter water separator canister...
Page 541: ...Intake Air Heater Diesel Attached to metal block on top of intake manifold...
Page 625: ...Fig 13 Belt Routing 5 9L Diesel Ram Pickup Courtesy of Chrysler Corp...
Page 626: ...Fig 14 Belt Routing 5 9L 8 0L Gasoline Ram Pickup With Air Pump Courtesy of Chrysler Corp...
Page 651: ...Fig 15 Oil Pan Alignment Dowel Fabrication Installation Courtesy of Chrysler Corp OVERHAUL...
Page 830: ...Fig 5 Identifying Heater Assembly Components Ram Pickup Courtesy of Chrysler Corp...
Page 839: ...Fig 11 Heater System Vacuum Circuits Dakota Courtesy of Chrysler Corp...
Page 840: ...Fig 12 Heater System Vacuum Circuits Durango Courtesy of Chrysler Corp...
Page 841: ...Fig 13 Heater System Vacuum Circuits Ram Pickup Courtesy of Chrysler Corp...
Page 842: ...Fig 14 Heater System Vacuum Circuits Ram Van Wagon Courtesy of Chrysler Corp WIRING DIAGRAMS...
Page 843: ...Fig 15 Heater System Wiring Diagram Dakota...
Page 844: ...Fig 16 Heater System Wiring Diagram Durango...
Page 845: ...Fig 17 Heater System Wiring Diagram Ram Pickup...
Page 846: ...Fig 18 Heater System Wiring Diagram Ram Van Wagon...
Page 867: ...WIRING DIAGRAMS Fig 9 Analog Instrument Panel Wiring Diagram Ram Pickup 1 Of 2...
Page 868: ...Fig 10 Analog Instrument Panel Wiring Diagram Ram Pickup 2 Of 2...
Page 869: ...Fig 11 Analog Instrument Panel Wiring Diagram Ram Van Ram Wagon...
Page 882: ...Fig 12 CNG Fuel Rail Service Points Courtesy of Chrysler Corp...
Page 883: ...Fig 13 CNG Fuel Tank Components Courtesy of Chrysler Corp...
Page 884: ...Fig 14 Manual Shutoff Valve Location Courtesy of Chrysler Corp...
Page 897: ...Fig 19 Interior Fuse Panel Courtesy of Chrysler Corp Fuse Circuit Breaker Identification...
Page 912: ...WIRING DIAGRAMS Fig 5 Power Mirror System Wiring Diagram Caravan Town Country Voyager...
Page 913: ...Fig 6 Power Mirror System Wiring Diagram Dakota...
Page 914: ...Fig 7 Power Mirror System Wiring Diagram Durango...
Page 915: ...Fig 8 Power Mirror System Wiring Diagram Ram Pickup...
Page 916: ...Fig 9 Power Mirror System Wiring Diagram Ram Van Ram Wagon...
Page 921: ...Fig 3 Quad Driver Test General Motors Courtesy of General Motors Corp...
Page 1194: ...Fig 2 Firing Order Distributor Rotation 2 5L 4 Cyl Dakota...
Page 1196: ...Fig 5 Firing Order Distributor Rotation 3 9L V6 Dakota Durango Ram Pickup Ram Van Ram Wagon...
Page 1207: ...Fig 3 Power Seat System Wiring Diagram Ram Pickup...
Page 1208: ...Fig 4 Power Seat System Wiring Diagram Ram Van Ram Wagon...
Page 1218: ...Fig 3 Starting System Wiring Diagram Breeze Cirrus Stratus...
Page 1219: ...Fig 4 Starting System Wiring Diagram Caravan Town Country Voyager...
Page 1220: ...Fig 5 Starting System Wiring Diagram Concorde Intrepid LHS 300M...
Page 1221: ...Fig 6 Starting System Wiring Diagram Dakota...
Page 1222: ...Fig 7 Starting System Wiring Diagram Durango...
Page 1223: ...Fig 8 Starting System Wiring Diagram Neon...
Page 1224: ...Fig 9 Starting System Wiring Diagram Ram Pickup...
Page 1225: ...Fig 10 Starting System Wiring Diagram Ram Van Ram Wagon...
Page 1226: ...Fig 11 Starting System Wiring Diagram Sebring Convertible...
Page 1242: ...Fig 10 Horn System Wiring Diagram Durango...
Page 1243: ...Fig 11 Horn System Wiring Diagram Ram Pickup...
Page 1315: ...Fig 2 Removing Front Shock Absorber Assembly Courtesy of Chrysler Corp STABILIZER BAR...
Page 1371: ...customer whenever possible Fig 2 Symptom Check List Page 1...
Page 1372: ...Fig 3 Symptom Check List Page 2...
Page 1373: ...Fig 4 Symptom Check List Page 3...
Page 1375: ...Fig 6 Engine Driveability Automatic Transmission...
