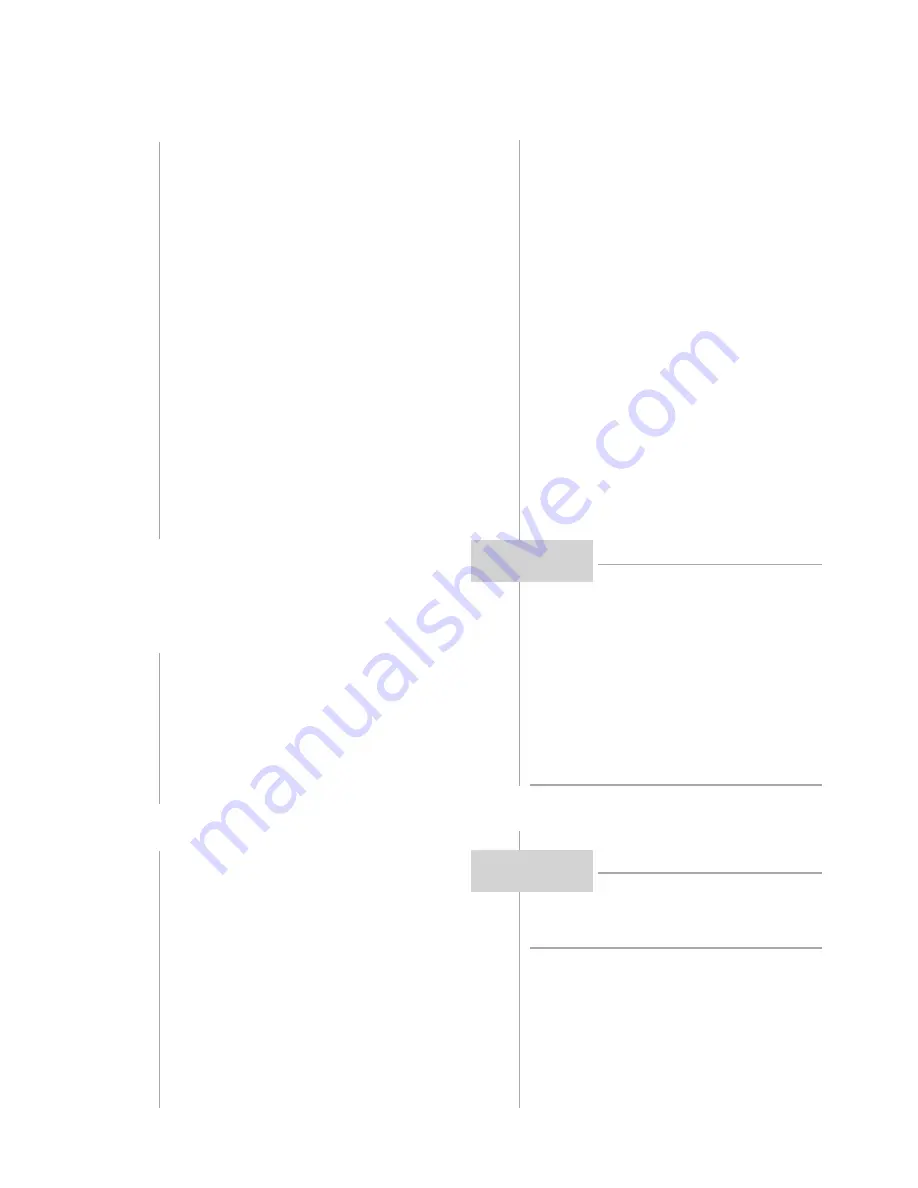
8
9
COMMISSIONING
CARE/CLEANING
consumption. To correctly set the overflow valve, the
following procedure is recommended:
a) Open all heating circuits and close the overflow
valve. Determine the resulting temperature
difference between supply and return flow.
b) Close all of the heating circuits that may also be
closed during operation (depending on the type
of heat pump usage) so that the most unfa-
vourable operating state - with respect to the water
flow rate - is achieved.
c) In this operating state open the overflow valve
until approximately the same temperature
difference exists that was measured under a)
when the overflow valve was closed and the
heating circuits open.
Any malfunctions occurring during operation are
displayed on the heat pump controller and can be
corrected as described in the operating manual of
the heat pump controller.
CARE/CLEANING
9.1 Care
The heat pump is maintenance-free. To prevent
malfunctions due to sediments in the heat ex-
changers, care must be taken that no impurities can
enter the heat source system and heating installa-
tion. In the event that operating malfunctions due to
contamination occur nevertheless, the system
should be cleaned as described below.
9.2 Cleaning of Heating Side
The ingress of oxygen into the heating water circuit
may result in the formation of oxidation products
(rust). It is therefore important - in particular with
respect to the piping of underfloor heating systems
- that the installation is executed in a diffusion-proof
manner.
Also residues of lubricating and sealing agents may
contaminate the heating water.
In the case of severe contamination leading to a
reduction of the performance of the condenser in
the heat pump, the system must be cleaned by a
heating technician.
CAUTION!
CAUTION!
Based on information known to date we recommend
cleaning with a 5% phosphoric acid solution or, in
the case that cleaning needs to be performed more
frequently, with a 5% formic acid.
In either case, the cleaning fluid should be at room
temperature. It is recommended that the heat
exchanger is cleaned in the direction opposite to
the normal flow direction.
To prevent acidic cleaning agents from entering the
circuit of the heating installation we recommend that
the flushing device be fitted directly to the supply
and return lines of the condenser. To prevent any
damage caused by cleaning agent residues that
may be present in the system it is important that the
system be thoroughly flushed using appropriate
neutralising agents.
The acids must be used with great care, all relevant
regulations of the employers' liability insurance
associations must be adhered to.
If in doubt, contact the manufacturer of the chemicals!
C a u t i o n - H e a t i n g Te c h n i c i a n s !
Depending on the filling water quality and quantity,
in particular in the case of mixed installations
and plastic pipes, mineral deposits (rust sludge,
lime) may form, impairing the proper functioning
of the heating installation. A reason for this is the
water hardness and oxygen dissolved in the filling
waters as well as additional oxygen from the air,
which may penetrate via valves, fittings and
plastic pipes (oxygen diffusion). As a preventive
measure it is recommended that a physical water
conditio-ner such as ELYSATOR be used
.
9.3 Cleaning of Heat Source Side
The supplied strainer is to be install-
ed in the heat source inlet of the heat pump in
order to protect the evaporator against conta-
mination.
The filter screen of the strainer should be cleaned
one day after commissioning, thereafter every week.
If no more contamination can be noticed any more,
the strainer filter can be removed in order to reduce
pressure losses.