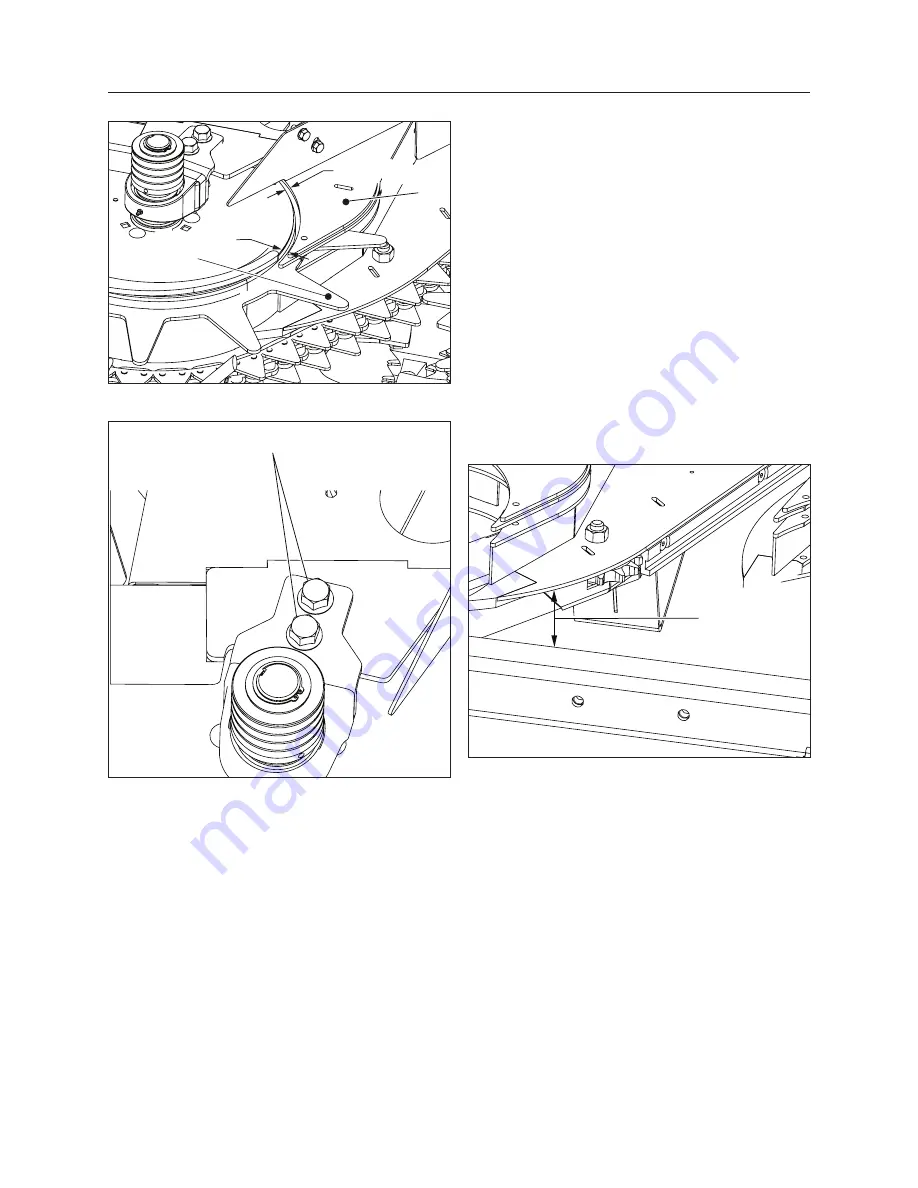
34
F6715E968
ADJUSTMENTS - MAINTENANCE
1/8" (3 mm)
1/4" (6 mm)
4
5
Figure 49 Drum adjustment
6
Figure 50 Drum support bearing bolts
SCRAPER ADJUSTMENT - FIGURE 51
It may be necessary to adjust the scrapers after they
have been moved or replaced.
1. Remove the drums.
2.
Loosen the scraper bolts.
3. Align the chain channel ridge with the frame
ridge (figure 51).
4.
Position the scraper to obtain 6” (152 mm) be
-
tween the cross beam and the bottom of the
scraper’s lower plate (figure 51).
5. The holes in the frame allow for a minor scraper
adjustment.
6. Tighten all bolts back then check alignment and
position.
7. Reinstall the drums by following the drum
adjustment instructions.
6" (152 mm)
Figure 51 Scraper adjustment