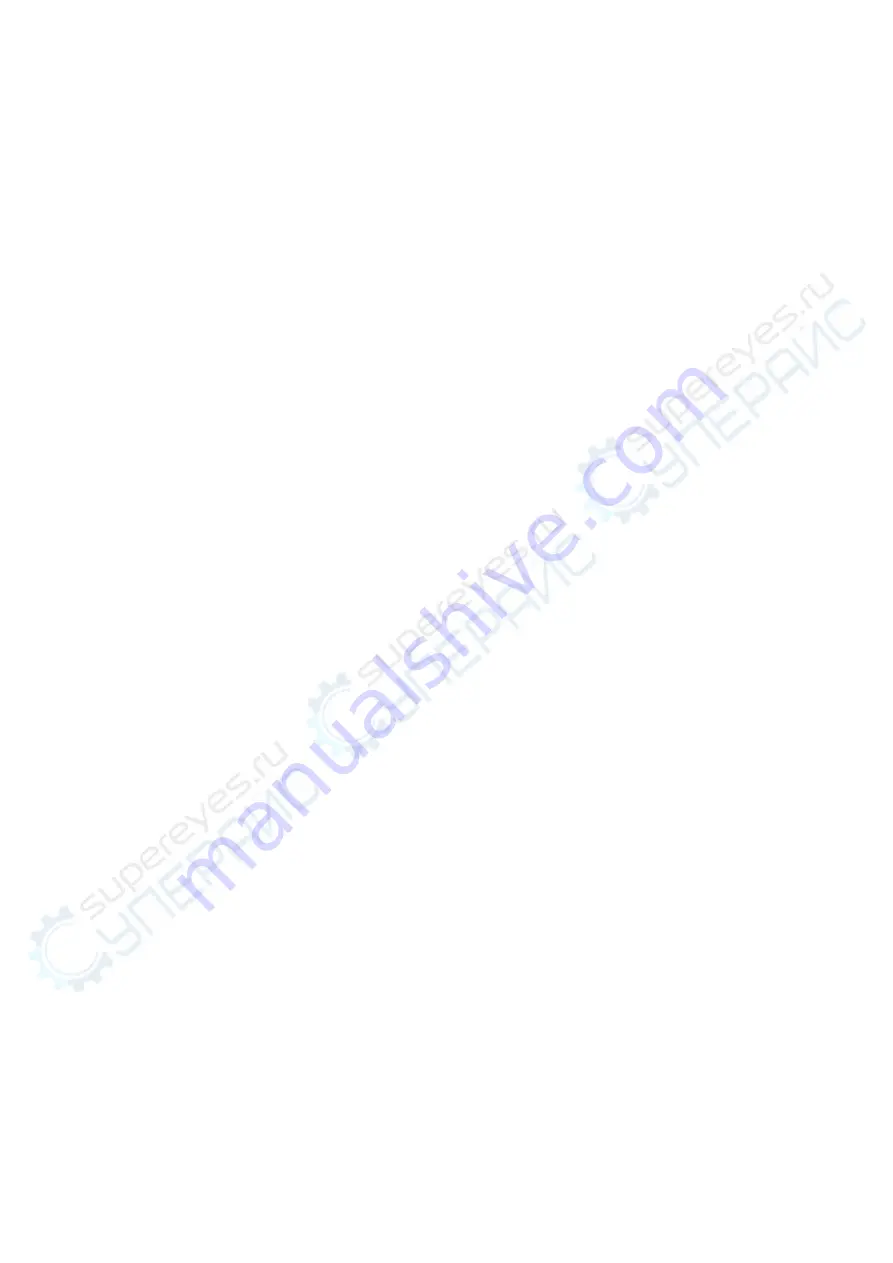
7
五
、
Operations:
1
、
Preheat
Preheat the PCB board and BGA chip, and the temperature of constant temperature oven is set at
80
℃
-100
℃
, for 4-8 hours to remove internal moisture of the PCB and BGA, to prevent the
burst phenomenon when heating.
2
、
Remove
Place the PCB board into the bracket on the repair station,and select the appropriate hot air reflow
nozzle,and set the appropriate soldering curve,press the open button until it finishes,and then
move the hot air manually,to suck the BGA chip away with the vacuum suction pen.
3
、
Clean-up welding
The BGA pad clean-up , one with de-soldering line to drag flat, the second with iron; Best to
remove the tin a short time after the BGA removed , then BGA has not completely cooled , and the
temperature difference make less damage to the pad;use the flux can improve the activity of
soldering tin,better to clean the soldering tin. Particular attention not to damage the PCB pad,and
in order to ensure the reliability of BGA solder, when the cleaning pad to make use of some of the
solder paste residues with more volatile solvents , such as plate washer water, industrial alcohol.
4
、
BGA re-balling
Wipe the paste flux equably with the brush pen on the BGA pad, choose the right steel mesh, and
then plant tin beads by the re-balling kit on the right pad.
5
、
BGA tin beads welding
Heat the bottom heating zone of BGA re-balling station and then weld the tin beads on the pad.
6
、
Besmear flux
Wipe the paste flux with the brush pen on the PCB pad. If you wipe so much, it will cause
connected welding, on the contrary, it will cause null welding. In order to wipe off dust and
impurity of tin balls, and enhance welding effect, the welding paste must be wiped equally.
7
、
Place the BGA chip
Place the BGA chip on the PCB board with manual alignment and silk-screen borders, meanwhile
the tension of the solder joint when melt will have a good self- alignment effect.
8
、
Weld
First, put the PCB board which is pasted with BGA chip on the positioning stand, and then move
the hot wind head to the working place. Second, choose the appropriate backflow nozzle and set
right welding temperature curve, start heating, open the switch, and then run the welding process.
Besides, after the welding process is finished, you have to cool the BGA by the cooling fan. Hoist
the upper hot wind head and make the bottom of hot wind nozzle apart from the surface of BGA
3-5mm, and stay 30-40 seconds, or, you can move the hot wind head after the starting switch is
put out, withdraw the hot wind head.Finally, take away the PCB board from the heating zones.
(1)
null welding
:
Because of counterpoint by hand will cause deviation between chip and welding plate, surface
tension of tin ball will make BGA chip and welding plate in the process of automatic correction.
Once heating, BGA falls not evenly, which cause the chip drops not evenly.If stop reflowing at
this time, the chip will not fall normally,which will cause the phenomenon of empty welding and
false welding.So you need to extent time of third
、
forth temperature zones or add the bottom
pre-heating temperature to make ,the tin balls meltdown and drop evenly.