Page 1376: ...Fig 7 Brakes Steering Suspension Fig 8 Air Conditioning Heater Ventilation...
Page 1377: ...Fig 9 Electrical Radio Tape CD Player...
Page 1378: ...Fig 10 Manual Transmission Clutch...
Page 1379: ...Fig 11 Squeak Rattle Noise Conditions Fig 12 Water Leak Wind Noise...
Page 1398: ...Manual A C Circuit ANTI LOCK BRAKES...
Page 1399: ...Anti lock Brake Circuits ANTI THEFT...
Page 1400: ...Anti theft Circuit BODY COMPUTER...
Page 1401: ...Central Timer Module Circuit...
Page 1402: ...Integrated Central Electronics Module Circuit COMPUTER DATA LINES...
Page 1403: ...Computer Data Lines CRUISE CONTROL...
Page 1404: ...Cruise Control Circuit ENGINE PERFORMANCE...
Page 1405: ...3 9L 3 9L Engine Performance Circuits 1 of 3...
Page 1406: ...3 9L Engine Performance Circuits 2 of 3...
Page 1407: ...3 9L Engine Performance Circuits 3 of 3 5 2L...
Page 1408: ...5 2L Engine Performance Circuits 1 of 3...
Page 1409: ...5 2L Engine Performance Circuits 2 of 3...
Page 1410: ...5 2L Engine Performance Circuits 3 of 3 5 9L...
Page 1411: ...5 9L Engine Performance Circuits 1 of 3...
Page 1412: ...5 9L Engine Performance Circuits 2 of 3...
Page 1413: ...5 9L Engine Performance Circuits 3 of 3 EXTERIOR LIGHTS...
Page 1414: ...Back up Lamps Circuit...
Page 1415: ...Exterior Lamps Trailer connector Circuit 1 of 2...
Page 1416: ...Exterior Lamps Trailer connector Circuit 2 of 2 GROUND DISTRIBUTION...
Page 1417: ...Ground Distribution Circuit 1 of 3...
Page 1418: ...Ground Distribution Circuit 2 of 3...
Page 1419: ...Ground Distribution Circuit 3 of 3 HEADLIGHTS...
Page 1420: ...Headlight Circuit W DRL W Quad Headlights...
Page 1421: ...Headlight Circuit W DRL W O Quad Headlights...
Page 1422: ...Headlight Circuit W O DRL W Quad Headlights...
Page 1423: ...Headlight Circuit W O DRL W O Quad Headlights HORN...
Page 1424: ...Horn Circuit INSTRUMENT CLUSTER...
Page 1425: ...Instrument Cluster Circuit 1 of 2...
Page 1426: ...Instrument Cluster Circuit 2 of 2...
Page 1427: ...Overhead Console Circuit INTERIOR LIGHTS...
Page 1428: ...Courtesy Lamps Circuit...
Page 1429: ...Instrument Illumination Circuit PASSIVE RESTRAINTS...
Page 1430: ...Passive Restraint Circuit POWER DISTRIBUTION...
Page 1431: ...Power Distribution Circuit 1 of 3...
Page 1432: ...Power Distribution Circuit 2 of 3...
Page 1433: ...Power Distribution Circuit 3 of 3 POWER DOOR LOCKS...
Page 1434: ...Power Door Lock Circuit W Keyless Entry...
Page 1435: ...Power Door Lock Circuit W O Keyless Entry POWER MIRRORS...
Page 1436: ...Power Mirror Circuit POWER SEATS...
Page 1437: ...Power Seat Circuits POWER WINDOWS...
Page 1438: ...Power Window Circuit RADIO...
Page 1439: ...Radio Circuits Premium Radio...
Page 1440: ...Radio Circuits Standard STARTING CHARGING...
Page 1441: ...Charging Circuit...
Page 1442: ...Starting Circuit SUPPLEMENTAL RESTRAINTS...
Page 1443: ...Supplemental Restraint Circuit TRANSMISSION...
Page 1444: ...3 9L 3 9L A T Circuit 1 of 2...
Page 1445: ...3 9L A T Circuit 2 of 2 5 2L...
Page 1446: ...5 2L A T Circuit 1 of 2...
Page 1447: ...5 2L A T Circuit 2 of 2 5 9L...
Page 1448: ...5 9L A T Circuit 1 of 2...
Page 1449: ...5 9L A T Circuit 2 of 2 WARNING SYSTEMS...
Page 1450: ...Warning System Circuits WIPER WASHER...
Page 1451: ...Wiper Washer Circuit...
Page 1525: ...Fig 26 Vacuum Hose Diagram Ram Van Ram Wagon 5 9L Except Calif Courtesy of Chrysler Corp...
Page 1559: ...Fig 18 Injector Bank Known Good Voltage Pattern...
