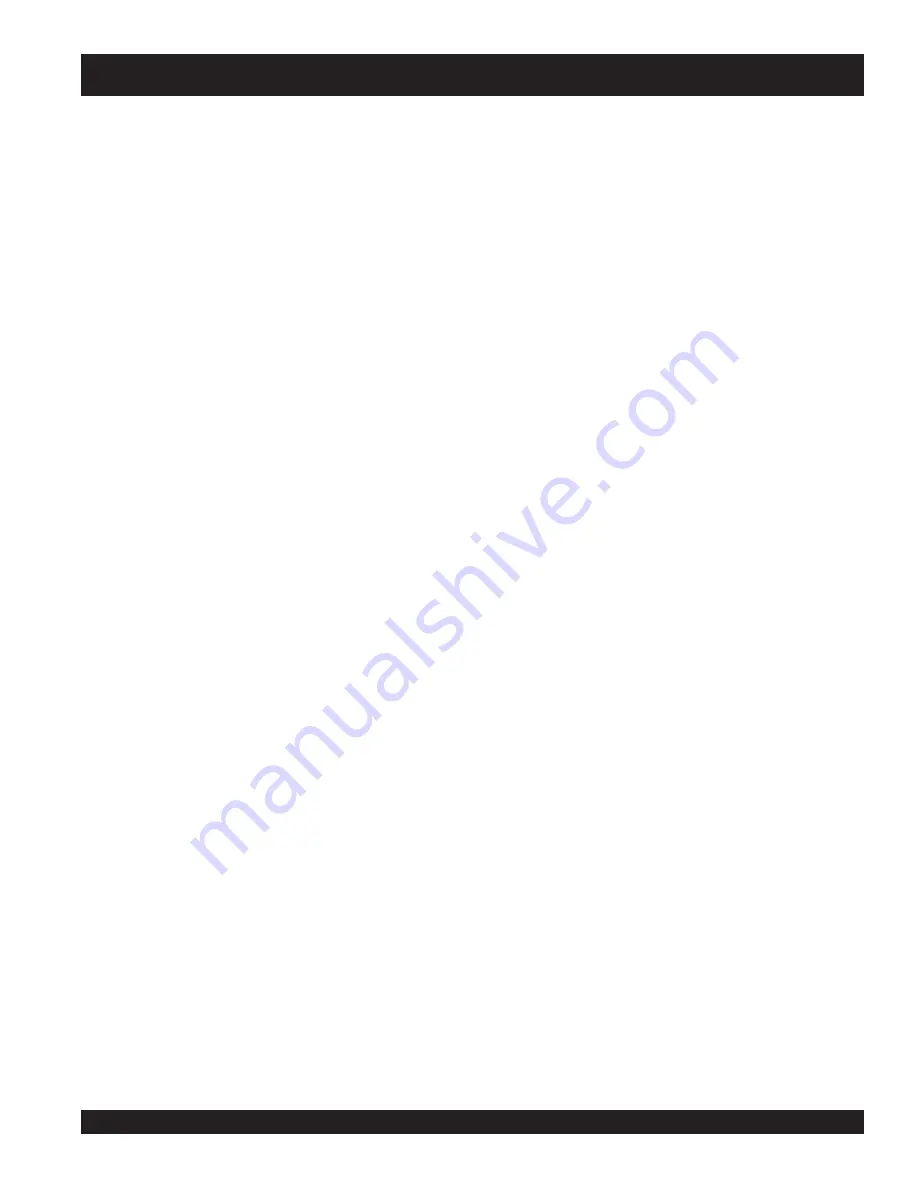
ST-70 — PARTS & OPERATION MANUAL — REV. #4 (05/29/07) — PAGE 29
Chip the blockage out with the pry-bar.
Flush the shuttle tube with water.
Replace and seal the inspection cover plate on the shuttle
tube.
