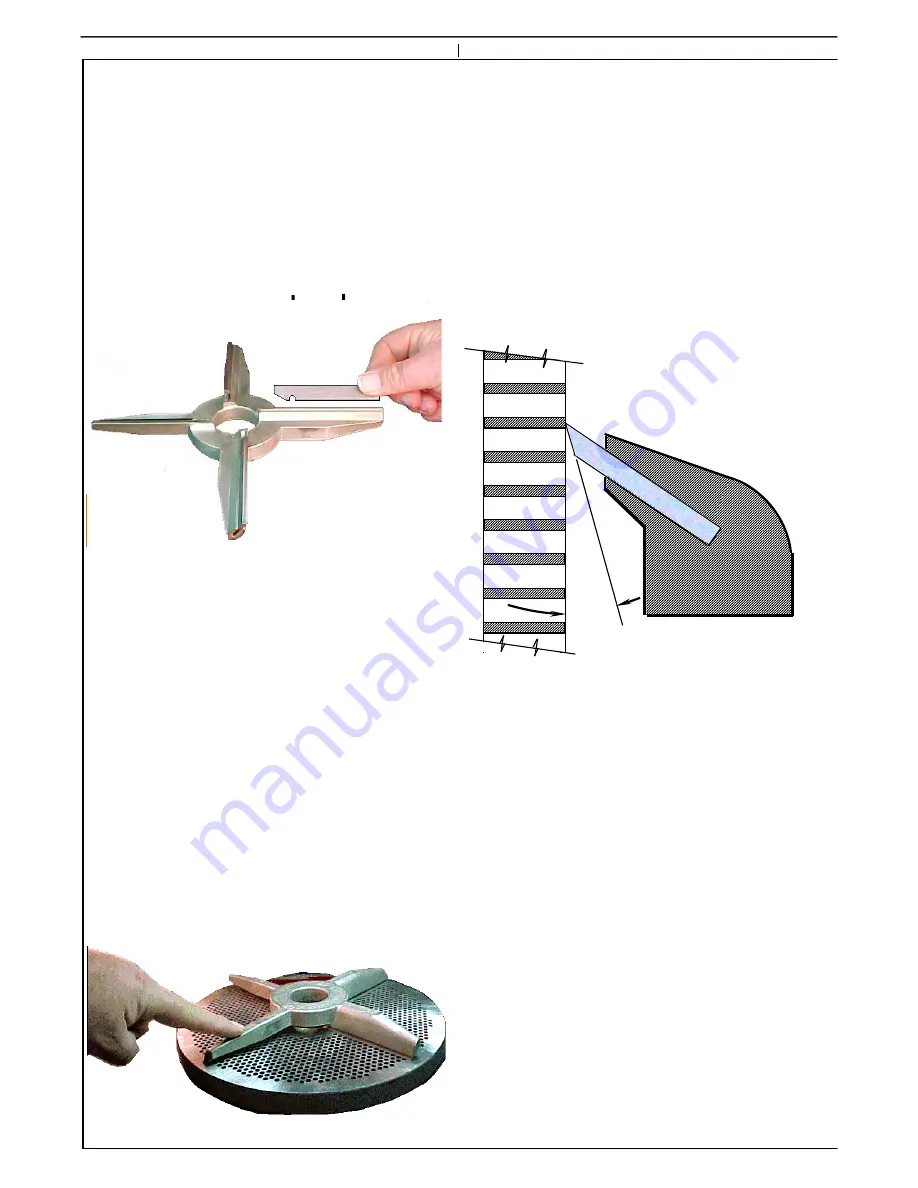
12.5°
Line the notch of the insert up with the pin in
the bottom of the slot of the knifeholder. If
necessary tap the insert into position with a
soft mallet, a soft rubber hammer, or a piece
of pine. The inserts should fit snugly in the
slots, but they should not have to be beat in.
It may be necessary to open the slots slightly
if they are too tight. Use a small flat file, or a
cut-off wheel. Tap on the face of the
knifeholder if they are too loose.
The combination of the insert slot angle and
the angle that the inserts are ground provide
that only the leading edge of the knife insert
contacts the plate. This slight amount of
clearance allows the insert to seat within a
few revolutions of the grinder being turned
on. The amount of material removed from
the leading edge of the insert is not
measurable, but it is advised that the first
product that comes out of any meat grinder
on start up is discarded.
TAP HERE IF
LOOSE
.
When the inserts have been properly
installed turn the knifeholder over and check
it for flatness. Use a properly sharpened
plate, or other known "true flat" surface. If
the knifeholder rocks, check to make sure all
the blades have been properly seated. Check
the bottom of the slots for obstructions.
Make sure that the slot of the insert is lined
up with the pin in the bottom of the slot.
A slight rock is permissible, a feeler gauge of
.005 should not fit under the knife insert that
is not touching the plate.
If inserts are not properly installed,
excessive clearance will result.
Excessive clearance will keep the grinder unit
from functioning properly, and in many cases
it will not grind.
We recommend that maintenance, or a
responsible person is entrusted with the
function of changing inserts and sharpening
the grinder plates. The success of your
operation depends on it.
If you do not have the equipment to sharpen
your plates, or you do not know if they are
being sharpened properly, send them to Dixie
Grinders Inc. (attention Service Department)
and we will examine your plate, sharpen it
properly, and return it to you promptly.
24