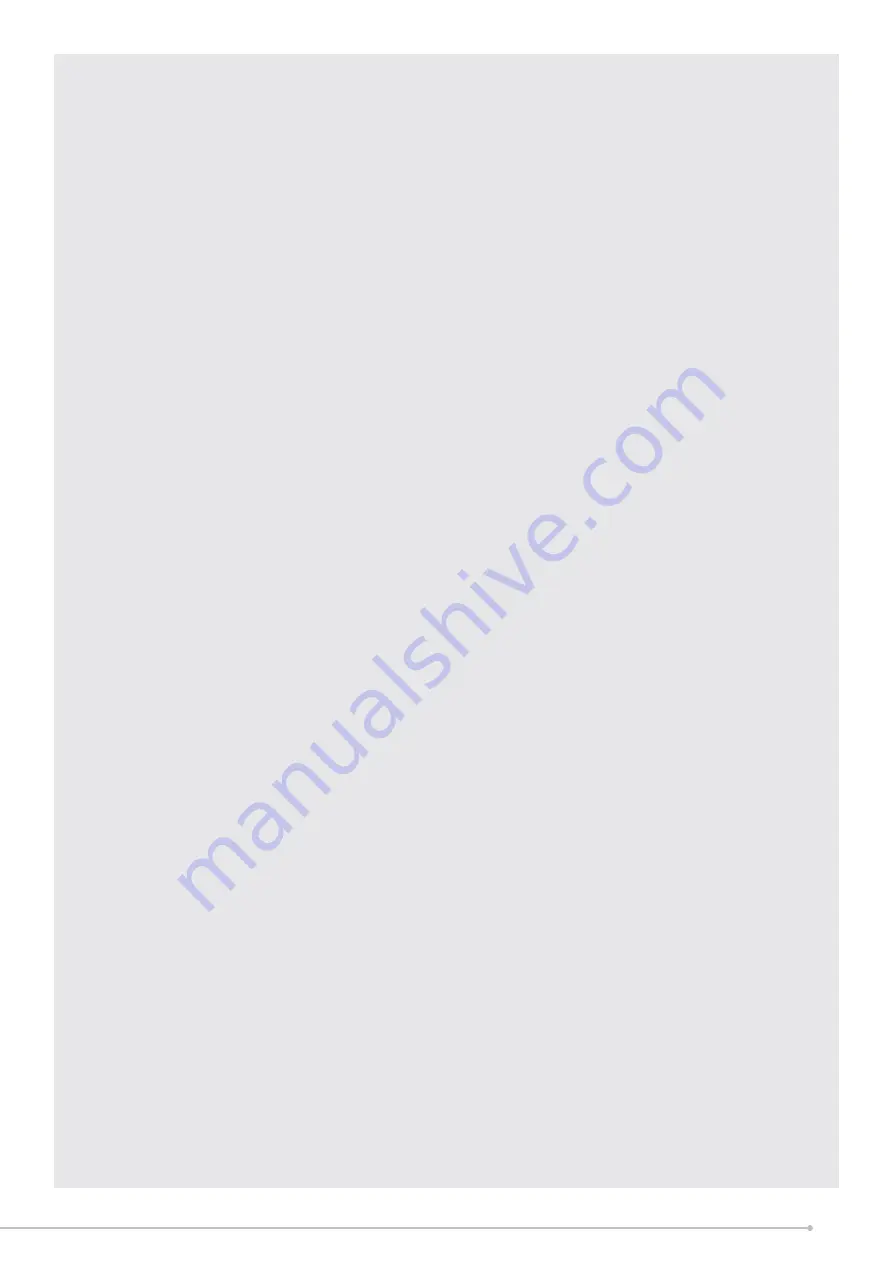
•
Cabling
Check that cabling will not be subject to wear, corrosion, excessive pressure, vibration,
sharp edges or any other adverse environmental effects. The check shall also take into
account the effects of aging or continual vibration from sources such as compressors or
fans.
•
Detection of flammable refrigerants
Under no circumstances shall potential sources of ignition be used in the searching for or
detection of refrigerant leaks. A halide torch (or any other detector using a naked flame)
shall not be used.
•
Leak detection methods
The following leak detection methods are deemed acceptable for systems containing
flammable refrigerants. Electronic leak detectors shall be used to detect flammable
refrigerants, but the sensitivity may not be adequate, or may need re-calibration.
(Detection equipment shall be calibrated in a refrigerant-free area.) Ensure that the
detector is not a potential source of ignition and is suitable for the refrigerant used. Leak
detection equipment shall be set at a percentage of the LFL of the refrigerant and shall
be calibrated to the refrigerant employed and the appropriate percentage of gas (25 %
maximum) is confirmed. Leak detection fluids are suitable for use with most refrigerants
but the use of detergents containing chlorine shall be avoided as the chlorine may react
with the refrigerant and corrode the copper pipe-work. If a leak is suspected, all naked
flames shall be removed/ extinguished. If a leakage of refrigerant is found which requires
brazing, all of the refrigerant shall be recovered from the system, or isolated (by means
of shut off valves) in a part of the system remote from the leak. Oxygen free nitrogen
(OFN) shall then be purged through the system both before and during the brazing
process.
•
Removal and evacuation
When breaking into the refrigerant circuit to make repairs or for any other purpose
conventional procedures shall be used. However, it is important that best practice is
followed since flammability is a consideration. The following procedure shall be adhered
to: Remove refrigerant; Purge the circuit with inert gas; Evacuate; Purge again with inert
gas; Open the circuit by cutting or brazing.
The refrigerant charge shall be recovered into the correct recovery cylinders. The system
shall be flushed with OFN to render the unit safe. This process may need to be repeated
several times. Compressed air or oxygen shall not be used for this task. Flushing shall be
achieved by breaking the vacuum in the system with OFN and continuing to fill until the
working pressure is achieved, then venting to atmosphere, and finally pulling down to a
vacuum. This process shall be repeated until no refrigerant is within the system. When
the final OFN charge is used, the system shall be vented down to atmospheric pressure
to enable work to take place. This operation is absolutely vital if brazing operations on
the pipe-work are to take place. Ensure that the outlet for the vacuum pump is not close
to any ignition sources and there is ventilation available.
•
Charging procedures
In addition to conventional charging procedures, the following requirements shall be
followed. Ensure that contamination of different refrigerants does not occur when using
charging equipment. Hoses or lines shall be as short as possible to minimise the amount
of refrigerant contained in them.
Cylinders shall be kept upright.
Ensure that the refrigeration system is earthed prior to charging the system with
refrigerant.
Label the system when charging is complete (if not already).
Extreme care shall be taken not to overfill the refrigeration system. Prior to recharging
the system it shall be pressure tested with OFN. The system shall be leak tested on
completion of charging but prior to commissioning. A follow up leak test shall be carried
out prior to leaving the site.
7