Page 1564: ...Fig 23 Injector Bank Known Good Voltage Pattern...
Page 1568: ...Fig 27 Single Injector Known Good Voltage Pattern...
Page 1569: ...Fig 28 Single Injector Known Good Voltage Pattern...
Page 1606: ...Fig 11 Power Window System Wiring Diagram Caravan Town Country Voyager...
Page 1607: ...Fig 12 Power Window System Wiring Diagram Dakota...
Page 1608: ...Fig 13 Power Window System Wiring Diagram Durango...
Page 1609: ...Fig 14 Power Window System Wiring Diagram Ram Pickup...
Page 1610: ...Fig 15 Power Window System Wiring Diagram Ram Van Ram Wagon...
Page 1619: ...Fig 5 Wiper Washer System Wiring Diagram Ram Pickup...
Page 1621: ...Fig 2 PCM Wiring Diagram Avenger Sebring Coupe 2 0L 2 Of 3...
Page 1622: ...Fig 3 PCM Wiring Diagram Avenger Sebring Coupe 2 0L 3 Of 3...
Page 1623: ...Fig 4 PCM Wiring Diagram Avenger Sebring Coupe 2 5L 1 Of 3...
Page 1624: ...Fig 5 PCM Wiring Diagram Avenger Sebring Coupe 2 5L 2 Of 3...
Page 1625: ...Fig 6 PCM Wiring Diagram Avenger Sebring Coupe 2 5L 3 Of 3 BREEZE STRATUS...
Page 1626: ...Fig 7 PCM Wiring Diagram Breeze Stratus 2 0L 2 4L 1 Of 3...
Page 1627: ...Fig 8 PCM Wiring Diagram Breeze Stratus 2 0L 2 4L 2 Of 3...
Page 1628: ...Fig 9 PCM Wiring Diagram Breeze Stratus 2 0L 2 4L 3 Of 3 CARAVAN TOWN COUNTRY VOYAGER...
Page 1629: ...Fig 10 PCM Wiring Diagram Caravan Voyager 2 4L 1 Of 3...
Page 1630: ...Fig 11 PCM Wiring Diagram Caravan Voyager 2 4L 2 Of 3...
Page 1631: ...Fig 12 PCM Wiring Diagram Caravan Voyager 2 4L 3 Of 3...
Page 1632: ...Fig 13 PCM Wiring Diagram Caravan Voyager 3 0L 1 Of 3...
Page 1633: ...Fig 14 PCM Wiring Diagram Caravan Voyager 3 0L 2 Of 3...
Page 1634: ...Fig 15 PCM Wiring Diagram Caravan Voyager 3 0L 3 Of 3...
Page 1635: ...Fig 16 PCM Wiring Diagram Caravan Town Country Voyager 3 3L 3 3L Flex Fuel 3 8L 1 Of 3...
Page 1636: ...Fig 17 PCM Wiring Diagram Caravan Town Country Voyager 3 3L 3 3L Flex Fuel 3 8L 2 Of 3...
Page 1638: ...Fig 19 PCM Wiring Diagram Cirrus Stratus 2 5L 1 Of 3...
Page 1639: ...Fig 20 PCM Wiring Diagram Cirrus Stratus 2 5L 2 Of 3...
Page 1640: ...Fig 21 PCM Wiring Diagram Cirrus Stratus 2 5L 3 Of 3 CONCORDE INTREPID LHS 300M...
Page 1641: ...Fig 22 PCM Wiring Diagram Concorde Intrepid 2 7L 1 Of 3...
Page 1642: ...Fig 23 PCM Wiring Diagram Concorde Intrepid 2 7L 2 Of 3...
Page 1643: ...Fig 24 PCM Wiring Diagram Concorde Intrepid 2 7L 3 Of 3...
Page 1644: ...Fig 25 PCM Wiring Diagram Concorde Intrepid 3 2L LHS 300M 3 5L 1 Of 3...
Page 1645: ...Fig 26 PCM Wiring Diagram Concorde Intrepid 3 2L LHS 300M 3 5L 2 Of 3...
Page 1646: ...Fig 27 PCM Wiring Diagram Concorde Intrepid 3 2L LHS 300M 3 5L 3 Of 3 DAKOTA...
Page 1647: ...Fig 28 PCM Wiring Diagram Dakota 2 5L 1 Of 3...
Page 1648: ...Fig 29 PCM Wiring Diagram Dakota 2 5L 2 Of 3...
Page 1649: ...Fig 30 PCM Wiring Diagram Dakota 2 5L 3 Of 3...
Page 1650: ...Fig 31 PCM Wiring Diagram Dakota 3 9L 5 2L 1 Of 3...
Page 1651: ...Fig 32 PCM Wiring Diagram Dakota 3 9L 5 2L 2 Of 3...
