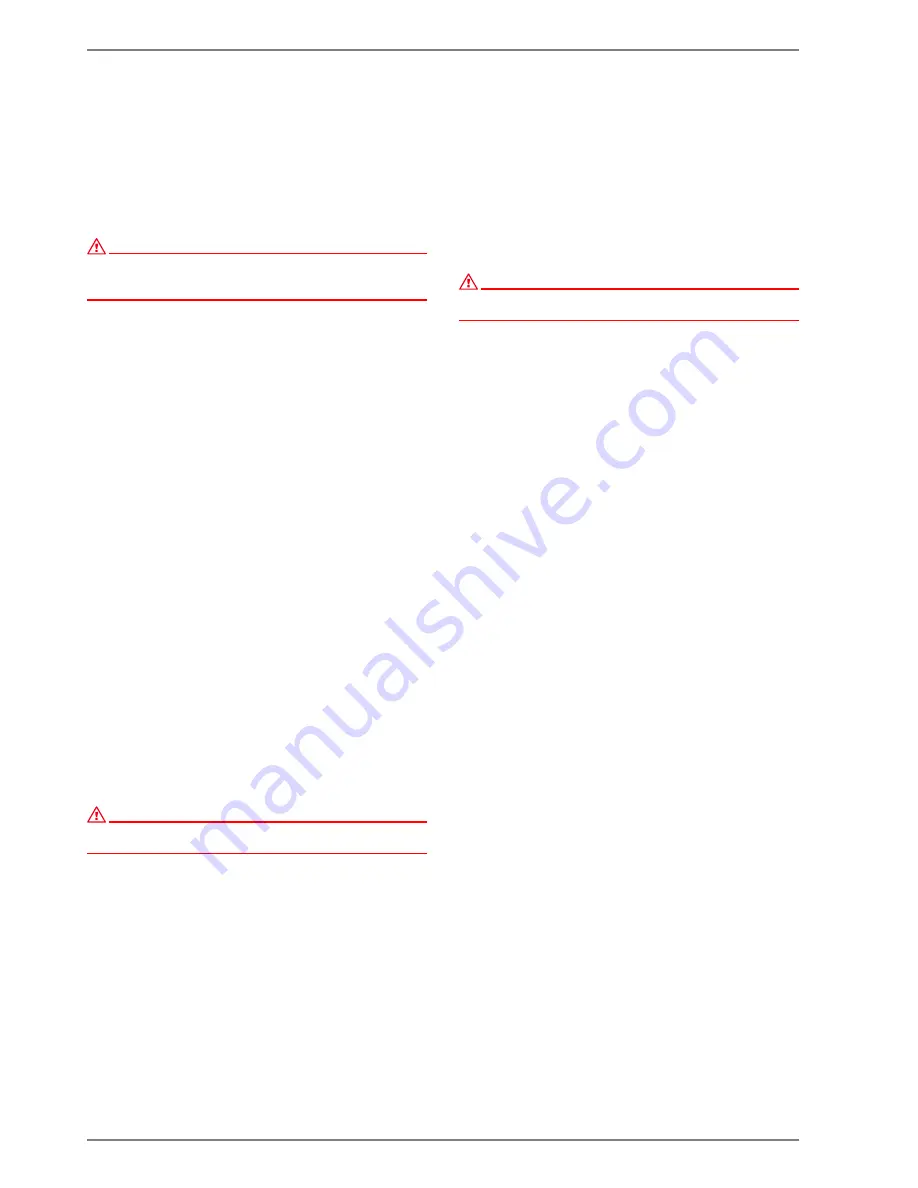
7
8.2
8.2 Cleaning the Heating System
The ingress of oxygen into the heating water circuit may result in
the formation of oxidation products (rust), particularly if steel
components are used. These products enter the heating system
via the valves, the circulating pumps and/or plastic pipes. It is
therefore essential - in particular with respect to the piping of un-
derfloor heating systems - that only diffusion-proof materials are
used.
ATTENTION!
We recommend the installation of a suitable corrosion protection system
to prevent the formation of deposits (e.g. rust) in the condenser of the
heat pump.
Residue from lubricants and sealants may also contaminate the
heating water.
In the case of severe contamination leading to a reduction in the
performance of the liquifier in the heat pump, the system must be
cleaned by a heating technician.
According to today's state of knowledge, we recommend using a
5 % phosphoric acid solution for cleaning purposes. However, if
cleaning needs to be performed more frequently, a 5 % formic
acid solution should be used.
In either case, the cleaning fluid should be at room temperature.
We recommend flushing the heat exchanger in the direction op-
posite to the normal flow direction.
To prevent acidic cleaning agents from entering the heating sys-
tem circuit, we recommend connecting the flushing device di-
rectly to the flow and return flow of the liquifier of the heat pump.
It is important that the system be thoroughly flushed using appro-
priate neutralising agents to prevent any damage from being
caused by cleaning agent residue remaining in the system.
Acids must be used with great care and all relevant regulations of
the employers' liability insurance associations must be adhered
to.
If in doubt, contact the manufacturer of the chemicals!
8.3 Cleaning the Air System
Evaporator, ventilator and condensate outflow should be cleaned
of contamination (leaves, twigs, etc.) before the heating period.
Do this by opening the front of the heat pump. The bottom should
be opened first followed by the top.
ATTENTION!
Before opening the device, ensure that all circuits are isolated from the
power supply.
Remove and rehang the side panel assemblies as described in
Chapter 4.
To prevent the evaporator and the condensate tray from being
damaged, do not use hard or sharp objects for cleaning.
Under extreme weather conditions (e.g. snow drifts), ice may
form on the air intake and exhaust air outlet grids. If this happens,
the ice must be removed in the vicinity of the air intake and ex-
haust air outlet grids to ensure that the minimum air flow rate is
maintained.
9 Faults / Trouble-
Shooting
This heat pump is a quality product and is designed for trouble-
free operation. In the event that a fault should occur, it will be in-
dicated on the heat pump manager display. Simply consult the
Faults and Trouble-shooting page in the operating instructions of
the heat pump manager.
If you cannot correct the fault yourself, please contact your after-
sales service technician.
ATTENTION!
Any work on the heat pump may only be performed by authorised and
qualified after-sales service technicians.
10 Decommissioning/
Disposal
Before removing the heat pump, disconnect it from the power
source and close all valves. Observe all environmentally-relevant
requirements regarding the recovery, recycling and disposal of
materials and components in accordance with all applicable
standards. Particular attention should be paid to the proper dis-
posal of refrigerants and refrigeration oils.