7.5 Resume pumping.
8. The effects of heat and excessive time on concrete:
Hot concrete, commonly referred to as a “hot load”, is
concrete that has been in a redi-mix truck in excess of 2 to
3 hours. On a hot day, the amount of time is even less. A
brief explanation of why heat and time affect concrete:
Concrete starts setting or drying up through a chemical
reaction. The catalyst to this reaction is heat. When pumping
a hot load, it is important to remember that when you have
to stop pumping for any reason, add water to the concrete in
the hopper and remix (see Page 27, Section 19). Move
concrete in the hose every 5 minutes. If shutdown time
becomes too long, wash out immediately (see Page 24).
9. ADMIXTURES: Admixtures are designed into the concrete
mix by the redi-mix company or an architectural engineering
company. This section lists common admixtures and a brief
explanation of their function.
9.1 POZZOLITH 300 R or the equivalent. – Acts as a water
retarder and a lubricant. On a lean mix, long pushes stiff
mixes and vertical pushes, Pozzolith 300 R helps
pumpability.
9.2 MBVR – Air entraining, acts as a lubricant.
9.3 CALCIUM CHLORIDE – Commonly referred to as C.C. , is
used as an accelerator. When pumping a load with calcium
chloride, it is recommended that you wash out if the waiting
time between delivery trucks becomes too long.
9.4 SUPER PLASTICIZERS – Acts as an accelerator. The
concrete will look very wet after the super plasticizer is
added, but will begin to set up very fast. Wash out
immediately if you do not have a truck waiting. Super
plasticizers are used mainly on commercial jobs.
9.5 RED LABEL – Acts as water retarder and an accelerator.
Red label also will mainly be used on commercial jobs.
9.6 FLY ASH – Is used to help increase the strength of the
concrete and decrease the cement content per yard. This is
one of the most common admixtures used.
NOTE: All admixtures will be shown on the redi-mix concrete
ticket. It is suggested before starting the pumping job you ask
the driver of the redi-mix truck to see the concrete ticket and
note the admixtures that exist and take the proper action.
ST-70 — OPERATING PROCEDURES
10. If the volume at end of hose starts to decrease gradually
and eventually almost stops, it is quite likely that the wear
ring and/or wear plate have to be replaced due to
excessive wear allowing the concrete to be discharged
back into the hopper under pressure. This is a major reason
for plugging in the shuttle tube.
11. Slight pulsation of the hose will always be noticeable near
the pump. Excessive pulsation of the hose near the pump
is normally due to higher than average line pressures
caused by stiff, harsh mixes or extremely long pumping
distances. The use of larger I.D. hose than specified on
page 3-8, para. 17 in these extreme cases reduces line
pressures or the addition of slight amounts of water to the
mix, if permissible, will permit easier pumping. The use of
certain pumping admixtures may help. If excessive
pulsation exists, it is advisable to use burlap or some
means of protection under the hose at points where the
hose may wear through the outer cover; e.g., over forms
or steel or sharp curbs.
12. It is the responsibility of the pump operator to ensure that
the delivery system hose and line system, with all clamps
and accessories have a higher pressure rating than the
concrete pump can generate. The model ST-70 generates
875 p.s.i.
13. Before starting the pumping operation, the following check
list procedure should be followed:
13.1 Check engine oil.
13.2 Check oil reservoir to make sure that it is full.
13.3 Start and run the engine a minimum of five minutes
before starting the pumping operation.
13.4 Cycle the pump at 6 strokes/minute maximum and
warm oil to 50 degrees Fahrenheit.
NOTE: When the redi-mix truck arrives, it is always a good idea
to check the concrete ticket and make sure you have the proper
mix design. When adding water to the mix, be sure not to get the
concrete too wet. In other words, if you think the load of concrete
needs 40 gallons, put in 20 gallons. You can always add more
water to the load but you cannot extract the water from the load.
Go to Discount-Equipment.com
to order your parts