Page 1652: ...Fig 33 PCM Wiring Diagram Dakota 3 9L 5 2L 3 Of 3...
Page 1653: ...Fig 34 PCM Wiring Diagram Dakota 5 9L 1 Of 3...
Page 1654: ...Fig 35 PCM Wiring Diagram Dakota 5 9L 2 Of 3...
Page 1655: ...Fig 36 PCM Wiring Diagram Dakota 5 9L 3 Of 3 DURANGO...
Page 1656: ...Fig 37 PCM Wiring Diagram Durango 3 9L 5 2L 5 9L 1 Of 3...
Page 1657: ...Fig 38 PCM Wiring Diagram Durango 3 9L 5 2L 5 9L 2 Of 3...
Page 1658: ...Fig 39 PCM Wiring Diagram Durango 3 9L 5 2L 5 9L 3 Of 3 NEON...
Page 1659: ...Fig 40 PCM Wiring Diagram Neon 2 0L 1 Of 3...
Page 1660: ...Fig 41 PCM Wiring Diagram Neon 2 0L 2 Of 3...
Page 1661: ...Fig 42 PCM Wiring Diagram Neon 2 0L 3 Of 3 RAM PICKUP...
Page 1662: ...Fig 43 PCM Wiring Diagram Ram Pickup 3 9L 5 2L 5 9L 1 Of 3...
Page 1663: ...Fig 44 PCM Wiring Diagram Ram Pickup 3 9L 5 2L 5 9L 2 Of 3...
Page 1664: ...Fig 45 PCM Wiring Diagram Ram Pickup 3 9L 5 2L 5 9L 3 Of 3...
Page 1665: ...Fig 46 PCM Wiring Diagram Ram Pickup 2500 3500 8 0L 1 Of 3...
Page 1666: ...Fig 47 PCM Wiring Diagram Ram Pickup 2500 3500 8 0L 2 Of 3...
Page 1667: ...Fig 48 PCM Wiring Diagram Ram Pickup 2500 3500 8 0L 3 Of 3...
Page 1668: ...Fig 49 PCM Wiring Diagram Ram Pickup 2500 3500 5 9L 24 Valve Diesel 1 Of 3...
Page 1669: ...Fig 50 PCM Wiring Diagram Ram Pickup 2500 3500 5 9L 24 Valve Diesel 2 Of 3...
Page 1670: ...Fig 51 PCM Wiring Diagram Ram Pickup 2500 3500 5 9L 24 Valve Diesel 3 Of 3 RAM VAN RAM WAGON...
Page 1671: ...Fig 52 PCM Wiring Diagram Ram Van Ram Wagon 1500 3 9L 1 Of 3...
Page 1672: ...Fig 53 PCM Wiring Diagram Ram Van Ram Wagon 1500 3 9L 2 Of 3...
Page 1673: ...Fig 54 PCM Wiring Diagram Ram Van Ram Wagon 1500 3 9L 3 Of 3...
Page 1674: ...Fig 55 PCM Wiring Diagram Ram Van Ram Wagon 5 2L Gasoline 5 9L 1 Of 3...
Page 1675: ...Fig 56 PCM Wiring Diagram Ram Van Ram Wagon 5 2L Gasoline 5 9L 2 Of 3...
Page 1676: ...Fig 57 PCM Wiring Diagram Ram Van Ram Wagon 5 2L Gasoline 5 9L 3 Of 3...
Page 1677: ...Fig 58 PCM Wiring Diagram Ram Van Ram Wagon 5 2L CNG 1 Of 3...
Page 1678: ...Fig 59 PCM Wiring Diagram Ram Van Ram Wagon 5 2L CNG 2 Of 3...
Page 1679: ...Fig 60 PCM Wiring Diagram Ram Van Ram Wagon 5 2L CNG 3 Of 3 SEBRING CONVERTIBLE...
Page 1680: ...Fig 61 PCM Wiring Diagram Sebring Convertible 2 4L 1 Of 4...
Page 1681: ...Fig 62 PCM Wiring Diagram Sebring Convertible 2 4L 2 Of 4...
Page 1682: ...Fig 63 PCM Wiring Diagram Sebring Convertible 2 4L 3 Of 4...
Page 1683: ...Fig 64 PCM Wiring Diagram Sebring Convertible 2 4L 4 Of 4...
Page 1684: ...Fig 65 PCM Wiring Diagram Sebring Convertible 2 5L 1 Of 4...
Page 1685: ...Fig 66 PCM Wiring Diagram Sebring Convertible 2 5L 2 Of 4...
Page 1686: ...Fig 67 PCM Wiring Diagram Sebring Convertible 2 5L 3 Of 4...
Page 1687: ...Fig 68 PCM Wiring Diagram Sebring Convertible 2 5L 4 Of 4...
Page 1688: ......
Page 1689: ......
Page 1690: ......
Page 1691: ......